
With the current difficulty in finding and keeping good employees, providing a safe and comfortable workplace is more important than ever. Providing better workplace conditions also improves efficiency and productivity.
As you work on your own operation, review the following:
Let there be light — Interior work areas should be adequately illuminated to minimize eyestrain. The common measurement for light intensity with efficient LED lamps is lumens/sq ft. For work areas, OSHA recommends a level of 70 lm/sq ft of floor area. For loading docks and storage areas, a level of 40 to 60 is sufficient. A simple calculation to determine how many lighting elements are required is to multiply the floor area by the desired light level and divide by the output of the selected luminaire. LED lights are standard today and they are available in many styles and outputs. Avoid glare by locating the fixtures out of the field of view. Light-colored wall and ceiling surfaces will help reduce contrast and shadows.
Heating is important — Work areas, such as a headhouse, can be cold and damp during the winter and spring if not heated. Depending on the type of task to be done, the ideal working temperature is in the range of 60° F to 68° F. The greenhouse is usually in this range for the plants. Gas or electric unit heaters or a separate zone on a boiler can provide the heat needed during the colder seasons of the year. Spot heating can be done with electric infrared heaters suspended over the work area.
Provide efficient workstations — For workers doing repetitive tasks such as potting or transplanting, consideration should be given to improving the workstation area. Movable worktables or a transplanting conveyor can increase production rates. Maximum dexterity and performance occur when the containers, plants, labels and other items are located within a 16-inch horizontal radius and 17-inch vertical radius of the normal elbow location. Objects that are placed outside of this zone slow the worker. Twisting the body or moving from a stationary position adds time to the operation. The height of the workstation should be just below the height of the worker’s elbow. For the standing position, this is usually 30 inches to 34 inches above the floor. Instead of walking, roller or belt conveyers can be used to move the materials to and from the worker. A sitting or standing position should be optional.
_fmt.png)
Non-slip floor surfaces will prevent falls — For safety and worker comfort, a good floor surface is needed. Non-slip surface coatings should be applied to areas subject to water spillage. Anti-fatigue mats made of vinyl or rubber can be used in areas around the workstation. When remodeling or building new facilities, follow the Americans with Disabilities Act (ADA) guidelines for access and safety.
Keep work and work area free of hazards — Many objects such as packing boxes, hoses, electric cords and machinery pose a potential hazard to employees as they move around. They also slow output. Place items such as tools, maintenance parts and weather gear out on shelves or cabinets. Try to keep the workstations out of the path of cart movement and human traffic. Assign an employee to clean up the work area at the end of the shift so there can be a fresh start the next morning.
Dust from media components and growing mixes can also present a hazard — Keep the media moist and use an exhaust system to remove the dust. Provide dust masks for working with dry mixes.
A noisy environment reduces productivity — When selecting equipment for mixing, container filling and powered materials handling, check the noise level. For some types of equipment, hearing protection may have to be provided to meet OSHA standards.
Check electrical safety — Portable electric equipment should be connected to ground fault circuit interrupters (GCFI). Machinery guards and safety shields should be kept in place.
Provide a quiet rest area — A convenient rest area can make lunch and break times more relaxing and enjoyable. Supplying lockers, tables, chairs, a snack machine, a refrigerator and a microwave can save employees time so they don’t have to make trips off the property to satisfy their needs.
There is a strong relationship between comfort, safety and productivity.
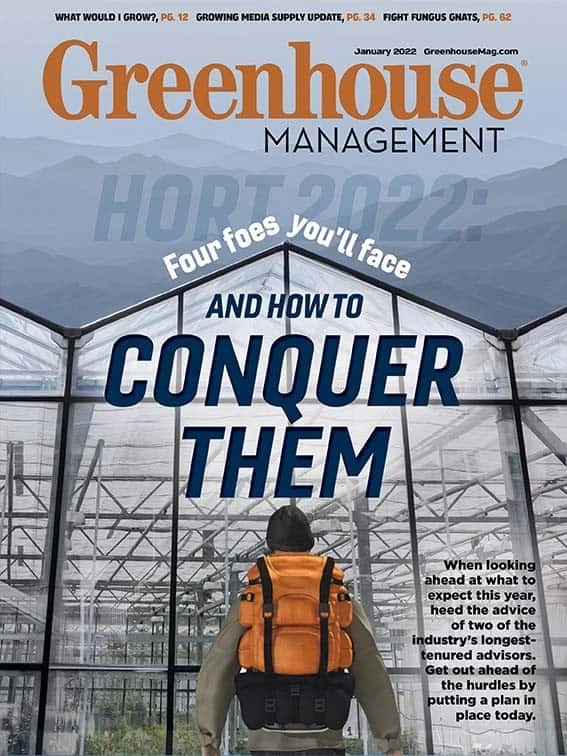
Explore the January 2022 Issue
Check out more from this issue and find your next story to read.
Latest from Greenhouse Management
- 2025 Proven Winners Horticulture Scholarship applications now open
- How to improve inventory and shipping management in the greenhouse
- Leading Women of Horticulture: Anna Ball, Ball Hort, and Terri McEnaney, Bailey Nurseries
- GM CEA HERB Part 2: A guide to increasing the sowing density of culinary herbs
- GM CEA HERB Part 1: Best practices for producing culinary herbs in controlled environments
- USDA fires experts on invasive pests, including Asian citrus psyllid, chilli thrips
- CEA Alliance celebrates bipartisan introduction of Supporting Innovation in Agriculture Act
- Dümmen Orange North America celebrating 25th anniversary in 2025