
At the C. Raker & Sons greenhouse operation in Litchfield, Mich., a researcher is hard at work in a 100-square-foot shipping chamber that’s been converted into a growing space. Paul Karlovich, director of research, has been trialing sole-source LED lighting with different crops in this shipping chamber since this past April.
Raker isn’t new to lighting — the company has been using high pressure sodium (HPS) supplemental lighting to extend the day length in its greenhouses for quite some time, Karlovich says. “We light our entire crop here in the wintertime,” Karlovich says. “We start lighting in October/November, and we end in March/April.”
But not all crops can be easily grown in the greenhouse, even with the use of supplemental lighting — and that’s where the growth chamber comes into play. “What I’m looking to do is grow crops that are difficult to grow in the greenhouse under normal conditions,” Karlovich says. “So basically, [we’re experimenting with] high-value crops that generally are hard to supply or [have] significant problems that cause a lot of waste in production in a greenhouse for whatever reason.”
Raker has been looking at growing tuberous begonia and gerbera in the chamber as a solution to the struggles they often face growing them in the greenhouse. “A tuberous begonia is a very slow grower and very fine rooted,” he says. “A gerbera is the same way; it’s very temperamental to very small issues in a greenhouse.” And when there are issues, growers lose product and money. Through this research, Karlovich is evaluating if they can improve productivity and speed up the crop time.
Why use a growth chamber?
In Litchfield, as in many other places in the Midwest, weather can be inconsistent at best, which complicates growing — even in a greenhouse. “The biggest problem in a greenhouse for any crop is the weather is different every day, at least in Michigan,” Karlovich says. “The sun comes out, it’s very hot. [Then] it’s cloudy today, [but] it’s going to rain tomorrow. Do I water? Do I not water?” To further complicate matters, these tasks are carried out by low-skilled laborers that often make mistakes. One of the advantages of growing in a chamber is the consistency of the growing conditions. Light, water, CO2, fertilizer and temperature can be strictly controlled, and the weather outside becomes irrelevant.
In addition, Karlovich sees an opportunity to eventually automate many of the processes in the chamber. At this point, people still need to enter the chamber to make sure the plants are up to count and progressing well. “But you almost wouldn’t need anybody if you had the recipes right,” Karlovich says. That is, once they find the best combination of light, water, fertilizer and other conditions to grow each crop in, labor needs would be reduced and productivity would increase.
Is it worth it?

The capital investment in a project such as this one is not insignificant, and growers should carefully consider the costs and benefits just as they would with any other greenhouse expense. In this case, electricity is the biggest cost that Raker is incurring. “Basically, you’ve got to look at all your costs and see if you’re going to make money out of it,” Karlovich says. “A lot of it has to do with whether we can be more productive or not. If we can’t be more productive, it won’t work.”
The evolution of LEDs in recent years has been a big part of why Raker has been considering them for uses such as premium crop production. It’s been made possible by “the fact that LEDs are much more efficient even than they were three years ago,” Karlovich says. “They continue to come out with lights that are more efficient; just in the last few months the latest LEDs are more efficient than HID lights, which is really a change. It hasn’t [always] been that way.” The possibility of controlling the light spectrum with LEDs in order to modify plant growth is also an attractive feature for Raker.
But overall, “It all comes down to economics,” says Karlovich. “These rooms have got to run year round. You can’t just buy these lights for your spring season. Raker is a year-round producer of products [and] have plugs growing every week of the year.” Growers who are growing a volume of high-value crops and have the market to get a better price point for them could benefit from a set-up like Raker’s. “To justify building a room, you really need to use it as much as possible,” he says.
However, Karlovich says that switching to LEDs isn’t in the cards yet for the main house, mostly because the HPS lights are still in good working order and get the job done. “If I needed new lights for whatever reason, I would look at [LEDs],” he says. “But to replace what you already have when it works — it’s not quite as easy [to justify].”
If other growers are using incandescent supplemental lighting and considering switching to LEDs, Karlovich says that it’s worth looking at for the energy savings. “The efficiency of the bulb alone will pay for itself fairly quickly,” he says.
Plans for the future
While the growth chamber research is in its early stages at Raker, Karlovich has given a lot of thought to how he’d like to see the project progress. “I’m hoping that we can do six or eight layers of plug production [in the 15-foot-tall chamber],” Karlovich says. He has “a whole series of experiments planned,” and plans to keep the chamber up and running for the foreseeable future to see how it can be best utilized.
Karlovich is also seeking out different crops that can be grown year-round in order to get the maximum return on the chamber and keep the facility up and running 12 months out of the year. “The economics are, in the end, going to make it or break it,” he says. “I need to have a year-round facility.”
“We’re very happy with the initial results [of the growth chamber and LED lighting],” Karlovich says. His advice to other growers considering undertaking a project of this type? “The challenge is not growing, believe it or not,” he says. “The real challenges are the efficiencies and how you work in them, and making sure that it’s profitable. But I wouldn’t be doing it if I didn’t think there was opportunity — I think there is.” As the home lighting market develops and drives costs down and lighting efficiencies up — especially for LEDs — the horticulture market will benefit. “I think it’s a good time for Raker to get involved in it, be an early adopter, figure it out,” Karlovich says.

Over the past 25 years, Battlefield Farms has innovated and invested in technology to maintain a strong business and weather economic downturns. In recent years, Battlefield has been focused on lighting, including trialing and implementing LED lighting in different growing areas. The company already had experience using high pressure sodium (HPS) lights in the greenhouse for some time for supplemental lighting or night extension. Typically, “We grow fine with the light levels that we have during our seasons,” says Travis Higginbotham, research and development manager. But there were specific areas where they believed LEDs might improve production, especially in tissue culture propagation.
In order to satisfy future perennials orders, Higginbotham says that they needed to propagate in the greenhouse during a time of year that wasn’t ideal. “The problem that initiated the [LED] research was [we were propagating] during the summer when conditions were too hot and light levels were too intense,” he says. This led to losses, inconsistencies and increased labor needs.
Moving indoors

The team decided to move their tissue culture propagation into a room with a controlled environment that utilized a sole-source lighting system about two years ago. “We used LEDs mainly for the efficiency, and then from that we started to realize we can actually manipulate the spectrum with LEDs and get a specific response out of the plant,” Higginbotham says. “That was a big benefit for us, not only for energy efficiency but also, we can keep plants from flowering, we can keep them from elongating with just applying blue and red wavelengths, and that helped us get well-rooted, compact plugs — which is exactly what we wanted — and on average cut about a week off of grow time.”
Battlefield produces between 400,000 and 600,000 perennial liners a year in the controlled environment room, and it’s been worth it. “The entire room [was] paid off in two years,” he says. Labor needs were also reduced, as finishing times are more consistent now and there’s less need for workers to remove and replace partially rooted trays. Ideally, they would be utilizing the room year-round, Higginbotham says. But even if it’s not, it’s still a worthwhile resource with good ROI.
Look for solutions and educate yourself
At Battlefield, they’re seeking to solve problems with this technology, Higginbotham says. Growers who are considering investing in LEDs need to understand the differences between the lighting types, such as intensity, spectrum and heat emission. “[You] certainly need a trial yourself and to have a specific objective,” he says. “Make sure you have a control, trial it yourself, have the right tools to measure light and educate yourself on the spectrums you’re using. Have some really good personal experience and data before making the investment.”
Higginbotham educates himself about lighting using a range of sources, including lighting manufacturers. “They’re having to get a decent bit of research behind a lot of the modules, mainly due to the investment cost [for growers],” he says. “So they’re able to really help us look a bit deeper into light.” Higginbotham also reads scholarly literature coming out of Purdue, Michigan State, Cornell and others, attends webinars and works with experienced technical consultants to keep himself up-to-date.
A bright future
Higginbotham is excited about the possibilities of LED lighting at Battlefield. “It’s fascinating what you can do with an LED,” he says. “Right now you can get perfect growth [and] adequate supplemental lighting with HPS, but you have the environmental factor to look at. Now we have the ability to cut back on energy, [and] manipulate [the plant] with different spectrums of light. That’s the benefit of LEDs.”
Building on the success they’ve had with the sole-source lighting in the controlled environment with Stage III tissue culture, Higginbotham is running tests using multiple light spectrums and intensities on seeds and cuttings to see if he can speed up propagation, rooting and finish time, improve germination and overall consistencies.
He recently conducted a trial that compared incandescent lights to LED lights in night interruption photoperiodic lighting of perennials, namely echinacea. “We had incandescent lights [on] just enough so that the plants could perceive the photoperiod, and we ended up getting even better growth with just the night interruption from the LEDs,” Higginbotham says. “I equate it to the spectrum that was being applied, because the intensity was the exact same.”
Currently, Higginbotham is experimenting with putting LEDs on their irrigation booms for night interruption. “I’m just trying to see what other options we [have] with those same lights as well as [try] a few little things like on boom lighting,” he says. “We’re [also] seeing if we can try a few different [lighting] modules out that are just coming on the market.”
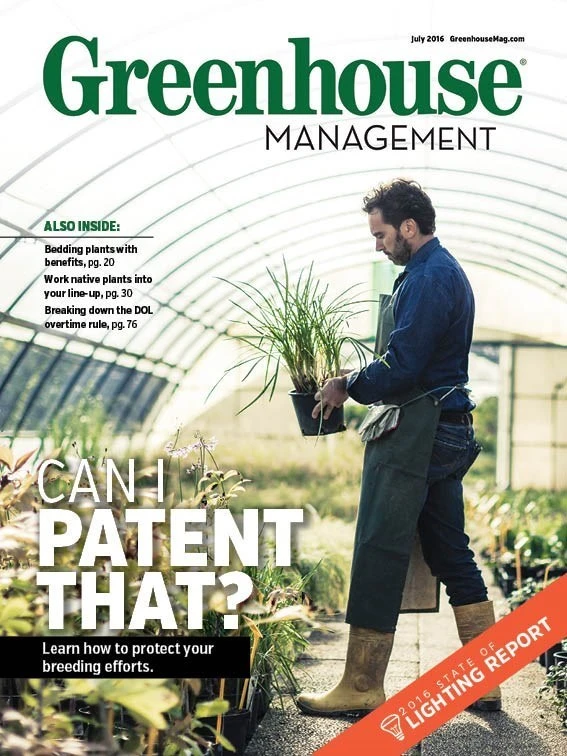
Explore the July 2016 Issue
Check out more from this issue and find your next story to read.
Latest from Greenhouse Management
- Flexible fungicides
- Super Charged Moon Juice from Moon Valley Nurseries now available nationally
- 2025 Proven Winners Horticulture Scholarship applications now open
- How to improve inventory and shipping management in the greenhouse
- Leading Women of Horticulture: Anna Ball, Ball Hort, and Terri McEnaney, Bailey Nurseries
- GM CEA HERB Part 2: A guide to increasing the sowing density of culinary herbs
- GM CEA HERB Part 1: Best practices for producing culinary herbs in controlled environments
- USDA fires experts on invasive pests, including Asian citrus psyllid, chilli thrips