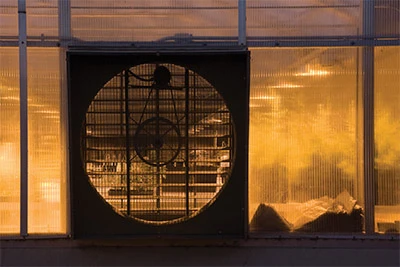
In the chilled winter months, when temperatures are frigid in the North and pleasant in the South, fan purchasing and maintenance might seem like a low priority for most growers. But Mark Fales, the sales manager at American Coolair, has some tips for growers trying to breeze through the season.
Buying a fan
- Look for fans that have been tested by an independent agency like the Air Movement and Control Association (AMCA) or the University of Illinois’ BESS Labs. Study the performance rating awarded to the fans by independent bodies.
- Seek out members of the National Greenhouse Manufacturers Association.
- Deal with a known supplier when you’re searching for fans. “If you go find Joe’s Garage Shop and he’s bending pipe down the road, and he’s going to supply you with some structure and some fans, you don’t know what you’re going to get,” Fales says.
- Consult with other growers. If you have a neighbor who’s also growing in a greenhouse, see what fan he’s utilizing and if he’s satisfied with its performance.
- Price should be a concern, but one considered within the scope of quality. “You can get cheap equipment, but you’ll be re-buying it again in a few years, but if you go ahead and buy quality product, it’ll be there when your grandchildren are taking over the greenhouse. You can be penny wise and pound foolish,” Fales says.
Winter maintenance
In the winter, you’re not really trying to cool the greenhouse, you’re just trying to inject some fresh air. But many growers select one fan to run and either seal the others or leave them wholly exposed. Instead, run each fan for a few minutes. This prevents condensation build up, which can lead to motor damage.
The benefits and drawbacks of fans Benefits: Fans provide a known quality, you know that you can move a particular amount of air when you need to. Natural ventilation is cheap but its effectiveness can vary wildly with the weather. A few days of unfavorable conditions and growers could start losing plants. Plus, the cost of operating fans isn’t always substantial. “Say I’m running two 48-inch fans with one horsepower motors and every hour they’re running I’m consuming two kilowatt-hours (kWhs), but the electricity company charges, $0.06 to $0.10 per kWh. That’s not a lot to have the reliability of knowing that you can control the environment in-house,” Fales says. Drawbacks: The initial investment in quality-tested fans can be steep. Growers have to purchase the fans and then pay for their installation. And running the fans comes with a price tag (even if it’s not particularly large), while natural ventilation relies on Mother Nature. You will still have some cost to install ridge vents or whatever mechanism that you will be using in order to utilize natural ventilation in your greenhouse. |
“One of the worst things you can do to an electric motor is not run it and keep it in a non-controlled environment,” Fales says.
If you’re not planning on running a fan and are sealing it up, be sure to keep the motor protected from the elements. Growers frequently seal a fan and leave the motor exposed. Instead, remove the motor and keep it in a controlled environment.
“If nothing else put the motor in the closet in your office where it’s heated and air conditioned,” Fales says.
And to properly seal the fan, growers should use non-breathable curtain material or some type of foam board insulation.
Many growers buy a backup motor for their fans. That fan should be stored in an environmentally controlled area. Frequently, a backup motor is stored in a shed or left exposed in the elements. Over time, that exposure can degrade the internal mechanism of the engine.
If you live in an area that suffers from overnight freezing, Fales recommends taking the shutter down and hitting each pivot point with a drop of antifreeze and then working the shutter up and down. “It actually refurbishes the pivot pens and it helps to keep the shutter from freezing up. Growers should do that maybe twice a year, more if needed,” he says.
Spring and summer maintenance
Don’t wait until it’s too late. The temptation is to let well enough alone and wait until the temperature is climbing above the mid-80s to start testing your fan equipment. Unfortunately, this can leave you with little to no time to fix broken parts. Instead, begin testing equipment when temperatures climb into the high 60s or 70s.
“If nothing else, just crank the fan up for a short period of time, a couple of minutes just to make sure it comes on, runs, so that if something is wrong they have time to order a replacement motor,” Fales says.
Spring is also a good time to check the belts on your equipment. Be sure that the tension is correct and that the belts are not too worn from use. Belts are relatively cheap and easy to replace, but you don’t want to wait until your busy season to do basic maintenance. “You can get a new belt for $10. Typically your belt should last you anywhere from 12 to 18 months with normal use,” Fales says.
Evaporative cooling maintenance
Growers using evaporative cooling should drain the system in winter. They should then remove the pump and store it in a controlled environment.
“Once again, you don’t want to leave an electric motor exposed,” Fales says. “If you leave it where it can get hot or cold, and not run it for six months, it’s probably not going to start when you’re ready to use it again.”
Another problem for evaporative cooling systems is rodents. Rodents will use the trough beneath the system like a runway, scurrying back and forth. The rodents will reach up and pull down chunks of the system’s cellulous material and use it to make nests.
“What growers might think about doing in the winter is going along the system and every 10 or 15 feet, pull a piece of pad out and throw some bait in there. Growers are essentially rat-proofing the pad system so the rats don’t chew it,” Fales says.
When Spring rolls around and thaws everything out, growers should bring their pump back, re-attach it and flush the system.
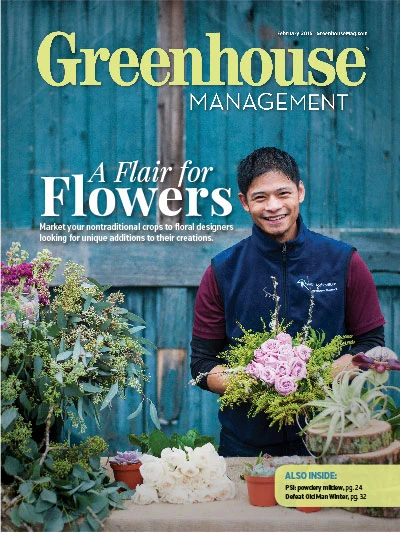
Explore the February 2015 Issue
Check out more from this issue and find your next story to read.
Latest from Greenhouse Management
- Happy holidays from the GIE Media Horticulture Group!
- North Carolina Nursery & Landscape Association announces new executive vice president
- Plant Development Services, Inc. unveils plant varieties debuting in 2025
- Promo kit available to celebrate first National Wave Day on May 3
- Applications now open for American Floral Endowment graduate scholarships
- Endless Summer Hydrangeas celebrates 20 years with community plantings
- Invest in silver
- Garden Center magazine announces dates for 2025 Garden Center Conference & Expo