
With the utmost respect to my colleagues in the gas and electric utilities, energy companies and the services they provide are frankly not the sexiest.
All too often, we treat them as simply a vehicle to get the power we need to run our businesses. In the controlled environment agriculture world, utilities are more than just companies that sell you electricity or gas. In fact, it is essential to have a proactive and open relationship with your utility providers. Being engaged with them will help you avoid pitfalls, and they can advise you about serious cash-saving opportunities.
Below are six key considerations to run by your utility provider.
1. Get input early.
During all phases of your facility’s development, your energy utility contacts, and their colleagues can serve as de facto members of your project planning team. As you conceive of and design your new space or expansion, you will need input from your gas and electric utilities to ensure that your site is able to meet your energy needs.
Similarly, if you are scoping out locations for a new facility, keep in mind that even those sites that appear to be adequately equipped with electric or gas service may not be able to meet your needs without additional infrastructure investment. Upgrades for electric service may range from simply having an electrician install a new panel to exploring with your utility adding three-phase power to your site. Natural gas infrastructure expansion will often include laying new pipe, the costs of which are driven primarily by the distance of your site to the nearest distribution system.It is equally important that, if you are interested in installing a power-generating combined heat and power (CHP) or solar-power system, you may be obligated to apply for an agreement with the utility to connect your equipment to the power grid.
2. Ask about loads and upgrades.
Energy supply upgrades can easily exceed tens of thousands of dollars. Not accounting for these costs early in your process could result in a painful surprise and will undoubtedly put a dent in your financial projections. Don’t just take the word of the real estate broker that the site is adequately served; a simple phone call to the local utilities will help you make an informed decision about your site location and ultimate equipment selection choices.
Key immediate utility items you will want to ask about are the maximum load that your site can handle without any upgrades, what upgrades will be necessary to meet your expected load, and whether natural gas is available at your location. The answers to all of these will be fundamental to your cost projections and equipment selection options.
3. Check for incentives.
As you consider the equipment for your new build or expansion project, your utility can be an important resource for grants to help you adopt energy-saving (and often performance-boosting) technologies. To the extent that state or local regulations allow, utilities may incentivize growers to purchase and install light-emitting diode (LED) lights, custom HVAC systems, environmental controls, and even technologies such CHP or gas-driven chiller systems that use natural gas to reduce grid-provided power. Some states, such as Massachusetts and Illinois, have energy regulations that mandate use of energy-efficient equipment in cultivation facilities. In these instances, the local utility may not be able to offer you a cash incentive to purchase and install these technologies. Your utility, or their assigned energy efficiency program administrator in some states, including Maine, Vermont and Oregon, should be able to share information about their specific programs.
But the onus will be on you, the greenhouse owner or operator, to learn about any relevant incentives and pursue the appropriate channels to get them. The good news is that there are professional energy firms who can assist you with the application process and maximize your incentive opportunity.
4. Estimate operating costs.
As your design moves forward and if it includes technologies that are eligible for a custom energy efficiency incentive, your electric and gas utility can be a good resource to help you corroborate your estimates of your ongoing energy-related operating costs. In a rush to build out projects, too many facility operators neglect to give adequate attention to ongoing operating energy costs.
However, because these costs are often among the first three items on a cultivator’s expense sheet, operators who ignore opportunities to understand and seek reductions in their energy use do so at their own peril. Before committing serious money on hardware, cultivators should have a very good sense of the total amount of power their desired equipment setup will require. Big items are lights and HVAC, of course, but don’t forget other items such as fertigation, fans and automation and processing equipment.
5. Track data.
As a best practice, constantly track energy usage throughout your facility. Analyzing your energy consumption data will help you diagnose potential aspects of your facility that are not performing properly or causing your overall energy productivity to drag. Furthermore, because of the strategic imperative to be a smart energy consumer, it is more essential than ever that you know how, where and when your facility uses power.
For example, a large percentage of your power bill may be made up of demand charges, which are determined by the height of your facility’s largest demand “spikes.” By using sub-meters in your facility that provide rich minute-by-minute energy-consumption data, you can better plan your power use to keep those spikes as low as possible. Even if you do not have sub-meters in your facility, your primary utility-owned meter should be able to provide you with facility-wide historical usage in 15-minute increments; many offer access to this information by enrolling in the utility’s optional “energy manager” or “energy tracker” program. Ask your utility if there are programs you can take advantage of to capture more data related to your energy consumption.
6. Consider rate changes based on demand.
Finally, your utility account manager can share details about how gas and electricity rate changes will affect your monthly bill. An ideal time to check in with your electric utility is in the spring, prior to the beginning of the summer cooling season when demand charges can increase to reflect higher demand on the power grid. Being in regular communication with your utility will also help ensure that you are on the rate that best matches your power usage and time-of-use patterns. If you are considering installing CHP systems, backup generation, or solar panels, your utility will also let you know how installation of those technologies will affect your rates and overall bills.
In summary, think of your utility provider as a friend, not foe. They can save you money by providing you with tools and resources to help you understand and track your energy usage, adopt energy-efficient technology and discover ways to reduce your power usage and costs. For your facility planning process, utilities hold key information about the technical requirements needed to provide your location with the electricity and gas services that your facility needs to produce your crop.
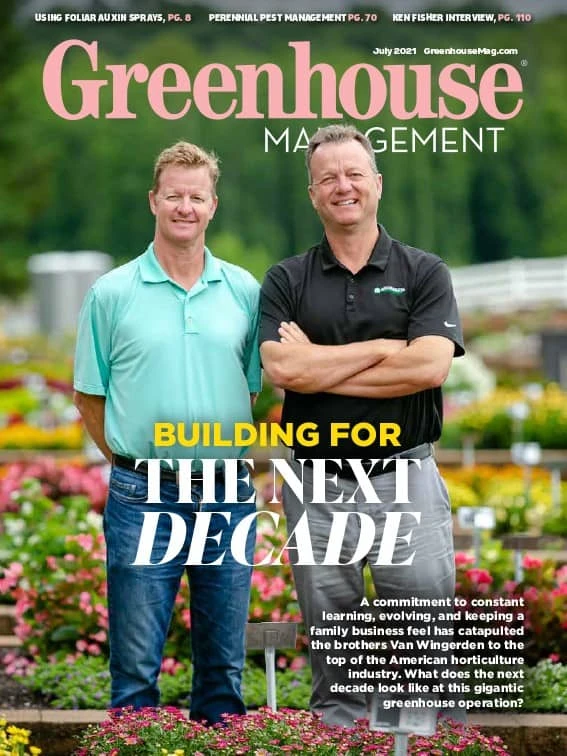
Explore the July 2021 Issue
Check out more from this issue and find your next story to read.
Latest from Greenhouse Management
- North Carolina Nursery & Landscape Association announces new executive vice president
- Plant Development Services, Inc. unveils plant varieties debuting in 2025
- Promo kit available to celebrate first National Wave Day on May 3
- Applications now open for American Floral Endowment graduate scholarships
- Endless Summer Hydrangeas celebrates 20 years with community plantings
- Invest in silver
- Garden Center magazine announces dates for 2025 Garden Center Conference & Expo
- USDA launches $2 billion in aid for floriculture growers