
Greenhouse technology has improved in recent years. Growers, via increased automation, artificial intelligence and other technologies, can achieve greater control over their growing environment than ever before. It can also reduce their dependence on labor. That is, if they want to.
No matter what crop they grow — be it annuals and perennials or vegetables — growers can now create the right environments so plants reach their maximum potential. The crop itself will determine some growing factors — temperature, light levels, etc. — but growers have the tools to zero in on those factors.
“We are getting to a point where people have the knowledge with crops that people actually know have the knowledge to use technology to its optimum and aren’t missing out on functionality,” says Wil Lammers, Ridder’s managing director in the Americas.
Affecting the bottom line
At the 2023 NGMA annual meeting, Lammers gave a presentation titled “Shaping the Future of the Industry: Insights on Emerging Trends and Technologies.” On one of the slides, which detailed different components growers can consider for their greenhouse, “crop management” was positioned at the center.
The reason is simple: Any and all growing businesses depend on how well crops can be managed.
“Crop management is always at the center,” Lammers says. “If you look at a greenhouse operation, how well you run this determines your financial performance, your ability to have positive cash flow. That’s for any greenhouse, whether it’s orchids or bedding plants or tomatoes or peppers. Whatever you grow, wherever you grow, it’s about creating the most optimal [environment] for the 12 months of the year you are growing. That’s how it all comes together in the end.”
That said, growers should also consider a cost-benefit analysis. Typically, the more automation and control growers build in, the higher the short-term cost. So, growers have to consider a) how much up-front costs they are willing to take on and b) what level of automation and control makes sense as a long-term investment.

Choosing the right components
Lammers says one of the keys is figuring out what components are actually right for a given business.
There are a number of ways to answer that question, he says. For one: location matters. Even in a controlled environment, the needs of a grower in Arizona are different than a grower in Florida. Both are typically warm environments, but Arizona is typically arid while Florida is more humid.
“Take a greenhouse with a pad wall for cooling for an example,” he says. “That will work very well in a dry climate. But if you take the same cookie cutter greenhouse and put it in Florida with 90% humidity, the ecosystem is completely different because you don’t get the same cooling effect because of the humidity outside compared to Arizona or Colorado where everything is dry. So you need to pick the components that allow you to grow on the inside optimally based on what is going on outside.”
Another factor in picking the right components is the actual crop. Every plant has different optimal temperatures for physiological and metabolic activity. When those optimal temperatures are met, that pushes the plants toward optimal yields and plant quality. And when growers achieve those optimal yields and the desired plant quality, they have happy customers.
There are regulations to consider, too. Greenhouse operators in the Netherlands have been adjusting to regulations that move them toward more sustainable practices for some time, he says, but growers in the U.S. are starting to see similar regulations. That is reason to look at how Dutch and some Mexican operations are co-locating to limit waste.
“It’s a migration process, right?” Lammers says. “Say you have an ethanol factory, it has a lot of waste products that, if I build a greenhouse next to it, I can get methane or other resources to feed to a greenhouse to make it more sustainable in combination. You see that in Mexico a little bit with agroparks, where you have 500 acres together with some companies producing waste products that can be used to feed the plants. We don’t even look at that kind of situation here.”

Potential labor savings
Labor, he says, remains one of the biggest concerns for growers, both from a cost standpoint and from an availability standpoint.
For some growers, labor costs are going up as minimum wage increases or they need to raise wages to be competitive with other jobs. For some growers, it’s become harder to find employees who want to work in a greenhouse setting and do manual labor. Some growers have turned to H-2A programs to fill labor needs, but there are costs associated with that as well.
That is where automation can come in, Lammers says. There will never be a world where growers don’t need some form of human labor to operate day-to-day. But with the right equipment, they can cut down on the need for labor for some tasks. Then, the labor that growers do have can be more efficiently applied to other tasks.
An example Lammers cites is environmental controls. Even at scale — in facilities over 100 acres — the technology exists that allows growers to not have to manually check and adjust the environment. Instead, it can be managed automatically with some check-ins and adjustments needed based on how the plants are growing. With less time spent on those tasks, growers can then focus on other jobs.
“What we can do with AI and autonomous greenhouse control,” Lammers says, “is give a top-notch greenhouse grower the capability to cover more acres with less people.”
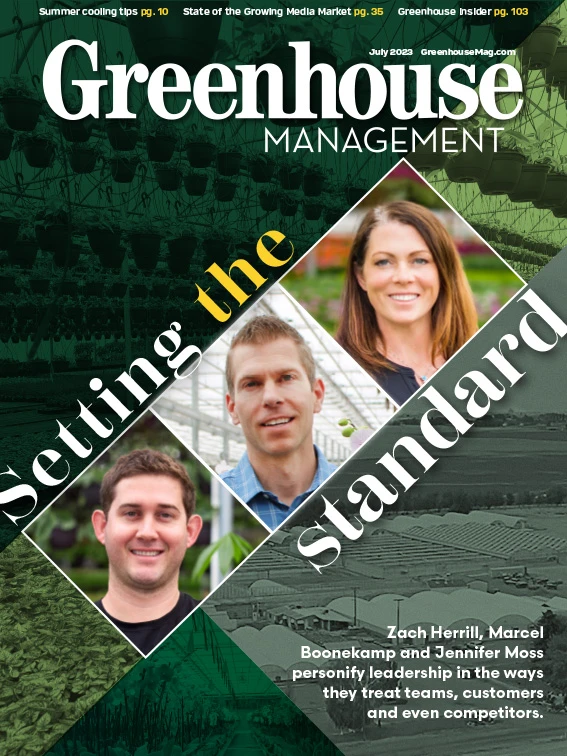
Explore the July 2023 Issue
Check out more from this issue and find your next story to read.
Latest from Greenhouse Management
- Flexible fungicides
- Super Charged Moon Juice from Moon Valley Nurseries now available nationally
- 2025 Proven Winners Horticulture Scholarship applications now open
- How to improve inventory and shipping management in the greenhouse
- Leading Women of Horticulture: Anna Ball, Ball Hort, and Terri McEnaney, Bailey Nurseries
- GM CEA HERB Part 2: A guide to increasing the sowing density of culinary herbs
- GM CEA HERB Part 1: Best practices for producing culinary herbs in controlled environments
- USDA fires experts on invasive pests, including Asian citrus psyllid, chilli thrips