
Fogging equipment for ornamental crop production has come a long way over the last decade or so. Ultra-low volume foggers can now spray up to 2 million square feet as growers have pressed for machines that are bigger and faster. Also, some foggers are capable of doing double and even triple duty in the greenhouse: sterilizing, humidifying and cooling, giving growers a little more bang for their buck.
Yet, not all growers need a fogger with all these capabilities. Like any tool in your arsenal, foggers and sprayers are just another tool — an important one — to get the job done as efficiently as possible.
“It’s a really nice tool to have in your IPM toolbox,” says Tim Reusch, Western Technical Representative with Dramm Corporation. “[But] it’s not an end-all silver bullet where you’ll never have to use a wet sprayer again.”
Reusch says the main advantages of some of the modern fogging equipment are the increased efficiency of application and labor cost savings. Prices range from $3,500 to $15,000 for these machines, so it is important to select the right fogger to meet the needs of your greenhouse. Consider these points when investing in fogging equipment.
High volume hydraulic sprayers
The standard hydraulic sprayer may be what you initially started out using in your greenhouse. Like a hammer that you keep in your tool box even after upgrading to a nail gun, a hydraulic backpack sprayer is a tool that is still handy to have within reach in a greenhouse. Hydraulic sprayers can be effectively used to spot treat infestations before they get out of hand. A typical hydraulic sprayer operates between 100-300psi with an output between two and four gallons per minute with average particle sizes between 200 and 400 microns. When shopping for a hydraulic sprayer, Reusch suggests choosing a spray gun that allows for easy pattern adjustment and multiple nozzle choices.
Targeted low volume sprayers
The targeted low volume sprayer can do what the high volume hydraulic sprayer does only faster. These sprayers produce smaller particle sizes and lower flow rates, allowing for spot treatment and focused application in targeted areas where insect populations are running high. And because the particle sizes aren’t too small, they can be used in shade houses and even outdoors on a calm day. With low volume sprayers there’ll be little to no run-off.
Growers have several types of low volume sprayers to choose from, including high-pressure cold foggers, electrostatic sprayers, mist blowers and rotary disk sprayers. High pressure sprayers, such as the Dramm Coldfogger, working at 3,000psi will create fine droplets with high velocity, which results in good coverage to the undersides of leaves.

Not all foggers are created equal
Growers should do their homework before investing in fogging equipment. Ask other growers what has worked for them. Look at white papers and reviews of the different products on the market. There are different kinds of fogging equipment that can be used for different purposes and even ones that can multi task. There are likely advantages and disadvantages to each one.
“Know the structure where you’re going to be setting up the foggers,” says Reusch. “If you have a series of hoophouses, 20 to 30, a cold fogger or thermal fogger is a faster way to do it.” He says stationary equipment applies the product at a slower rate, but the automation saves on labor and it gets the job done effectively.
Fan-based foggers are an option for growers as well and can perform multiple functions in a greenhouse, according to Dana Pack, Vice President of Sales at Fogco Systems, Inc., based in Chandler, Ariz.
“We have a couple different product lines of fans, the Revolution and an Evolution.” says Pack. “Basically, what it does is fog comes out of a nozzle ring, airflow from the fan will either distribute it horizontally 360 degrees like an umbrella from top down; then we have fans that are more directional that send it horizontally.” He says an injector injects solution into the water supply that then runs through a high pressure pump, which atomizes into a fog. He says the particle sizes by this method is 10 microns or less, which allows for good distribution in the houses.
A good investment for growers
Given the cost of labor, which ranges from about $10-15 an hour, fogging equipment can be a good investment. With just 400 hours of manual labor at $10 an hour, a grower could break even with an entry level fogger quickly. If properly maintained, the equipment will last for years.
“We have some equipment that has been around over 20 years,” says Reusch. “The No. 1 thing is keeping the equipment clean and doing annual maintenance — change the seals and rings — [to] prolong the life of the equipment.”
If your fogging equipment works well but you’re thinking of upgrading, there are plenty of reasons to do so. The manufacturers of this equipment have added features and capabilities to these machines, mostly responding to grower input, to make them bigger, faster and smarter.
“The machines have gotten bigger, growers want something bigger and faster,” says Reusch. “That’s why we want a machine that treats 2 million square feet at a given time, that was unheard of 10 years ago.”
New technology also provides applicators important information that not only prolongs the life of the equipment, but can alert the applicator to halt fogging operations if something is going haywire.
“One of the biggest changes is with our custom high-pressure pumps,” says Pack. “We now build them with a PLC option, which controls several features in the pump. It allows for a high-pressure safety switch so if there is a breach in the line the pump will automatically sense it and shut down; it will also log hours of operation and indicate when maintenance is needed on the pump. In addition, it includes indicator lights that will illuminate and will track normal run operation and illuminates green light, normal operation; yellow for maintenance, red for a fault — high pressure fault or low water fault — and it will track and store that info as well. So, if there is any problem with the pump, it is much easier to troubleshoot.”
A fogging unit should also be able to apply any of the biological insecticides currently sold on the market. Food crops, in particular, require these products. However, many growers of ornamental crops are turning towards organic-based insecticides as well.
The bottom line in any pesticide applicator program is, of course, worker safety.
“Make sure you check with your state agriculture regulatory agency to see if you’re meeting drift compatibility requirements, if there is any for worker safety,” says Reusch.
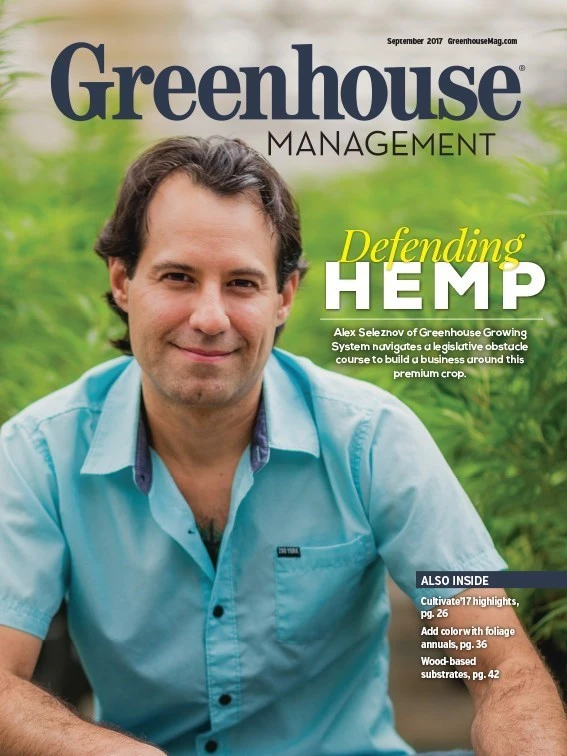
Explore the September 2017 Issue
Check out more from this issue and find your next story to read.
Latest from Greenhouse Management
- Society of American Florists accepting entries for 2025 Marketer of the Year Contest
- Sustainabloom launches Wholesale Nickel Program to support floriculture sustainability
- American Horticultural Society welcomes five new board members
- Color Orchids acquires Floricultura Pacific, becoming largest orchid supplier in U.S.
- American Floral Endowment establishes Demaree Family Floriculture Advancement Fund
- The Growth Industry Episode 3: Across the Pond with Neville Stein
- Flowerful growth
- The Growth Industry Episode 2: Emily Showalter on how Willoway Nurseries transformed its business