Improving the design and efficiency of an operation should be part of every grower’s New Year’s Resolution. But how do you accomplish that feat?
One of the answers is simple: Automation and work stations designed for efficiency.
Automation has many benefits, not the least of which is improving the flow of your production. That upgrade can increase efficiency and make an operation leaner at the same time, allowing for the production of more finished plants, while simultaneously reducing staffing needs.
Measuring the benefits of automation requires growers to calculate return on investment. To do so, growers need to compare cost of labor with and without automation, while taking into consideration the capital cost of equipment. A five-year amortization works well to calculate return on investment, but these machines usually run for 10 to 15 years.
Bill Bissell, lead process designer for AgriNomix, believes automation, plus an optimum design for workstations, will greatly improve any grower’s operation. He says a grower with a powerfully staffed 606 bedding flat production line, designed for hand planting and tagging, might have anywhere from 16-18 people working on it in order to produce an average of 550 flats per hour.
“With an efficient layout plan of the working area and the right automated equipment, such as an automatic transplanter and label applicator, a grower can reduce the number of needed personnel to four workers,” he says. “You’d have one person placing trays with inserts on a belt, one person overseeing the line including the automatic transplanter, one person fixing and patching and one person loading carts.”
Bissell says a grower who implements that design wouldn’t only reap the cost-savings of reduced staffing but could also nearly double their production capabilities per hour. The question for that grower would be: Does the upfront cost and expected maintenance of the automation outweigh the potential savings the machines could provide? Or can the grower find and then oversee 16 to 18 reliable workers to staff the manual production lines?
Seeing green
Return on investment, or ROI, can vary greatly from operation to operation. The standard calculation has to be adjusted to account for a myriad of factors, including: staffing levels, production capabilities, supervision required, desired production levels, facility size, existing levels of automation and ability to accommodate future automation. A smaller grower may choose to automate in order to allow a limited staff to keep the place humming. Larger growers may choose to automate in order to streamline for maximum efficiency and achieve the lowest cost of production.
Another area Bissell says growers should optimize is the in-feed and out-feed of the production line. Simple conveyors can create a buffer allowing personnel to work ahead. These conveyors can allow workers to be nearly self-sufficient when it comes to re-supply of materials. Growers are then free to reassign staff to other needed work areas or even eliminate unneeded personnel. When staff have well-designed and ergonomic work stations they’re able to perform at high levels.
“We can then view in our layouts all the personnel — their positions on the line — in conjunction with projected production rates, so that a grower can do his own ROI, based on current production rates and labor costs,” he says.
Have it your way
Determining where automation is needed is the most important part of the automation process.
“When we assist growers, we try to visit their facility,” Bissell says. “We find out who their customer base is, what products they’re producing, weekly and hourly production numbers and what they may want to produce in the future. We like to get as much information as possible so that we can provide growers with a realistic production design for each type of growing container and machine hours required to accomplish their goals.”
Some growers might think counting the number of products they produce per year will provide a detailed enough answer. They would be mistaken.
“Saying ‘We do 3.5 million pots a year’ doesn’t really tell us enough. We need to know the number of weeks it takes to produce those pots and then develop a rate per hour,” Bissell says. “Are you producing that in five weeks or 52 weeks?”
Once growers attain thorough calculations, they’ll need to measure their production area. Those measurements, along with specifications of the automation, will allow the grower or an outside consultant, to create a detailed drawing, sort of like an architectural blueprint.
“We map it all out on AutoCAD to scale with virtually every post located,” Bissell says. “We designate break rooms, restrooms, pallets of raw materials, plug and liner carts, fork lifts, etc. We draw all the production lines and try to build in the most efficient and safe flow of materials. We want to fully understand the foreseeable challenges and then develop the most efficient implementation plan.”
Four takeaways
Deciding to incorporate automation into your facility can be time consuming and difficult. Keep these tips in mind:
- Understand your current and future needs. You need to know your current staffing levels, how many plants you’re producing, what type of plants you’re producing, what your production schedule is and what you would like to produce in the future.
- Know your facility. Don’t rush into purchasing a large production line if your production area can’t house it. Design the area in a manner that also improves flow and accounts for proper storage and easy access of daily input materials.
- Take the time to calculate the ROI. This is crucial. You need to know if the equipment you’re preparing to buy is appropriate to your needs.
- Prepare, prepare, prepare. Take time to map out your facility.
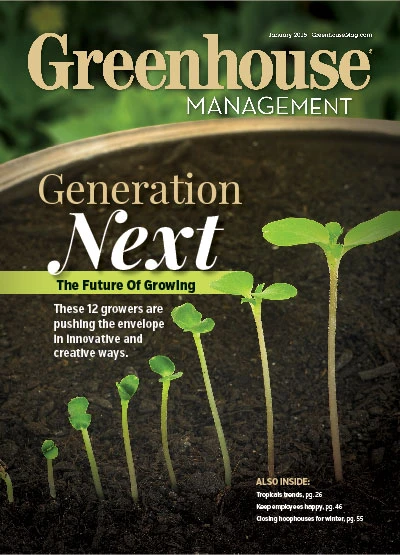
Explore the January 2015 Issue
Check out more from this issue and find your next story to read.
Latest from Greenhouse Management
- Grant awarded to test western U.S. wood species for use as wood fiber potting substrate
- Pennsylvania Horticultural Society announces 2025 Gold Medal Plant winners
- Oasis Grower Solutions announces new Southeast territory sales manager
- A nation of gardeners: A history of the British horticulture industry
- Last Word with Angela Labrum, Bailey Nurseries
- Iowa plant supplier Plantpeddler building retail complex
- This month's Greenhouse Management magazine is about native plants and sustainability
- The HC Companies, Classic Home & Garden merge as Growscape