![]() Soilless hydroponic systems are a new growth area for container manufacturers. Courtesy of Beaver Plastics |
In any industry, the successful companies pay attention to trends and find new business in hidden market niches. And it’s no different with horticulture containers. We spoke with two container designers and manufacturers about what’s new in the world of trays and pots.
Quality is trending up Paul O’Neill, a professional engineer, is manager of grower products for Beaver Plastics. The Alberta, Canada, company makes containers and trays that resist root penetration, keeping roots undisturbed when transplanting. The shape of each cell encourages the roots to bind together with the soil into a single plug.
“Most people are familiar with the vacuum-formed containers they see in retail operations,” O’Neill says. “The Styroblock, Hortiblock and Plugblock grind away in the background, actually producing all of the plant material.”
Beaver Plastics’ trays and containers are used extensively in large commercial nursery production. O’Neill estimates that between 500 million to a billion trees are grown in their trays annually in North America.
“In the U.S., there is a lot of bare-root replacement, containerization occurring there. So the number of trees being grown is going down, but the amount of containerization is going up. We’re seeing large stock types going into that market down there.”
Rick Anderson, president of Anderson Die & Manufacturing, says he also sees some interesting trends in growing containers.
The Portland, Ore., company designs and manufactures a wide variety of field containers in sizes from one gallon through 20 gallons, used in mostly Oregon, California, Washington, Hawaii and British Columbia nurseries.
Anderson says today’s customers are looking for higher-quality products.
“There has been a long-term trend to go to thermo-formed, blow-molded, cheaper stuff,” he says. “That’s not what we’re in. We’re in injection molding. To us, because we’re in a different area with higher quality, we see interest seems to be waning somewhat in the low-end products that have either been thermo-molded or come from China. There seems to be more of a push for people to buy American, to buy locally.”
O’Neill also sees a move toward emphasis on quality. Essentially, there are two camps, he says — one that looks at its containers as commodities to be shipped out then thrown away, and one that wants to keep reusing the trays over and over again.
“The industry is its own worst enemy sometimes because they want a cheap, low-priced product to produce a premium plant, but you can’t have both,” he says. “You need a good-quality product to do a good-quality plant. It’s a balancing act.”
Anderson says the other trend he sees is a desire for products that can be reused or recycled. “We play into that, as the stuff people see in retail stores is usually throwaway, one-use pots,” he says. “But there seems to be a movement toward material that is reusable or recyclable.”
![]() The tallest band in this photo is the 9-inch band originally designed for deep-root tree propagation. It has become popular in the propagation of grape plants for wine growing in California, Oregon and Washington, says Rick Anderson. |
Root-rot prevention
Anderson says a few products have been doing well in the area of preventing root rot. In the last couple years, Anderson’s cross-bottom banded product has increased its sales. The bands are sold nationally, in contrast to some of the company’s bigger pots, which are sold regionally. Anderson attributes the increase in sales to the value the bands provide in terms of root growth. The bands have excellent drainage, he says, because it has just a cross across the bottom.
Another item with great drainage has been placed back in Anderson’s rotation by popular demand. About 15 years ago, the company developed a pot for an Oregon State University (OSU) project. The container had a slightly domed, sieve-type bottom. The holes through the entire bottom of Anderson’s “No. 1” pot improved drainage immensely, Anderson says.
Today, the No. 1 special bottom is becoming popular again, thanks to its excellent drainage. There is no problem with root rot because the roots are never left standing in water.
“It is a type of pot that is used in Europe a great deal,” Anderson says. “(OSU) wanted to introduce it to the U.S., so we built some for them. They were used for a while but never seemed to catch on much. Now there seems to be an interest in them again. We have had a number of people inquire about that and start buying those pots, which we were about to close out. That’s something old that people have reawakened to.”
In recent years, the special bottom of the No. 1 hasn’t been on Anderson’s normal price list, but it will make its reappearance next year because of the interest.
![]() The Anderson Special Bottom #1 has a slightly domed bottom and multiple bottom drain holes. |
New growth areas
One new growth area for Beaver Plastics is hydroponic growing. The company has developed a few new products to cater to drip- and deep-water culture vegetable production.
“Our trays are developed in a proprietary manufacturing process, that’s why they last so long,” O’Neill says. “They are well-fused and -manufactured. You need that with lettuce rafts and float systems.”
The system uses a saw tooth grow pad that is designed for use under growing slabs. These insulation boards provide an optimal root-growth environment. The design allows air to circulate under the root zone, evaporating excess moisture and providing a consistent temperature to roots.
The lettuce rafts were a result of O’Neill visiting a few large customers that were requesting some sort of hydroponic vegetable growing system. A trial-and-error period of factory-testing different materials ensued until he found something that matched what his customers required. The rafts are paired with plug-growing trays, such as the Hortiblock 242/26, or a solid growing media.
Another new growth area for containers is more surprising. In the last few years, customers have started using Anderson’s 9-inch bands to grow grapes for wine production. Grape propagation for wineries seems to be a pretty big business, Anderson says.
“They are being used by people who propagate grapes for wine in Oregon and California, Washington, too — all along the West coast,” Anderson says. “That’s become a new thing for us.
These growers are using the 9-inch banded pot, which was originally designed for deep-root tree propagation, because of its depth. The grapes need that space for their roots, Anderson says.
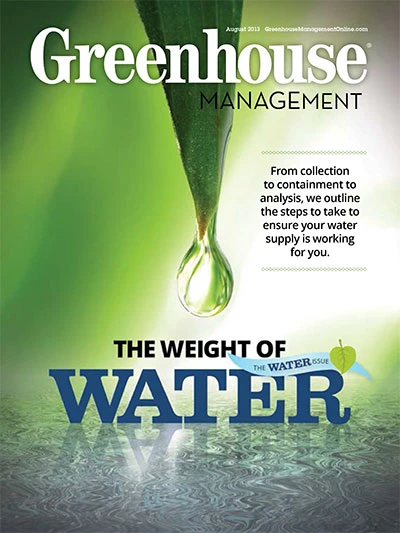
Explore the August 2013 Issue
Check out more from this issue and find your next story to read.
Latest from Greenhouse Management
- North Carolina Nursery & Landscape Association announces new executive vice president
- Plant Development Services, Inc. unveils plant varieties debuting in 2025
- Promo kit available to celebrate first National Wave Day on May 3
- Applications now open for American Floral Endowment graduate scholarships
- Endless Summer Hydrangeas celebrates 20 years with community plantings
- Invest in silver
- Garden Center magazine announces dates for 2025 Garden Center Conference & Expo
- USDA launches $2 billion in aid for floriculture growers