
With the increased use of hydroponic and ebb and flood systems, there becomes a need for better treatment of recycled water. Older methods such as ultraviolet disinfection, heat treatment, chlorination, copper-silver ionization and slow sand filtration are being replaced by electrochemically activated water (ECA). This concentrated solution has many disinfecting properties including ozone, chlorine, hypochlorous acid and other biocidal agents. This process was invented in Russia about 30 years ago.
ECA is based on the principal of membrane electrolysis — an environmentally friendly process that reduces the use of chemical products by requiring only potassium chloride (commonly used for fertilizer and ice removal) or sodium chloride (table salt) and water. The chemical reactor consists of a metal cylinder with interior electrically charged electrodes separated by a specially designed ion permeable membrane. When a voltage is placed across the electrodes and the salt water passed through, an anolyte solution on the positive anode and a catholyte solution on the negative cathode are created. These liquids can be used separately or combined and injected into the irrigation water.
The anolyte solution is acidic and has an antimicrobial effect. Chlorine gas and oxygen are formed. The chlorine gas dissolves in the liquid to form hypochlorous acid. It is lethal to all pathogens. It is biodegradable and nontoxic to humans.
Neutral anolyte is also formed and consists of hypochlorous acid and hypochlorate. This acts like a biocide. Hypochlorous acid (active chlorine and hydrogen chloride) is unstable and has not been available until the development of ECA system. It is 100 times faster in killing microorganisms than the hypochlorite ion. The pH is usually 5 to 8.5. It has a low chlorine level and is approved for treating potable water. This material is effective against pathogens including bacteria, viruses, spores, mold and fungi.
The catholyte solution is mainly alkaline and acts like a detergent. It has a solution that is either sodium or potassium and hydroxide based. The pH is from 11 to 13. It has a cleaning effect and removes biofilm on pipes, tanks or troughs.
Older methods such as ultraviolet disinfection, heat treatment, chlorination, copper-silver ionization and slow sand filtration are being replaced by electrochemically activated water (ECA).
Electrochemically activated water has several advantages over other systems:
Simple installation of the equipment – The unit is connected to a water supply, electricity and an injector.
Effective control - Fights against bacteria, root and fungal diseases, viruses, and biofilm on pipes and equipment. ECA can be used at different concentrations for nutrient solutions, container cleaning, produce and seed disinfection and supply lines.
Easy to operate – Only need to refill brine tank.
Low injection rate – Less than 5 percent.
Low operating cost – Only a few kilowatts of electricity are needed.
Warranty – Usually one year. Cells need to be replaced after two to five years.
Unit size – Modular units are available in several sizes to fit different greenhouse and crop needs.
Harmless to the environment – ECA is harmless to human tissue and is commonly used to disinfect drinking water. ECA returns to plain water after 48 hours.
Raw materials are harmless and readily available – Base materials are sodium chloride (table salt) or potassium chloride. Brine solution is usually 0.5 to 1 percent.
No transport, storage or dosing of hazardous chemicals as ECA is produced on site.
Research has shown that electrochemically activated water is an environmentally safe water treatment that will produce plants with healthier roots, reduce disease and extend the life of cut flowers and produce. It also will clean the buildup of biofilm in the piping system.
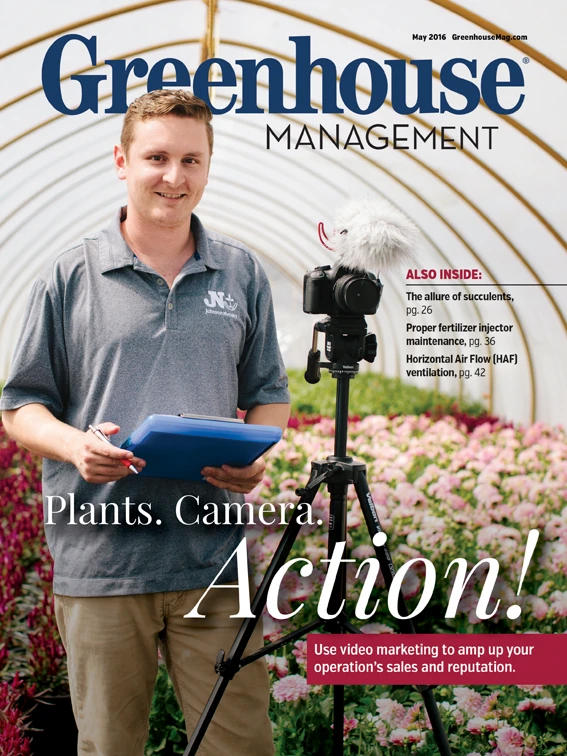
Explore the May 2016 Issue
Check out more from this issue and find your next story to read.
Latest from Greenhouse Management
- Grant awarded to test western U.S. wood species for use as wood fiber potting substrate
- Pennsylvania Horticultural Society announces 2025 Gold Medal Plant winners
- Oasis Grower Solutions announces new Southeast territory sales manager
- How to reduce labor in greenhouse vegetable production
- A nation of gardeners: A history of the British horticulture industry
- Last Word with Angela Labrum, Bailey Nurseries
- Iowa plant supplier Plantpeddler building retail complex
- This month's Greenhouse Management magazine is about native plants and sustainability