Last year the University of Massachusetts Amherst completed a $10.8 million, 15,500-square-foot project, adding new greenhouse and laboratory space as well as updating a 4,500-square-foot teaching greenhouse.
Jacob Werner of Boston-based Payette Associates was the architect on the project and saw the opportunity to create an amazing research and teaching facility.
“They had probably in the range of 20 various kinds of structures and put them all in one place,” Werner says. “ … For us, we saw it as a way to take the laboratory research part of plant science and integrate it with the greenhouse in a way that’s different from other projects.”
The heart of the greenhouse is the sophisticated Argus system. It operates all of the other systems automatically. Staff can also log on remotely via the computer and see if things are going as they should.
“This is definitely a Cadillac of greenhouses,” Werner says. “It’s a really nice, really flexible, really sustainable greenhouse that will put them at the top of their game in terms of what they can do for research.”
The UMass systems Structure: Hot-dip galvanized steel structure. Anodized aluminum glazing system. Exterior walls with Insulated Glazing Units (Oldcastle Glass), high performance glazing. Roof with laminated glass for safety and durability. Natural ventilation: Both side wall and ridge vent openings, with automated operation (Ridder Motors). Accordion screen in the ridge vent, good natural ventilation and small insect penetration. Thrips screened positive pressure fans (PPF) for winter ventilation and dehumidification (Sigma Green, SFN GHPP). Evaporative cooling: Evaporative cooler units, specifically designed for GH application (all stainless steel, Sigma Green, SC-EC-60). Cold weather performance with motorized dampers with silicone edge seals. Thermally broken blades. Pleated thrips screen cartages for easier maintenance and cleaning. Fog/humidification system: Integrated with vertical air flow fans (VAF) for even distribution and stable humidity control (ML Systems, Princess). A/C compartments: All aluminum chilled water fan coil units, specifically designed for greenhouse use (Sigma Green, SGH 2250). Vestibule isolation for containment/exclusion zones. High humidity capable up to 70 percent. Served by laboratory’s high-efficiency chiller. Heating: All aluminum fin tube radiation heating (Delta T, Delta Fin system). Two independent heating zones per room: under benchtop and at roof. Shading: Vertical side wall curtains and horizontal shade curtains (Ridder motors, Svensson XLS shade cloth), automated. Lighting: High efficiency lighting system with electronic ballast (Parsource, GLX/GLS). Interchangeable high pressure sodium, metal halide, or other fixtures. Computer control: Fully computer controlled (Argus, Titan system). Internet connection and remote control capabilities. Data logging capabilities. Full featured weather station. |
Greenhouse Management spoke with Werner about how to effectively approach renovations and new greenhouse projects.
What tips would you give people if they wanted to put state of the art systems in place?
Understand what it is you want to achieve, so get a good sense of your priorities. What exactly are you doing in the greenhouse? What do you realistically want to be able to do that you can’t do in the greenhouse as it is at the moment? Usually that comes down to things like computer control. There’s a huge range of computer control. You can go from very basic all the way up to beyond the Argus system or a way more advanced Argus system, and it’s all money how much you want to do, but there are simple things that can be done to turn on and off lights or open shades, for example, that may only require you to put in a different shade panel.
I would say the most profound change that could be made is from a greenhouse without computer control to one with computer control. That may involve changing out some of the other things to work with the computer control system, but it will take you from being able to do a few things to being able to do a whole lot more in the greenhouse.
After you identify your needs, how do you proceed next?
It’s important to hire a good consultant – either an architect who understands greenhouses or a combination team of architect and engineers. Once you get that team on board, they can help you through the initial planning stage to figure out what you can realistically achieve with the budget that you have or help you set a budget so you can go do fundraising or whatever it is you have to do to start the project off. Once you have that team together, they can help you specify exactly what kind of lighting, what kind of heating, ventilating, control systems and other things you might need.
It was critical for us to have the right team in place because contractors, especially general contractors don’t seem to have a really great handle on greenhouses. They’re so specialized. And greenhouses vary so wildly from plastic covered hoops to the greenhouse we did at UMass. It’s not something that you say, “Greenhouse,” and people go, ‘Oh, I know exactly what you mean.’ It’s like saying, ‘Oh, I bought a book.’ Well, what kind of book? It can vary so widely, it has almost no meaning. … Trying to get across what it is you want is a little bit of a challenge because people have particular ways of working, so it’s a real communication issue trying to get your drawings, specifications, requests to the contractor in a language they can understand. I think that’s key – get the right team and reach out for help.
How do you get the right team?
There are different kinds of people that you can engage, and you may need them all depending on what kind of project you’re doing. We’ve worked with programming consultants who come in early in the project and they really just give you a 10,000-foot-level of what you might want to do and what kinds of overall systems you might want to employ.
We worked with Greenhouse Engineering. They helped us through working with the faculty to figure out what kinds of research they’re doing and then trying to figure out what kinds of facility they would need, and not just what they would need next year but also what they would need 10 years from now because these buildings tend to have 30-plus-year life spans.
You may want to ask yourself, ‘Do I need help figuring out what I’ll be doing in 10 years, or I already know that but I need help figuring out what kind of building will do what I want to do?’ Or do you already know that and have been through that step and you actually need somebody who can tell you what should it be made out of, and what size it should be and how durable it should be and what kind of electrical requirements it should be.
Once you have the 10,000-foot, you have the, ‘What general building do I need,’ and then you have the what specific equipment do I need, then you need to start talking to a contractor to figure out how much is this going to cost, how long is it going to take, what kinds of logistical problems are there – do I have to move out of my existing greenhouse for a year, or can they do it faster, and where am I going to go in that interim time frame and all those kinds of things.
I think viewing it as a process where you may need different kinds of advice at different points in time is a really good way to think about it, and you really want to find the right person for the place you’re at and don’t jump all the way to the contactor at the beginning because they may think they’re helping you, but they may not be able to. The last thing you want is to build the wrong greenhouse that won’t do what you want it to do.
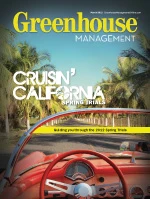
Explore the March 2012 Issue
Check out more from this issue and find your next story to read.
Latest from Greenhouse Management
- Happy holidays from the GIE Media Horticulture Group!
- North Carolina Nursery & Landscape Association announces new executive vice president
- Plant Development Services, Inc. unveils plant varieties debuting in 2025
- Promo kit available to celebrate first National Wave Day on May 3
- Applications now open for American Floral Endowment graduate scholarships
- Endless Summer Hydrangeas celebrates 20 years with community plantings
- Invest in silver
- Garden Center magazine announces dates for 2025 Garden Center Conference & Expo