

Growing media (substrates) have been in the news a lot over the past year, mostly covering the usage and availability of peat as well as peat alternative substrate materials that are being investigated and adopted by growers. While these conversations are timely and warranted, there are other sectors and types of growing media, namely bark substrates, that are also evolving in their uses and formulations for many traditional and “new” specialty crops produced in soilless container systems.
Biochar and wood fiber are two substrate components (Figure 1) that are seeing more use in bark mixes for the ornamental nursery industry, as well as many soft fruit production systems. These two materials are probably not new to most folks at this point, as they have been heavily researched and publicized over the past decade, but there remain a lot of questions as to “why, when and how” they may be advantageous to use in bark mixes. There are numerous reasons why growers may choose to modify their growing media, and those reasons can vary from grower to grower. Some reasons include:
- unstable or unreliable supply chain of existing substrates;
- recent cost increases;
- preference to use more local/regional substrate materials;
- more stable substrates for long-term crop production;
- use of more sustainable/renewable substrate materials;
- better nutrient and water use efficiency;
- new/modified substrate that better performs in the specific growing system and irrigation delivery system they have;
- new or modified mixes that improve or increase shelf life (wilting) of plants in garden centers, etc.
The buzz about biochar’s use in soil and in soilless substrates seems to be at an all-time high. The body of scientific data (globally) on the many potential benefits and uses of biochar (and similar materials) is quite staggering. While most of the research and commercial use is on field soil application, it cannot be overstated how much work, by so many, has been done to investigate its potential in growing media.
One of the main over-arching benefits of making and using biochar is the ability to sequester (lock up) carbon, thereby not allowing it to be released in the atmosphere — a key element of global warming and climate change. Another tremendous advantage is that biochar can be made from almost any organic biomass/waste material, thereby removing it from waste streams. A quick review of the published literature from the past eight years found more than 70 unique organic biomass materials have been made via pyrolysis, gasification, flash carbonization, torrefaction or other thermochemical techniques.
It is well known that the type, quality, sourcing and consistency of the feedstock material used to make biochar, as well as the process used to make it, all contribute to the quality and consistency of the biochar end-product. The most touted benefits of biochar’s use in substrates, other than sequestering carbon, are its stability (does not degrade for a very long time), remediation of toxic pollutants, high porosity, high cation exchange capacity (nutrient holding) and reusability. Some readers may remember the use of bark ash in mixes, which I suppose could be considered the precursor to biochar today, even though they are not the same materials but do have some similar properties and benefits.
While our understanding of the science behind biochar and its benefits continues to improve, one of the most impressive advancements in the past two to three years (in my opinion) is the efforts made by so many to improve the process of making the material(s). For many years early in the exploration of biochar, I and many others often referred to biochar as being a verb (process) more than a noun (product) due to the variability in the materials from batch to batch or across production systems. Variability in the chemical and physical properties of any substrate component can greatly limit its adoption and use — and of course price.
Today in the U.S., there are numerous companies specializing in the production and sale of biochar for agriculture. My lab has worked with several of these companies and their products, and we have seen the vast improvement in the quality and consistency of the materials now being made. This is in part due to new processing technologies as well as investments by some in multi-million-dollar machines to make the material. The range of biochar products available on the market today is impressive and continues to grow (Figure 2).


The addition of biochar to bark (pine in the eastern U.S. and Douglas fir in the west) substrates has some potential advantages. First, the high CEC of biochar can aid in nutrient retention and reduced nutrient leaching in outdoor container production systems. Some research suggests the inherent nutrients in biochar are also beneficial to crops and can reduce certain fertilizer applications, but this is variable and unreliably consistent to be the main reason for adding biochar. The second benefit — with more likely potential — is the use of biochar in bark mixes for large containers for crops that will be grown or kept in pots for multiple years. Due to the resilient biostability of biochar and its resistance to degradation, it can greatly aid in the long-term structure (water, air and drainage) of substrates for longer than bark alone.
The biggest limitation or hesitation to using biochar that I see and hear from growers and substrate manufacturers is the cost. As mentioned earlier, there must be a beneficial reason to the grower for using new substrates or substrate components. Most reasons can fall into one of two categories: lower costs of a substrate to save money on the front end, or some proven value-added benefit to production costs (i.e. water or fertilizer savings) and/or improvement of plant growth/performance/shelf life of crops. I do believe that commercial biochar costs will eventually get to a place where growers are more inclined to adopt it on a wider scale, but until then, the availability and economics of bark substrates currently compared to biochar make it a difficult decision for many, unless of course someone makes their own or finds a local source that is reliable and economical.
Wood substrates, now widely accepted as a component that is here to stay, have experienced steady increases in their development, commercialization and use across North America and around the world. Some may remember when conversations about the use of processed pine trees as a substrate began in the U.S. around 2005. These early research reports and presentations took the main stage at the annual Southern Nursery Association (SNA) meetings, and the public response was, well, let’s just say “not overly optimistic” from many folks. Understandably, it has been taught and believed for decades that you can’t grow plants in fresh wood. However, with the future supply and availability of pine bark facing an uncertain future at that time, researchers and growers alike were open-minded to new substrates in the event bark was no longer available. In the 20 years since then, wood products have become a mainstay in many substrates produced and sold today.
Nursery growers have been using sawdust and wood shavings as components in their propagation and production mixes for decades, well before any commercial products were on the market. The use of sawdust and shavings continues today by many growers, but now that there are numerous types, sizes and brands of engineered wood fiber on the market, more growers have taken advantage of using them. Thanks to new processing technologies for making wood fiber (mostly borrowed or modified from the pulp and paper industries), we now have wood components with a wide range of particle shapes and sizes: granular small particles that are flowable as well as short fibers that work well to make propagation mixes, thin long fibers that hold lots of water, coarser fibers that have more structure and drainage, etc. (Figure 3).
As an indication of the expansion of wood fiber production and use in the U.S., five years ago, there was one main company making and selling wood substrates. Today, there are at least five, with more coming soon. Additionally, many smaller companies and individual growers are making their own wood substrates (mostly with hammer mills). Many more are interested in doing the same, and they have good reason to pursue that. Globally, in 2017, there were fewer than 10 wood substrate processing facilities in the world. Today, there are more than 40, and the number is expanding rapidly.
The addition of wood fiber to bark, depending on the size/type chosen, can either add more drainage and long-term stability to the substrate or add more water-holding capacity. Wood can be used to extend bark supplies, something that is not practiced much today due to the availability of bark in most areas of the country, or be added as a cheaper option in places were wood can be made or sourced cheaper than bark substrates. For most bark substrates for container production, wood products that are coarse enough (in size and structure) to be easily blended with a front-end-loader or existing mixer are likely preferred (materials made with hammer mill or extruder) due to convenience and cost.
Will biochar or wood replace bark substrates? No, I do not believe that will be the case, barring any unforeseen event or situation where bark is not an option. Can they offer options and potential benefits to growers and their crops? Absolutely. Every grower and operation is different, but with more substrate options available, there is more security in the future of substrate supplies.
Read the rest of the State of Growing Media Report:
Automation: Preparing for potting automation
Sponsor Message: Premier Tech's commitment to growing media advancements drives innovation
Get curated news on YOUR industry.
Enter your email to receive our newsletters.
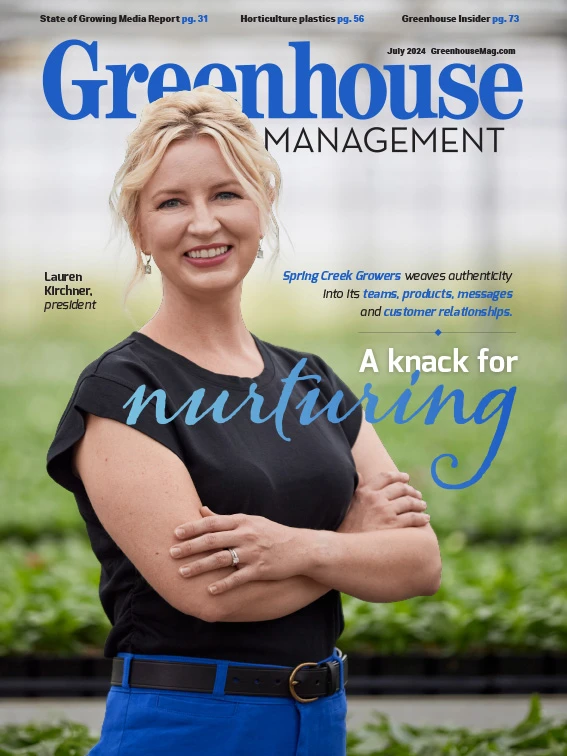
Explore the July 2024 Issue
Check out more from this issue and find your next story to read.
Latest from Greenhouse Management
- Flexible fungicides
- Super Charged Moon Juice from Moon Valley Nurseries now available nationally
- 2025 Proven Winners Horticulture Scholarship applications now open
- How to improve inventory and shipping management in the greenhouse
- Leading Women of Horticulture: Anna Ball, Ball Hort, and Terri McEnaney, Bailey Nurseries
- GM CEA HERB Part 2: A guide to increasing the sowing density of culinary herbs
- GM CEA HERB Part 1: Best practices for producing culinary herbs in controlled environments
- USDA fires experts on invasive pests, including Asian citrus psyllid, chilli thrips