
“Paper or plastic?” asks the grocer. If only the choice in greenhouse coverings could be so simple. Greenhouse growers have many variables to consider before they make a substantial investment in a greenhouse covering, such as crop type; light diffusion and transmission; the R-value (insulation measurement) of the covering; to allow or not allow ultraviolet (UV) light; and geographical location. And
in the ever-changing business climate we’re in, it’s important to consider just how long you plan on being in business producing a particular crop.
“You need to weigh in a lot of factors,” says Jess Roethle, corporate facility manager at Floral Plant Growers in Denmark, Wisc. for nearly four decades. “Things have changed over the last 40 years. Ask yourself, ‘What is my payback and how long will I own this business?’”
Understanding these considerations for coverings will help you choose the appropriate greenhouse glazing and possibly save money in the long run.
Energy considerations
Next to labor, energy is the biggest cost greenhouse growers face. Northern growers need to fire up their greenhouses in late winter and early spring. This pretty much rules out glass as a covering, which lets in maximum light, but doesn’t insulate against the cold very well. For this reason, Floral Plant Growers, with locations in four different states, has chosen to use double poly in their northern houses.Six mil double polyethylene is essentially the standard minimum thickness, according to Rick Hannigan, of Warps, a producer of various plastic products based in Chicago. It has an R-value of 1.4, when doubled up and inflated, while 8-mm twin-wall poly bumps the R-value up to 1.5. (The R-value is a scale that evaluates the thickness of insulation. The lower the value, the less the insulation quality.) Of course, the thickness of the material will also mean less light entering the greenhouse. Growers need to decide what is more important, heat retention or light transmission, which will be largely determined by the crop grown, climate, and time of year it is being grown.
Polycarbonate and acrylic have better R-values, hovering around the 2.0 range for both, depending on the thickness of the material. Finally, glass, which allows excellent light transmission, has a low R-value and is all but impractical in the northern region, especially with commercial growers.
Light transmission and diffusion
Polycarbonate and polyethylene will block out approximately 10 percent of light per layer, according to Debbie Remblence, sales director with International Greenhouse Company in Danville, Ill. In most climates, 80 to 90 percent of light transmission is sufficient for good growth.
Shading, in the form of knitted or cloth-type curtains, is often applied during peak seasons of sun and hot weather and for shade loving plants.

“Seventy to 80 percent of growers can spray a liquid shade on their roof, and most do,” says Nick Holubowski, Greenhouse Project Manager with Evonik Cyro Canada, Inc. “Some remove the shade product in the fall to allow in more light,” he says.
The topic of light diffusion is currently the buzz in the industry, according to Holubowski. While not new, it is nevertheless garnering a lot of attention as growers seek to purchase a glazing material that will be most cost effective for their crop.
Diffused light scatters light throughout the house and reduces shadows caused by the greenhouse framing materials.
All glazing products —polyethylene, polycarbonate, glass and acrylic, can be manufactured or treated to diffuse light.
Growers should know the capability of a covering to diffuse light before making a purchase.
Coverings life expectancy
The old adage, “You get what you pay for,” certainly applies to greenhouse coverings. Expect about a four-year life expectancy from poly plastic, 10 years and possibly longer from polycarbonate, and up to 30 years with acrylic — a material that, unlike polycarbonate, won’t yellow over time. Glass has the longest life expectancy, but is most prone to damage, Remblence says.
Each of these materials increase with cost proportional to longevity. As mentioned earlier, greenhouse growers need to consider how long they will be in the business before they take the leap into some of the more expensive, albeit longer-lasting coverings.
“Warranty aside, with polycarbonate you can almost guarantee an effective usefulness of 15 to 20 years before replacement,” Remblence says. “Polyethylene can often last only two to three years if it is prone to winds or external elements … and lead to tearing.”
Polyethylene — the largest selling greenhouse covering in the commercial industry, according to Remblence — is currently going for about 12 cents per square foot, while polycarbonate runs approximately $1.65 per square foot.
Growers should also be mindful of potential for extremes of weather, such as the extended period of snow and high winds in the Boston area this past winter that destroyed some greenhouses. This should be a factor to consider, not only from the standpoint of what type of covering and structural supports to purchase, but how to position and protect houses against the elements.
“Depending on the snow event you get you have to pay attention,” Roethle says. “Shovel it off or burn a little heat.”

Bubble wrap
A fairly new covering to U.S. markets, one that a number of key industry leaders are starting to use, features a heat-trapping plastic that resembles bubble wrap. The German-designed product was engineered to both insulate against heat loss while diffusing light inside the house. It is being touted as being more resilient to winds, hail storms and snow loads, having a 120-pounds-per-square-foot snow load rating and 100-mph wind rating. The structural framework of the greenhouse will contribute to the overall resistance to the forces of nature. The bubble wrap type covering has an R-value of 1.71.
UV Light Transmission
Ultraviolet light transmission (UV) is traditionally thought of as a negative for greenhouse growers due to its degrading effects — not only on glazing materials — but also components within a greenhouse, such as irrigation and electrical equipment. Some growers, however, welcome UV light because it contains the spectrum that is found in natural growing conditions.
By allowing UV light to enter a greenhouse, you have the best of both worlds: a protected growing environment, and the same light spectrum found outdoors. Holubowsky says some companies in the green industry have used glazing materials that allow UV light transmission, including acrylic products specifically designed to transmit UV rays to allow natural lighting for their breeding and test plots.
Holubowsky also says that botanical gardens and zoos use UV light emitting glazing because it keeps reptiles and other animals alive and healthy longer. It begs the question: Would biological pesticides and other controls, such as beneficial insects and even bacteria stay alive longer and be more effective in greenhouses that allow UV light transmission?
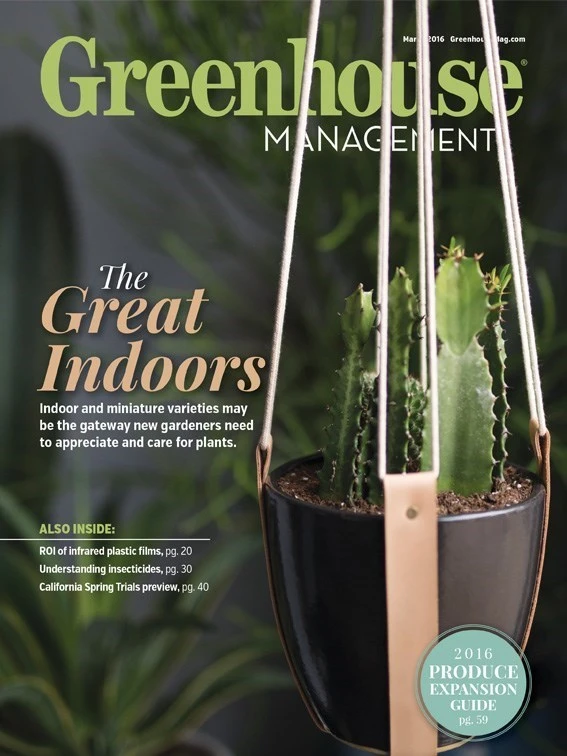
Explore the March 2016 Issue
Check out more from this issue and find your next story to read.
Latest from Greenhouse Management
- BioTherm launches the Ultimate Grower Climate Control System
- Jess Lyga joins Bailey sales team
- Happy holidays from the GIE Media Horticulture Group!
- North Carolina Nursery & Landscape Association announces new executive vice president
- Plant Development Services, Inc. unveils plant varieties debuting in 2025
- Promo kit available to celebrate first National Wave Day on May 3
- Applications now open for American Floral Endowment graduate scholarships
- Endless Summer Hydrangeas celebrates 20 years with community plantings