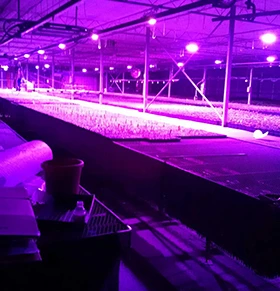
It’s a known fact. A plant depends on sunlight for photosynthesis and proper growth. Greenhouse growers, however, have gotten around the need for constant sun by installing high pressure sodium and fluorescent bulbs in their operations. In some regions, supplemental light is no longer an option, but a necessity in today’s market to maximize daily light integral (the amount light received in a specific area in a day’s period) on shorter days.
And now, growers are turning to yet another alternative: Light-emitting diode (LED) lighting. Science shows that with LEDs, growers won’t sacrifice light intensity. Plus, they may actually control how a plant grows and in some instances, enable it to grow quicker through adjustments in spectrum.
LEDs aren’t new, but they’re on the rise, with LED grow light module markets forecast to reach $1.8 billion by 2021 (the module markets earned $395 million in 2014), according to a 2015 WinterGreen Research report. The research firm is also anticipating worldwide “rapid growth” as LEDs are quickly becoming more efficient.
To that end, we’ve gathered testimonies from growers and information from manufacturers and researchers to explain the benefits LEDs can provide, as well as their potential setbacks, to help you make a more informed decision if you’re considering implementing LEDs in your own operation.
Watt for watt
Depending on the wattage, LEDs are just as intense, if not more so, than their high pressure sodium (HPS) counterparts.
“Because LEDs are more efficient, if you were providing an equivalent wattage light, say a 600-Watt (W) LED light, compared to a 600W high pressure sodium (HPS) light, our LED fixture is going to be delivering about double the photosynthetic par output [the range of spectral light plants require for photosynthesis] of the high pressure sodium,” says Cammie McKenzie product engineer at Horti-Tek, a commercial LED manufacturer in Florida.
She provides an example: If a grower is going from a 1000W HPS light burning 1150 watts per hour to a 600W LED fixture that’s going to give them the same results of the 1000W HPS fixture, they’re reducing their energy bill by almost 50 percent — and using about a fourth of the heat.
Chris Fifo, technical service adviser at Swift Greenhouses in Gilman, Iowa, trialed Horti-Tek lights in December 2014 with 600 square feet of seedling perennials and herbs (288 plugs) to see how they measured up to his HPS lights.
“The fixtures were really nice because you can just wire them into whatever is existing, and it automatically senses whether you have 110 or 220 volts, and adjusts [itself], so there’s no need to adjust or change any wiring,” Fifo says.
The 300W LEDs gave Fifo comparable growth to his current 400W HPS fixtures, and his results showed that with LEDs, he achieved the same photosynthetic par levels, and there were no adverse effects of using them, he says.
Although Fifo says he’s not ready just yet to implement LEDs into his entire operation, he’s looking toward the future. “It’s a great technology that’s evolving so quickly, and I think eventually it will reach a point where it can be cost effective to switch over to LEDs,” he says.
Some have already found the switch financially beneficial.
Jarratt Tunstall, vice president of Barnes Greenhouses, needed a better plan for his 9,000-square-foot facility in Dunkirk, New York, where the daily light integral is much lower during the winter season. That’s why he approached LumiGrow, an LED light manufacturing company based in California, in 2012.
LumiGrow worked with Tunstall to trial seven LumiGrow installments with his begonias and rooting geraniums. The next season, he purchased 40 more and now uses them throughout his entire facility.
“The geraniums were a lot faster to root,” he says. “After cutting a geranium, you can start seeing physical roots through an oasis wedge in a matter of seven days. Before that, it was two weeks [for us].”
It’s a 28-percent productivity gain, according to a case study by LumiGrow about Tunstall’s trial.
Not only did Tunstall produce higher yields, but he received a utility-sponsored, energy-efficiency grant from the New York State Energy Research and Development Authority, which significantly reduces his energy bill.
The savings turned the decision “into a no-brainer,” he says.
Coverage and customization
Tests show that not only do LEDs yield the same intensity as HPS lights, but coverage areas are also comparable, so long as growers work with lighting manufacturers to design a light layout, according to George Chan, marketing director for LumiGrow.
“When we brought the product to market…one of the design considerations was to create something that would function as a direct replacement for high pressure sodium, so we wanted to make sure that the light coverage was more or less the same pattern of the legacy lamp reflectors,” Chan says.
McKenzie says Horti-Tek’s newest model, which she hopes to preview in July at Cultivate ’15 in Columbus, Ohio will provide twice the intensity of traditional HPS lights.
There’s always room for improvement, Chan says, but LumiGrow is working to solve the myths that LED coverage is not equal to HPS lights. By conducting questionnaires and site visits, manufacturers can work with growers to cater to what they need on an individual basis.
The calculator McKenzie created at Horti-Tek considers a number of factors to calculate return on investment, including the model of light the grower’s already using, the LED equivalent and cost for installation, whether for a new build or a retrofit.
“We factor in the bulb cost and how often the facility changes their bulbs based on the hours and use, and we look at the wattage. We then look for any rebates that exist, whether federal or local utility company rebates, and we factor those into our calculator. Then we factor how many lights per day are used on different months of the year, and all of that comes together to tell us how much energy was used that year based on that light usage,” she says.
The calculator can also help determine how many years it may take for the LED systems to pay themselves back compared to HID systems, and then the savings cost over time of owning the system.
“Typical ROI for most facilities is three to five years,” McKenzie says.
Chan also says that HPS bulbs need to be changed every 10,000 to 20,000 hours compared to LEDs bulbs that are rated for 50,000 or more hours.
Color matters
The use of just two colors drives most of the positive results of using LED light.
“Plants utilize four colors primarily, two reds and two blues for photosynthesis. That’s the core of the light,” McKenzie says.
Red is the color considered to be most efficient for driving photosynthesis, according to Dr. Roberto Lopez, associate professor of horticulture at Purdue University. But when plants are grown with 100 percent red light, some crops can develop abnormally. Blue light, on the other hand, balances the spectrum of light, and plants grown under blue light can be smaller and more compact, a quality that’s favored in greenhouse production.
But an additional perk of blue light, as researchers like Lopez are finding, is that it induces anthocyanins, the red and purple pigments that can enhance colors of flowers and foliage and make them more visually appealing for consumers.
“That’s a key thing. Color is really important for consumers, not only impulse purchases, but the reason consumers love [a plant such as] Purple Fountain Grass is because it’s purple. And if they go to the garden center and they see a green plant with tints of purple, they’re not going to buy that plant. And the main reason those plants are not very green is that in the greenhouse, you’ve got low light intensities,” Lopez says.
“Plus, if they’re grown under glass, they [receive] very low UV light. UV light also stimulates anthocyanins as well as blue light. That’s why [with] using blue LEDs, we can stimulate those anthocyanins quickly and you get that nice, deep purple color.”
Red and blue ratios can also be adjusted to enhance growth for specific plants. It all depends on the grower's goals.
“[If growers] want to keep the plants short, make them grow tall, they want them stretched, they want them to flower sooner, flower later: We can control that entirely with the spectral ratios we put together for those plant groups,” McKenzie says.
Lopez’s latest study at Purdue University found that growth of bedding plant plugs can vary by adjusting red and blue light ratios. In their study, Lopez and his graduate student determined that plugs grown under supplemental lighting or sole-source lighting from LEDs were generally more compact, greener and had a higher root dry mass than those grown under high-pressure sodium lamps.
“In terms of the work we’ve done with the supplemental and sole-source lighting of young plants, primarily plugs, it can be very species-dependent,” Lopez says.
Not only can light be used to adjust plants’ density, color and length, but it can also affect taste.
A study published by LumiGrow in 2014 showed that manipulating blue light specifically can even adjust the taste in edibles. Depending on the treatment, sweet basil plants could taste spicier or more bitter with just an 8-percent adjustment.
The right brand
The number of LED options is increasing, so it can be daunting to choose the right manufacturer to fit growers’ specific needs. That’s why it’s good to shop around before making a decision.
“One thing I always tell growers is before you make a large investment, purchase LED arrays from several different companies and do small trials to compare plant growth and energy use,” Lopez says.
When choosing a company to trial from, find a reputable company with an experienced sales and technical staff, says Ron James, division manager at PARsource Greenhouse Lighting in Petaluma, California. Also, "Find a company that sells many types of lights so customers can find the proper light that fits their specific needs," he says.
"[Growers] will also want to look closely at the manufacturer’s warranty, which should cover the LED light engine, driver and all fixture components,"says Lisa Jansen van Rensburg, marketing specialist for P.L. Light Systems, a lighting knowledge company in Ontario, Canada.
And sometimes, the best sources are peers. “Talk to other growers who have purchased LEDs and see what they have to say,” Lopez adds.
It would also be beneficial to look into local, state and federal options for rebates for switching.
“The price and the technology is at a place where the headline is no longer ‘LEDs are the future,’” Chan says. “It’s really that [LED] is the choice to make these days… We recommend before growers undertake either replacements or a new installation, that they conduct a thorough evaluation of various manufacturers and find a company they believe in and have confidence in.”
Check out a time-lapse video of Swift Greenhouses’ basil plants grown under LEDs in action at www.greenhousemag.com/media.
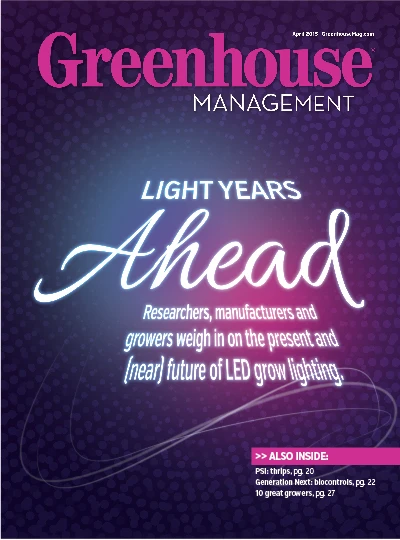
Explore the April 2015 Issue
Check out more from this issue and find your next story to read.
Latest from Greenhouse Management
- USDA fires experts on invasive pests, including Asian citrus psyllid, chilli thrips
- CEA Alliance celebrates bipartisan introduction of Supporting Innovation in Agriculture Act
- Dümmen Orange North America celebrating 25th anniversary in 2025
- CEA HERB Part 1: Best management practices for culinary herbs
- Lawsuit challenges new H-2 visa rules
- CEA HERB Part 2: A guide to increasing the sowing density of culinary herbs
- Illinois Landscape Contractors Association changes name to Landscape Illinois
- 2025 Proven Winners Horticulture Scholarship applications now open