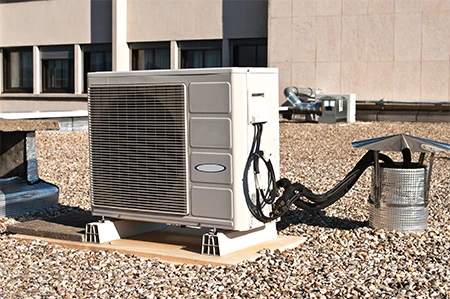
| Coolers and freezers are common in greenhouse operations for storage of plants, cuttings, floral arrangements and produce. Keeping plants and produce cool consumes a lot of electricity. New technology can provide 50 percent (or more) energy savings when applied to older refrigeration units. Energy efficient compressors — Replacing the standard piston-type hermetic compressor with a modern scroll compressor can save up to 20 percent in electricity use. You can recognize the hermetic type by its oval shape as compared to the cylindrical shape of the scroll compressor. The energy savings comes from the rotary motion as compared to the reciprocating motion. Scroll compressors have an energy efficiency ratio (EER) of 11 as compared to an old hermetic compressor with an EER of 6 to 8. Replacement cost is about $1,500/horsepower. Natural Resource Conservation Service (NRCS) EQIP funding may cover some of the cost. Drive motor replacement — For a large cooler with an old, well-maintained, independent hermetic compressor and electric belt-drive motor, it may be more cost-effective to simply install a new high efficiency motor. These motors usually have an increased efficiency of about 10-percent. Payback will usually be much shorter than replacing the compressor. Evaporator fan motors — To save on cost, most manufacturers incorporate shaded pole or permanent split capacitor (PSC) motors for their fans. A savings in electricity use of 40 to 60 percent can be achieved by replacing these with electronically-commutated (EC) motors. These motors convert the alternating power (AC) to direct current (DC) and then to 3 phase. This controls the speed and amount of torque. The electronic component of the motor allows for variable speed depending on the load. Wall/ceiling insulation — Older coolers and freezers frequently lack insulation that meets contemporary standards. The units manufactured now are required to have an insulation of R-26 for coolers and R-32 for freezers. Most older units do not meet those standards. Over time, insulation loses some of its R-value. Adding an inch or two of insulation, either extruded polystyrene sheets or foam in place polyurethane will help to reduce heat gain and save on electricity use. Door gaskets and closures may also need to be adjusted or replaced. Room lighting — LED lighting uses about one-half the energy of T-8 fixtures and lasts up to three times longer. It performs well at the refrigerated cooler temperature.
Energy Star standards — The payback may be shorter if you purchase a new cooler or freezer rather than retrofitting an old one. Select one that has an Energy Star rating that meets the minimum efficiency standards set by the National Appliance Energy Conservation Act (NAECA). These use about 20 percent less than standard models. Heat recovery — If you have a large cooler, waste heat from the compressed refrigerant could be captured to preheat irrigation or produce wash water. Refrigeration Heat Recovery units utilize a separate hot water tank with integral heat exchanger to take some of the heat out of the refrigerant gas. The gas circulates through the heat exchanger and is captured by the cool water in the tank. Refrigerant gas can reach a temperature in excess of 200 degrees Fahrenheit. Pollution reduction — Reducing the amount of electricity needed for cooling can help to reduce the amount of carbon dioxide and other pollutant emissions. It also can help to reduce refrigerant leakage that has been associated with global warming potential and ozone depletion.
Bartok is a regular contributor to Greenhouse Management and an agricultural engineer and emeritus extension professor at the University of Connecticut. He is an author, consultant and a certified technical service provider doing greenhouse energy audits for USDA grant programs in New England. Have a question? You can write John at jbartok@rcn.com.
|
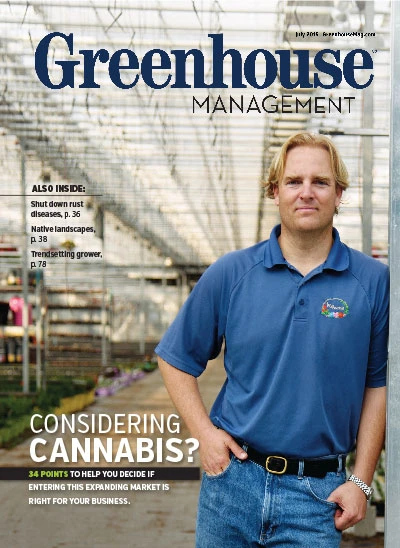
Explore the July 2015 Issue
Check out more from this issue and find your next story to read.
Latest from Greenhouse Management
- 2025 Proven Winners Horticulture Scholarship applications now open
- How to improve inventory and shipping management in the greenhouse
- Leading Women of Horticulture: Anna Ball, Ball Hort, and Terri McEnaney, Bailey Nurseries
- GM CEA HERB Part 2: A guide to increasing the sowing density of culinary herbs
- GM CEA HERB Part 1: Best practices for producing culinary herbs in controlled environments
- USDA fires experts on invasive pests, including Asian citrus psyllid, chilli thrips
- CEA Alliance celebrates bipartisan introduction of Supporting Innovation in Agriculture Act
- Dümmen Orange North America celebrating 25th anniversary in 2025