
When fertilizer injectors are working properly, they reduce the potential for human error in applying nutrients. But when undissolved nutrients get caught in the system or other problems arise, it falls on growers to maintain them.
Well-maintained fertilizer injectors ensure that growers apply the correct amount of fertilizer, plant growth regulators, pesticides and sanitizers, says Lela Kelly, vice president of Dosatron International. “Your fertilizer injector is one of the most important pieces of equipment you own,” she says. “Take care of it as well as your car, or trucks. Schedule the maintenance to be sure it gets done.”
1. Check with the manufacturer.
One of the most important steps growers can take in troubleshooting issues with their fertilizer injectors is to check with their injector manufacturer about how and how often they should maintain the equipment, Kelly says. “Go to your fertilizer injector’s website,” she says. “Often you will find easy to follow instructions, and videos to guide you.”
Growers can clean their injectors to help extend the equipment’s life, and use maintenance kits to ensure it works correctly, Kelly says. They can visit their distributor’s website or call their fertilizer injector company to purchase a maintenance kit.
2. Follow fertilizer label rates.
As with other aspects of greenhouse growing, having to curatively treat issues with fertilizer injectors can sometimes be avoided by making correct fertilizer applications in the first place, says Bruce Walters, technology sales at H.E. Anderson Company.

“If I were the grower, the number one thing would be to make double darn sure that the fertilizer mixtures that I’m getting — that I’m blending in my mixing tanks — are at the labeled rates for the amount that I want to apply and held in solution so that they don’t fall out and create plugs in my irrigation equipment,” Walters says.
3. Perform maintenance during downtimes.
Even when growers follow accurate mixing protocols, undissolved nutrients such as calcium, magnesium and phosphorus can fall out of the solution, get caught in the water stream and clog spray nozzles, Walters says. “You could actually put in some tertiary screens — filters — to help if that were a problem,” he says. “But, boy, once something like that particulate hits those small emitters — misters — little spray heads — it’s a physical thing there, primarily, to get those cleaned back out.” In downtimes when growers are switching crops, they can follow “common-sense maintenance” practices such as cleaning out their lines with sanitizers, Walters says. Disassembling the equipment, he says, is often simple but time-consuming.
4. Properly calibrate the equipment.
Growers should use a calibrated electrical conductivity meter to monitor how much fertilizer they are injecting, Kelly says. “This is an easy way to know when to clean, and maintain your injector,” she says.
Calibration is important and should keep growers “on their toes,” Walters says. “You definitely want to be putting on what you want to be putting on, instead of just throwing a hand grenade out there,” he says. “You check that by making sure that your equipment is calibrated, that you’re mixing the solutions according to the labels and using them on the appropriate crops.”
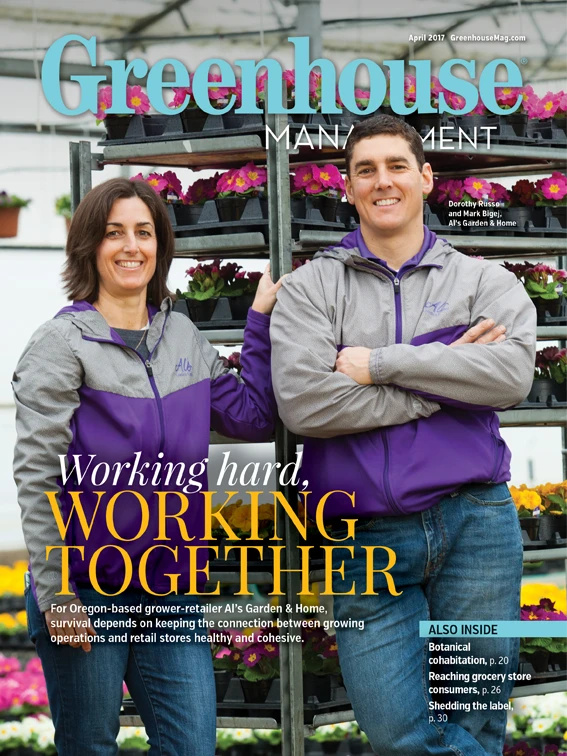
Explore the April 2017 Issue
Check out more from this issue and find your next story to read.
Latest from Greenhouse Management
- Hurricane Helene: Florida agricultural production losses top $40M, UF economists estimate
- No shelter!
- Sensaphone releases weatherproof enclosures for WSG30 remote monitoring system, wireless sensors
- Profile Growing Solutions hires regional sales manager
- Cultural controls
- University of Maryland graduate student receives 2024 Carville M. Akehurst Memorial Scholarship
- Applications open for Horticultural Research Institute Leadership Academy Class of 2026
- Meeting the challenge of pest management