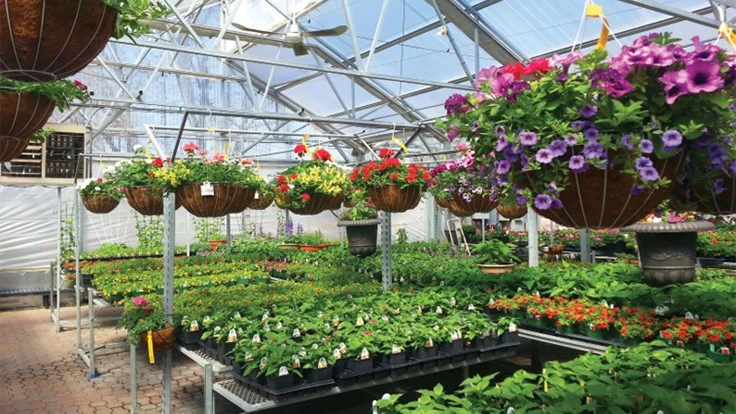

Greenhouses all across North America will be hammering away this summer as growers expand and improve their operations.
In Greenhouse Management’s 2019 Structures Report, a little more than 40% of respondents said they are planning to upgrade their greenhouse structures in the coming year, and about the same percentage said they’ll be adding production space by next spring. The majority are keeping expenses to $25,000 and under, with improvements ranging from new structures to technology updates to production areas for new types of plant materials.
Kopke’s Greenhouse in Oregon, Wisconsin, is making its first foray into hemp production this year. The 5-acre operation has about 2 acres under cover in two gutter-connected buildings, growing mainly annuals along with some perennials and vegetables.
But in mid-July, the company will be taking an existing quonset-style building and relocating it for organic vegetable and hemp production, which became legal in the state two years ago.
“We got our license for doing it this year and apparently so did every other person in the state. So we fully expect the market to bottom out within the next year or so and then it will be like corn or soy with everyone overproducing and nobody making any money,” says Vice President Josh Smith. “So our strategy is to get in and get out.”
Others, like Merwood Nursery, in Anchor Point, Alaska, are planning to expand and improve production of their existing crops. The company currently has two 24-by-120-foot greenhouses under construction to help shelter young plant material from the harsh climate.
“In the spring it’s very cold and the weather is pretty inclement here and [growers] complain that they have to move it outside to get it from greenhouse to greenhouse or from range to range,” says owner Michael Edwards. So I’m building passageways and corridors between all the houses that aren’t going to be gutter-connected so the plant material can stay inside until it moves out.”
Pipsypop Flowers in Lake Geneva, Wisconsin, has seen a huge demand for cut flowers, so they’re also planning to expand on their success. The 3-acre cut flower operation has about 800 square feet of greenhouse right now, and is in the process of adding another 500. In the spring, they’ll also be adding a couple of poly houses for seeding.
Rather than bring in outside laborers, the company is planning to handle construction in-house, custom-fitting polycarbonate around the frames they build.
That’s the plan at Merwood Nursery as well, where Edwards says it’s tough to find reliable, quality work. “It’s slow but it does cut down on the cost of labor,” he says. “Trying to find people that are qualified and do the job you need to get done is hard to find.”

Labor-saving strategies
Many of growers’ planned upgrades revolve around labor-saving strategies, whether it’s watering, transportation or environmental controls.
For 30 years, Kopke’s Greenhouse’s climate controls consisted of knobs and thermostats, but they’re in the process of replacing or upgrading to save some time and effort so that they don’t have to visit the greenhouse every time the sun comes out, Smith says. The operation already has automated controls in four of its 29 buildings so far, but due to issues with their vendor, they’re looking to replace or upgrade.
But it isn't a do-or-die situation. Kopke’s is at the point that they’re looking to shave off milliseconds rather than seconds off of production.
“We’re looking at some potential improvements in quality — not to say that we aren’t very pleased with what our growers do,” Smith says. “We just want to be able to augment them with tools that they can use to do even better. We feel like we nitpick nowadays rather than make big strides.”
At Merwin, Edwards is hoping to cut down on the labor it takes to move plant material around by installing a cart monorail system to move product throughout his two greenhouses.
“It’s so labor-intensive moving plant material — the trays, the individual pots — and so I want to cut down on labor that’s involved for the employees and myself in moving plant material around,” he says. “It takes so much out of your bottom line because every time you move stuff it costs you more to produce that individual plant or whatever you’re growing.”
Upcoming upgrades
Merwood Nursery is planning a dehumidifying system as well to help with ventilation in the fall and winter. The operation plans to install a sawtooth roof design with a 2-foot-wide vent that opens at the bottom. But in Alaska, the cold, cloudy days make moisture a real problem since ventilation translates to more heating costs.
The operation is currently using a biomass heater as the primary source of heat, and while Edwards would like to upgrade to natural gas, the price to build the pipes to connect would be around $62,000. He’s hoping that the natural gas company will build an infrastructure in the coming years, but in the meantime, he’s planning to install a propane heater for backup.
For now, he plans to keep on using thermostats to run vents and circulating pumps.
Other growers are sticking with what’s tried and true. Lasch plans to keep using the same system of exhaust fans, vents and thermostats that have worked for him for years.
“With the natural air flow going through there we really don’t use [exhaust fans] in the dead of the summer, so the heat isn’t as big of a deal,” Lasch says.
Next spring and summer, Edwards is planning to expand into a new perennial overwintering house, and after that, it’s on to a garden center building with an attached greenhouse for houseplants and tropicals.
And Smith says he’ll be upgrading on a case-by-case basis, working through what works for his operation.
“We don’t need the latest and greatest thing out there,” he says. “We try to do what makes sense and not let our eyes get to feasting on the desserts that are out there.”
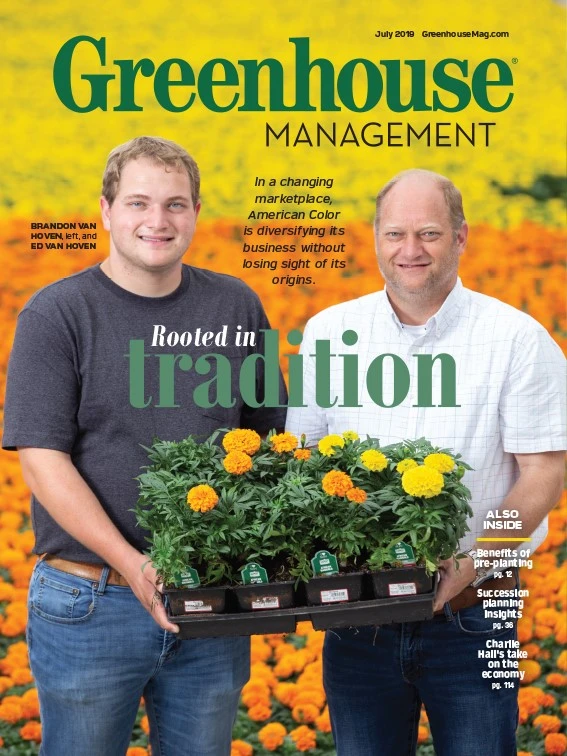
Explore the July 2019 Issue
Check out more from this issue and find your next story to read.
Latest from Greenhouse Management
- CEA Alliance celebrates bipartisan introduction of Supporting Innovation in Agriculture Act
- Dümmen Orange North America celebrating 25th anniversary in 2025
- Illinois Landscape Contractors Association changes name to Landscape Illinois
- 2025 Proven Winners Horticulture Scholarship applications now open
- ICL’s Gemini Granular herbicide now registered for use in California
- Eurazeo Planetary Boundaries Fund acquires Bioline AgroSciences
- Spring Meadow Nursery's Freedom Shelley finds joy in plants
- Leading Women of Horticulture: Dana Massey, Plantworks Nursery