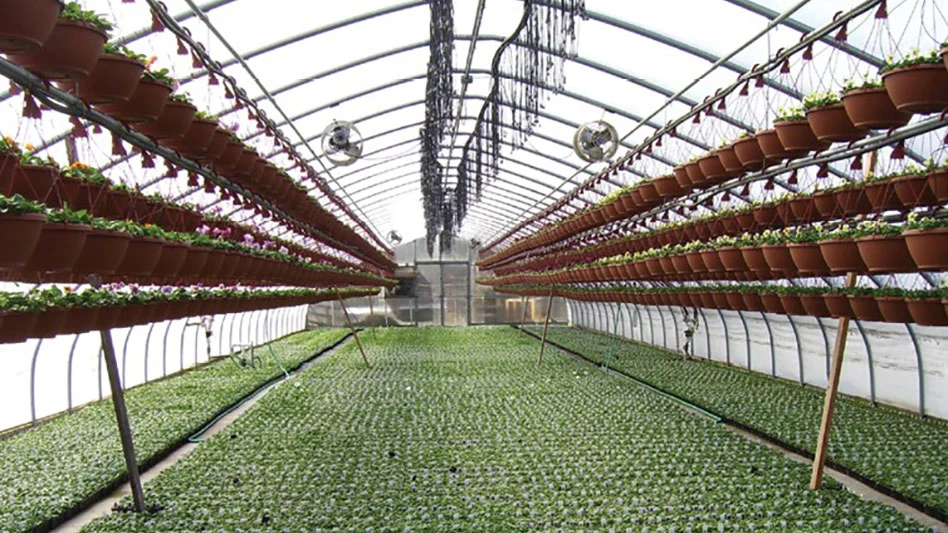

Production of hanging baskets has increased significantly over the past few years. Many homeowners enjoy the large variety of colorful plants available without the chore of planting.
Growers also benefit in that they can utilize additional overhead space in the greenhouse to realize additional income without increased cost for heat. Maintaining the correct level of moisture in the container can be a problem as the plants are out of reach where they can be checked easily.

Hand watering with a hose and wand is typical for the small grower with a hoophouse or two. If you have more than that, then installing a watering system will save considerable labor.
Inline drip or micro tube systems can work well, but they have some disadvantages that can affect plant growth. Overwatering or underwatering is common. Also, all baskets receive the same amount of water whether they need it or not.
Hanging basket conveyors can be installed to reduce labor. Manufacturers include Cherry Creek Systems, which makes the Echo; GTI Inc., which makes the Boomerang Basket System; and Control Dekk, which manufactures the Oasis watering system.
Walking is eliminated and watering is automated. Hanging, removing and maintenance of baskets can be done at one location, usually on an end cross aisle.

The most common system utilizes a horizontal drive cable stretched between two drums, one at each end of the greenhouse bay attached to the bottom truss cord. One or more levels of baskets are supported by hangers along the length of the cable. The diameter of the drum, typically 20-50 inches, determines the size of the basket that can be hung and the amount of light that can get to the lower-level plants. The cable is motorized and controlled with a variable speed gear motor on one of the drums. This provides low speed for watering and faster speed for hanging and removing the baskets. The bay length of the system can be up to 250 feet.
Typically, basket conveyor watering is done by a system located at one end that applies water for a predetermined number of seconds as each basket passes by a water supply tube. The speed of the conveyor and size of the basket determine how much water is applied. Each pot gets the same amount of water. This does not allow for moisture variation between baskets.
A recent development by Control Dekk can vary the amount of water applied by weighing each basket as it passes by the watering nozzle. An optic sensor determines if a basket is present. A weight sensor determines the weight of a basket and then calculates how much water is needed. This reduces water waste and chemical use. It also helps to reduce basket variability and provides greater uniformity of all baskets on the line. The system can be added to most existing conveyor lines.
The operation of the system and the condition of the plants can be observed on a color touch screen at the end of the line. Multiple lines of plants can also be easily monitored remotely on a smart phone, tablet or computer screen in the office. The ideal basket weight can be easily programmed. Some growers program the system to water before their employees come to work in the morning. Plant moisture level can be observed by the optic sensor.
Hanging basket watering is a task that can be easily mechanized. It will save labor and do a better job than hand watering. The payback is short if you grow large numbers of baskets.

Explore the June 2023 Issue
Check out more from this issue and find your next story to read.
Latest from Greenhouse Management
- North Carolina Nursery & Landscape Association announces new executive vice president
- Plant Development Services, Inc. unveils plant varieties debuting in 2025
- Promo kit available to celebrate first National Wave Day on May 3
- Applications now open for American Floral Endowment graduate scholarships
- Endless Summer Hydrangeas celebrates 20 years with community plantings
- Invest in silver
- Garden Center magazine announces dates for 2025 Garden Center Conference & Expo
- USDA launches $2 billion in aid for floriculture growers