

It’s the middle of December. Snow is on the greenhouse roof. The weather is frigid and the growing season is almost over. A well-deserved break is just a few days away.
But the entire greenhouse is still bustling, still humid and muggy as poinsettias and other holiday crops are being finished. Once the plants are ready to serve as a centerpiece of the table or the lynchpin of a home’s holiday decorations, they’ll be placed carefully into trucks to be shipped out to nearby big box stores, independent garden centers or perhaps the grower’s own retail shop down the road.
Some of those plants, though, serve a special purpose. Those plants then travel to nearby churches, schools, sports teams and other groups that have sold the plants as fundraisers. And for many greenhouses, doing fundraisers is a core part of the business and represents a main source of revenue.
Growing for fundraisers, though, can be a challenging exercise for operations. For one, there is no easy way to know exactly how big each fundraiser will be and how many of each plant will be needed. There’s also the question of pricing — should it match wholesale or retail pricing, or should it be marked at a different rate? And how can a grower prep without knowing final order sizes when the growing season starts?
“There’s no good way to plan,” says Tim Holliday, head grower and wholesale manager of Roebuck Greenhouses in Roebuck, South Carolina. “You never know what trend is going to hit year-to-year.”

“It can be a hard place to be in."
Galema’s Greenhouse, located in West Lafayette, Indiana, sells its plants to almost every corner of the industry, from fundraisers to landscapers to their own retail store. Growing in around 70,000 square feet of greenhouse space and about 20 acres outdoors, the business produces everything from young plants to poinsettias to mums and some vegetables.
According to Bev Galema, who runs the business alongside her husband, owner and founder Tim Galema, no part of the business is more chaotic than the fundraising part of the business.
“It can be a hard place to be in because if they order a pink plant and we don’t have that for whatever reason, they aren’t going to want a red one,” she says. “So, to balance what I can offer that’s unique and have enough on-hand, because it is a perishable product and I can’t grow more, is tricky.”
Galema’s was founded by Tim in 1991, a few years after he graduated from Purdue University. He had worked for a greenhouse operation and gone back to Purdue to work in a lab, but Bev says Tim had been unhappy and wanted to get back to growing. That’s when the greenhouse that had previously employed him was put on the market.
“So we looked at them and he said, ‘I helped build them. I know what’s wrong with them and how to fix them,’” Galema says. They leased some land on Tim’s grandfather’s farm and started building the business little by little. In the beginning, Tim was still working part-time at Purdue.
“That developed into one more thing and one more thing and now we’ve got space I can’t keep track of,” Bev says with a laugh. “I have a degree in accounting [from Purdue] and actually worked full time before we had kids. And then this became my full-time job.” The Galema’s three children, as well as Tim’s parents, all work for the business.
Fundraising, she says, has been part of the business almost since the beginning and accounts for roughly 10 to 15% of Galema’s overall sales. The business grows mums for fall fundraisers and poinsettias for winter ones.
“We started with small growers, so we understand the needs of small growers and know the needs of small people,” Galema says. “We are flexible to handle the needs of more hands-on people. Not everybody wants 10,000 of one thing. And even if they get 100 of one thing, they don’t want 100 of the same color.”

Fundraising for Galema’s follows that same ethos. According to Galema, the business does fundraisers with different organizations across the state with no real criteria for what kind of group can purchase Galema’s plants for them. For instance, the greenhouse began growing for around 12 fundraisers for different travel softball teams in the area after an initial team signed up. From there, word got around.
One challenge now, Galema says, is growing for fundraisers correctly without overextending the business by taking on orders that could leave the business short on plants. She says the greenhouse space is about full, so committing more space for a winter poinsettia fundraiser just isn’t an option. And even then, there is still the challenge of being able to give customers exactly what they ordered.
“For poinsettias, one thing people like that can be hard to find are Jingle Bells poinsettias, which have generally not been in a box store,” she says. “But because I can’t find it anywhere else, I can’t go to my fellow growers and ask for 50 more because the fundraiser over-ordered. So, in the past year, we have been trying to shift our customers to give us [final totals] at least two weeks ahead.”
Roebuck Greenhouses started growing for fundraisers in the late 1990s. According to Holliday, the business started working with fundraisers when a friend asked him to do one for a local middle school. From there, they developed their own brochures and started to grow that side of the business. Fundraisers take place in the winter for poinsettias and in the spring for hanging baskets.
Roebuck used to grow for big box stores like Kmart, Lowe’s and Walmart before many of those stores began sourcing all their plants from one greenhouse producer.
“We had to change our business model, so we started focusing more on the landscapers, the independents and the fundraisers,” Holliday says. He started at Roebuck in 1990 and the business only shifted hard away from big box stores in 2006 just before the Great Recession.
Currently, Holliday says fundraising accounts for around 30 to 33% of Roebuck’s overall sales from the 200,000-square-foot greenhouse. He expects that part of the business to continue growing too but says it’s the most stressful part of the job.
“It’s terrible; I’ll be quite honest with you,” he says. “The little bit of hair I have left, I’m about to pull out. We aren’t taking orders — we’ve committed to this school civic group or whatever — and their numbers are still coming in. And right now, I’m oversold based on paper. You need a good backup plan.”
“It’s one and done, and I don't have to keep after them."
Currently, Galema’s offers its fundraiser customers the same price it does its wholesale customers. According to Galema, they’ve done that for years and had no reason to do it differently until recently.
“We haven’t changed it yet,” she says. “As we get more into this and we talk to more people, we have learned that isn’t always the case.” In 2020, Galema’s could raise prices for fundraisers, although not by more than a few percentage points.
Galema says the business is still profitable charging wholesale rates. There is more uncertainly with the process, she says, but it is also a one-and-done sale. By comparison, the ongoing relationship with retailers is sometimes an ongoing negotiation.
“You’re really selling to retailers every single week,” Galema says. “You’ll call them and tell them they need to take the gerberas this week because they are blooming like crazy and they’ll fly off the shelves and they’ll say, ‘I don’t want gerberas.’ So you’re constantly in that sales mode with retailers because they are ordering what their shelves look like, regardless of how good mine look. A fundraiser is going to take them because they already ordered them.
“It’s one and done, and I don’t have to keep after them,” she says. “It’s a different mindset.”
The real key for pricing fundraisers correctly, Galema says, is finding the right balance between the different parts of the business. Each part of the business supports the other, so if there’s a rainy spring and retailers aren’t ordering as much as expected, fundraiser orders can help make up lost sales. The inverse can be true if there’s a shorter poinsettia season.
She also notes that the different parts of the business can be reliant on different crops. For instance, Galema’s would probably stop growing poinsettias altogether, she says, if two large fundraisers went away in the winter. Without the fundraisers, the profit margins are not there to make growing poinsettias worthwhile.
For Holliday, the idea is to at least break even on a fundraiser. Prices are typically set at a point where the business can either make profit — particularly on volume sales — even if extra plants must be purchased from other growers at the last minute to fill orders. His prices per plant are slightly lower for fundraisers because the volume is likely to be there. His customers, 90% of which are schools, will regularly have $3,000 orders, whereas some IGCs are buying a maximum of $1,000 worth of plants.
Right now, Holliday does not have an order minimum, which it means there can be orders that are so small that Roebuck can’t make any money on them, but he’s considering changing that.
“I’ve been hung out to dry a few times this year where someone is three hours away and their fundraiser total is $300 and I’m sitting there thinking this is going to cost me $300, so it’s not even worth it,” he says. “But you never know. That small sale may be their first sale and the next year could be bigger.”
This year, Galema’s started using a program called Farmraiser to manage its orders. Schlegel Greenhouse, an operation in Indianapolis, recommended it to Galema’s and has used it for years. Farmraiser works by having the orders placed and processed online instead of via paper slip. The streamlined process also means there’s no chance cash or checks are lost in the process.
Farmraiser does take 10% of the gross sales from the fundraiser. The platform, though, allows the organizer to set the price for each item after the supplier sets a price based on what revenue they need out of it. The supplier can also set a maximum for a certain product — say a Jingle Bell poinsettia — so fundraising organizers can’t order in excess.

“It controls some of that unknown."
The first Galema’s customer to use Farmraiser was a fundraiser run by Bev and Tim’s daughter’s school band, who agreed to do it through the platform after Bev mentioned it.
“I got to see it from both ends, how it works,” she says. “They’ve got some kinks to work out, but I think it’s going to be a good platform. It gives me an ongoing report of what’s being ordered and then spits out specific orders of who ordered what.”
Galema also tries to only work with customers they’ve worked with in the past. Additionally, she says it is important to ease in any new customers by limiting what new customers can offer in a fundraiser. It’s also important, she says, to know what plants can be sourced from another operation if substitutions need to be made at the last minute.
Substitutions are a trick Holliday uses as well and he’s upfront with fundraisers to let them know that sometimes a change must be made. Roebuck only produces 35,000 to 40,000 poinsettias each year, so a larger grower nearby often will sell him enough to fill orders that Roebuck can’t with what’s on hand. He also limits the choices for poinsettias to 6” and 8” red, pink or white poinsettias.
Typically, he says, customers are interested in supporting the fundraiser as opposed to buying a specific plant, so substitutions — say a red poinsettia for a pink one — are a reliable solution. Another tip Holliday has: be picky about taking on new customers. In Roebuck’s case, they added 12 new fundraisers this year after a nearby greenhouse closed, but only did so because they felt it wouldn’t hinder any existing business.
Both Galema and Holliday say the best way to prognosticate for the next year is to tally what sold well in the year before and to have conversations with repeat customers to gauge what worked for them and what didn’t. That, they say, is the best way to see what sells and allows them to order the right product.
The process of making fundraisers run smoothly, however, is ongoing. More than anything, successfully growing for fundraisers is about doing what you can to get ahead and make it work as best you can.
“The farther ahead we can work on new things, and start new fundraisers, the better,” Galema says.
Get curated news on YOUR industry.
Enter your email to receive our newsletters.
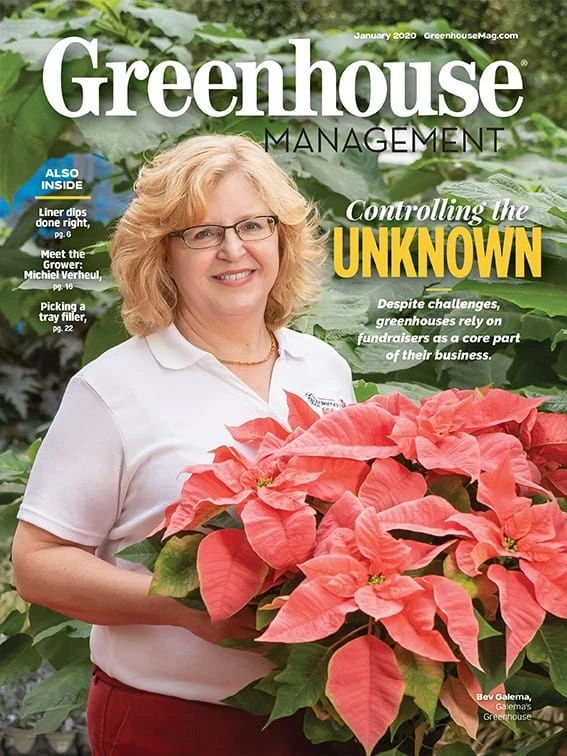
Explore the January 2020 Issue
Check out more from this issue and find your next story to read.
Latest from Greenhouse Management
- Flexible fungicides
- Super Charged Moon Juice from Moon Valley Nurseries now available nationally
- 2025 Proven Winners Horticulture Scholarship applications now open
- How to improve inventory and shipping management in the greenhouse
- Leading Women of Horticulture: Anna Ball, Ball Hort, and Terri McEnaney, Bailey Nurseries
- GM CEA HERB Part 2: A guide to increasing the sowing density of culinary herbs
- GM CEA HERB Part 1: Best practices for producing culinary herbs in controlled environments
- USDA fires experts on invasive pests, including Asian citrus psyllid, chilli thrips