|
Considerable progress has been made in improving the efficiency of automatic transplanters in the 25 years since they were first developed. There have been many improvements in the plug sizes they will handle, speed of operation, uniformity of placement and ease of changing from one tray configuration to another. Although more expensive, the new machines have given a big boost to the larger growers. For the mom-and-pop size operations that don’t need the volume production of an automated transplanter, a 20 to 30 percent increase in production can be achieved by just improving the transplanting workstation layout. Table height, hand and arm reach, and convenient availability of materials are keys to increased production. For the medium-size grower that grows mainly a spring crop of annuals or holiday plants, a transplanting conveyor can give a big increase in production. I have seen growers that have reduced transplanting costs by 30 to 40 percent by just installing a transplanting conveyor. Another option is the use of the Blackmore Punch’n Gro Puncher/Planter. This mechanized system will do up to 500 flats per hour. Plugs in specially designed trays are available from Ball Co. and grown by contract growers throughout the U.S. The machine pushes the plug from the plug tray through the bottom into the transplant tray. Punch plates are available for many flat configurations. The machine is easy to use and costs about $4,000.
The smallest machines can transplant enough flats to fill a 30-foot by 100-foot hoophouse in less than a day. These machines require a single operator plus the help needed to supply the prefilled flats and move the transplanted ones to the greenhouse. With the largest machines, you can fill more than a half acre per day. To get maximum production the transplanter is only one piece of equipment in a system that may include a bale breaker, flat destacker, tray or pot dispenser, container filler, transplanter, source tray feeder, automatic tagger, watering tunnel and associated conveyors. Once the trays are transplanted, carts or conveyors are necessary to transport the 1,000 flats/hr to the growing area. Automatic transplanters are available with a lot of features that may or may not be needed. When selecting an automatic transplanter consider the following: Select a machine that has a production rate that will match your production needs and schedule. One of the greatest benefits to having a transplanter is that you can refill growing areas quickly. How quickly can the machine be changed to handle a different size container, different cell configuration or different plug size? Will the transplanter handle hanging baskets, patio pots and bowls? Will the machine plant multiple plugs in the same pot?
Can the picking and planting depth be changed easily? Are the plugs damaged during handling? There are several designs for grippers including multiple needles and different styles of external grippers. Some machines incorporate a plug ejector to loosen it before the gripper holds it. How many persons are required to operate the machine? The basic machines require an operator and several persons to supply and take away the containers. What electrical power and compressed air supply is required? Machines will operate on 115 or 230 volts. A separate air supply is required by some to power the air cylinders that control movement of the arms and feed mechanisms. Servo motors are frequently used to control the gripper and planting pattern. What information will the transplanter computer system retain? Number of flats, size of flat, cell configuration, variety of plant, etc. This information helps in planning future crops. How much training will be provided? Are replacement parts readily available? Manufacturers usually require that sample containers and plugs be provided for testing on a machine before it is delivered. This helps in designing for the right number of grippers and the position of plants in a multi-plant pot. An automatic transplanter may require you to adapt your production system to handle different plug or tray sizes. You may also have to purchase or grow uniform plugs that are at the right stage of maturity with a well-developed root system.
With a new price of $20,000 to more than $100,000, automatic transplanters are generally economic for the medium to large growers. For example, if you are now using a transplanting conveyor with workers transplanting 50 flats/hour, at $10/hr wages, the cost per flat is about 20 cents. Installing a $30,000 automatic transplanter that has a production of 200 flats/hr/worker, the transplanting cost per flat drops to 5 cents. This 15 cents savings will give a basic payback of two years if you do 100,000 flats a year. You would need to have about three acres of greenhouse space to handle this volume if you filled the greenhouse twice a year. Automatic transplanters have reduced the drudgery and fatigue associated with getting the plugs into the flats. The increased production means fewer workers are required and more space can be filled in one day. John Bartok is an agricultural engineer and emeritus extension professor at the University of Connecticut. He is an author, consultant and a certified technical service provider doing greenhouse energy audits for USDA grant programs in New England.
John Bartok is an agricultural engineer and emeritus extension professor at the University of Connecticut. He is an author, consultant and a certified technical service provider doing greenhouse energy audits for USDA grant programs in New England. Have a question? You can write John at jbartok@rcn.com. |
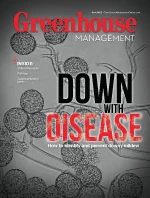
Explore the June 2012 Issue
Check out more from this issue and find your next story to read.
Latest from Greenhouse Management
- North Carolina Nursery & Landscape Association announces new executive vice president
- Plant Development Services, Inc. unveils plant varieties debuting in 2025
- Promo kit available to celebrate first National Wave Day on May 3
- Applications now open for American Floral Endowment graduate scholarships
- Endless Summer Hydrangeas celebrates 20 years with community plantings
- Invest in silver
- Garden Center magazine announces dates for 2025 Garden Center Conference & Expo
- USDA launches $2 billion in aid for floriculture growers