![]() |
Desperate times call for desperate measures. That’s what we were thinking as we began to consider evaluating wood-based substrates for greenhouse and nursery production. At the time (2005), the forward-thinking Horticulture Research Institute recognized a need: What will growers do if there isn’t enough peat or pine bark available? How will they manage the increasing costs of fuel for shipping?
Nursery production isn’t exactly at the top of the totem pole of pine bark buyers (landscape mulch and fuel take that honor). And if there is a problem with the Canadian peat harvest (peat has a short harvest season; it’s frozen much of the remainder of the year), there’s not much you can do about it except keep a large storage facility filled with peat. In fact, in 2006 one large greenhouse grower (Young’s Plant Farm in Auburn, Ala.) was frustrated by the lack of price control for peat and began looking for alternatives to supplement their bedding plant production operation.
Fortunately, researchers at Auburn, Virginia Tech and North Carolina State Universities had already begun looking at alternative substrates that could replace or at least supplement peat and pine bark supplies. Specifically, they were looking at wood-based substrate materials.
Prior to these studies, it was generally accepted knowledge that using wood in potting materials was a terrible idea — that it would tie up nitrogen (N) and prevent the crop from taking up needed nutrients. This goes all the way back to the 1950s, when researchers at the University of California (Lunt and Clark, 1959) reported reduced crop growth due to N deficiency when wood chips were substrate components. The authors noted that wood-based substrates could still be used, but with caution. So everyone played it safe and generally stayed away from substrates containing wood fragments.
Because wood didn’t seem to be a viable option in the greenhouse, growers and researchers moved on to what can be more accurately described as substrate “amendment” — material that can supplement but not replace peat supplies for a variety of reasons. Most substrate amendments are composts or waste products. Often, they have unstable pH, EC and compress in containers. They may also have microbial activity from the compost (poultry litter, etc.), which can cause significant substrate shrinkage over time (certainly not ideal for customers). The good news is that many of these materials can supplement or extend peat and pine bark supplies when used at up to 30 percent of the total substrate volume. You get the best of both worlds -- lower costs with a local/regional waste product and consistent performance with peat or pine bark.
Researchers across the United States have screened a great many alternatives since the 1950s. At that time, pine bark was even considered a waste product of the lumber industry. Now, some of these materials are more useful than others, but looking at locally available materials can significantly increase the sustainability of greenhouse operations.
What other industries are near enough to your operation to be a source? In the literature review for my dissertation, I counted more than 30 materials beyond peat moss and pine bark that have been evaluated in the United States, Europe and Australia. Some of the more outlandish-sounding things that have been tested include shredded waste tires (zinc toxicity), municipal solid waste compost (sewage sludge), spent tea grinds, nut shells (cocoa, pecan, peanut), fish waste, beer waste and animal biosolids. Talk about resourceful! Still, you’ll want to stick to less than 30 percent by volume for most amendments.
What about these wood-based materials? They work very well, actually. In a nursery setting with woody plants, there are quite a few options that don’t require much change to the fertilizer program and can, in some cases, completely replace pine bark. Greenhouse production, however, is trickier. Herbaceous bedding plants are more sensitive to changes in substrate water-holding capacity, aeration, pH, EC, cation exchange capacity and nutrient availability than woody plants. That’s why it’s essential to test alternative substrates with each crop before implementing them operation-wide. But it can be done with great success.
Considering wood substrates
First, what species of wood are you considering? Research shows that softwood pine trees seem to be best, and in the southeast United States, they are the most available (clean chip residual, WholeTree/pine tree substrate). We’ve looked at hardwood species (oak, elm, maple, sweetgum, hickory), though most studies show that plants grew less in these materials (ties up N, can have toxicities, high pH). Douglas-fir bark works well in the Pacific Northwest. Punk tree (Melaleuca quinquenervia) might work well if you’re in Florida. If you’re in the Great Plains like I am, you can seriously consider eastern redcedar (Juniperus virginiana) and hedge apple (Maclura pomifera).
![]() |
Second, what particle size? After chipping trees, they need to be processed through a hammer-mill. The smaller the screen size (we like 3/16-inch for greenhouse production), the longer it takes to process and the more energy it requires. For larger containers, you can use larger particle sizes. In fact, if you’re looking to test wood substrates in your greenhouses, one of the best uses for larger particle sizes (3/8-inch) is as a perlite replacement.
Third, does it matter how long you store it? Surprisingly, not much. Many of our tests at Auburn were using freshly chipped trees. We could go from the tree to the pot in one day. But the reality is that you will likely need to store your material outdoors for a while. Not to worry. Minor changes in particle sizes may occur and pH may change, but these are manageable problems.
Lastly, will consumers and employees like it? We don’t have much data on consumers, but anecdotal evidence suggests that they may not even notice a change in substrate material as long as the plant is healthy. Employees at Young’s Plant Farm actually preferred the wood substrates over peat moss, citing that it was “softer” on their fingers than peat. Who would have thought?
Most recently, my colleagues (Drs. James Altland and Jim Owen, Jr.) and I have been evaluating eastern redcedar, switchgrass (Panicum virgatum), miscanthus (Miscanthus x giganteus), ground wheat straw, culled shade trees and biofuel crops, with funding from the USDA-ARS Floriculture and Nursery Research Initiative. We’ve compiled our most recent research along with recorded seminars and slide sets (among other resources) on our website, www.SustainableSubstrates.com. In the next several months, we’ll be updating it with research spanning the last 60 years, divided by material and growing condition (greenhouse or nursery). We hope you find it useful. Please drop us a line and let us know if you’ve got a question.
So, what happened with the Young’s Plant Farm substrate price control problem? Long story short, they worked with Dr. Glenn Fain at Auburn to test a pine tree substrate (WholeTree), and now they use it as a component of almost all of their substrate mixes (generally at 25-50 percent by volume, but that can vary depending on the crop). They not only use the wood material in their greenhouse operation; they now have their own sustainable forest harvesting and substrate processing facility on site, and more substrate stockpiled than you can imagine. Best of all? They have more control than ever over the cost and availability of substrate for their production facilities.
Processing your own substrate may not be an option for you, but that doesn’t mean you don’t have access to wood-based substrates. Ask your suppliers. The more you ask for it, the better chance they’ll know to look for something called fuelwood (clean chip residual) or WholeTree or pine tree substrate. Just know, the next time you’re feeling desperate over your peat or pine bark supply, there’s a wealth of information stored for you on the website. In the meantime, we’ll keep working and adding to the body of knowledge so it’s there when you need it.
Dr. Cheryl Boyer is an assistant professor and extension specialist for ornamental nursery crop production at Kansas State University. She earned a B.L.A and M.S. from Oklahoma State University (advisor Dr. Janet Cole) and a doctorate from Auburn University under the guidance of Drs. Charles Gilliam and Glenn Fain. Her doctoral research focused on the use of clean chip residual, a forestry by-product, as an alternative substrate. She has expanded this work at Kansas State University, where she has been evaluating aggressively weedy tree species as alternative substrates.
References: Lunt, O.R. and B. Clark. 1959. Horticultural applications for bark and wood fragments. Forest Products Journal, April p. 39-42.
Photos courtesy of Cheryl Boyer
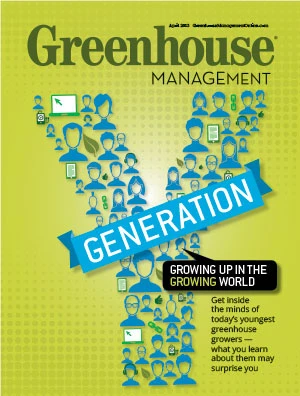
Explore the April 2013 Issue
Check out more from this issue and find your next story to read.
Latest from Greenhouse Management
- The Growth Industry Episode 3: Across the Pond with Neville Stein
- Trends: Proven Winners 2025 perennial survey shows strong demand
- Online registration opens for the 2025 Farwest Show
- Green Gear: Battery-powered backpack sprayer and a hoodie
- Sustainabloom launches Wholesale Nickel Program to support floriculture sustainability
- Be the source
- pH Helpers
- Society of American Florists accepting entries for 2025 Marketer of the Year Contest