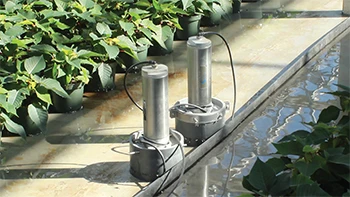
Editor’s note: The management of irrigation water is a top concern of ornamental growers who are affected by fresh water depletion as well as the introduction of agricultural water regulations. Several growers in New Jersey and New York have invested in recycling technology in anticipation of such regulations. This first part of a multipart series highlights the costs and benefits of disinfecting and recycling irrigation water using ozone in large-scale container production.
Lucas Greenhouses in Monroeville, N.J., opened in 1979 as a 9,000-square-foot facility. At that time, George and Louise Lucas, a husband-and-wife team, dreamed of one day having 1 acre under production. Thirty-five years later, Lucas Greenhouses is 18 acres and serves as a Syngenta rooting station and new plant trial site east of the Mississippi.
Lucas was one of the first greenhouse operations to utilize ozone disinfection 12 years ago. The greenhouse employs a unique integrated water-disinfection system using ozone, UV light, and beneficial bacteria to recycle almost 100 percent of its irrigation water.
“When we first put this system in, nobody in the industry was doing what I wanted to do,” George recalls while giving a tour of his property. Lucas’ unique water treatment operation was designed with the help of Charlie Hayes, whom George and Louise met at a Young Plant Research Group meeting at AgriStarts in Apopka, Fla., where there were 30 different water companies sharing different technology.
“I don’t know what drew me to Charlie so much. It was his personality just as much as his system, but I liked the fact that there are no chemical additives,” says George. “[We’re] taking oxygen, electrically charging it to O3, it does its thing, and it goes back to O2 again.”
Lucas started collecting water in 1985, but he did not know what to do with it.
“We knew sooner or later it was going to become an issue and we just didn’t want to be putting everything into the ground,” George says. George initially invested in a UV light system but never completed the installation because “there’s zero residual with UV- it kills what is in the tube and then what’s done is done. If anything is contaminated downstream, you’re back to square one. With ozone you have residual effects if the rates are high enough.”
The operation’s plants are bigger and healthier since they began their ozone treatment. “Very few greenhouses are collecting their water,” says George, “but I just wanted to be environmentally friendly. I figured the law would [be introduced] eventually.”
He is anticipating laws that will regulate irrigation and water management from horticultural operations.
Flood floor system
The ozone treatment began in 2002 when Lucas installed flood floors. The company uses flood floors with a two-zone system, where water is pressure pumped up and gravity fed down.
“It takes about six minutes to flood a bay with 5,000 gallons; anywhere from 500 to 800 gallons is being used up by the plant,” explains Jay Szymanski, the trial manager for Lucas Greenhouses. George adds, “the key is to treat the plant like a sponge. If you stick a sponge in water and pick it up fast enough, nothing drips back out. If you stick it in there and leave it too long, then you have drip. You don’t want that in a flood system because if [a plant]has a soil disease then the disease will come out.”
After irrigation, “the water comes back and goes over a paper filter that filters all of the large particles out. That’s always key in the whole process – if dirty water gets into the tanks then you’re in trouble. Keeping the water clean and flowing is key,” Jay says.
The water is filtered further with glass beads, gets electrically charged, and then goes into another tank to mix and that’s where the kill takes place. Finally, it is filtered again and reused.
Until a few years ago, this was the extent of the process. Since additional construction in 2011, Lucas Greenhouses can now reuse chemically treated water.
“If we have a floor that has a disease in it like Pythium, we’ll take that water and put it into a trash tank. Out of that trash tank we ozone that water to kill the Pythium, but there might be a chemical drench in it like a Bonzai drench. To take that out, we ozone it first, which will kill the Pythium and pathogens. To take the chemicals out, we run it through a UV light, which destroys that ozone and creates a free radial spike in the water. When that takes place, the ozone is destroyed and we can go ahead and put it through our biological filtration. That eats up all of the chemicals in the water. And that is pretty much clean water,” explains Scott Burger, one of George Lucas’ nephews who works in the family business.
Lucas takes his water disinfection a step further by reusing the water that is used to backwash his entire system. “These tanks have to be backwashed every other night; with almost 2,000 gallons (of water). That’s the worst water that you have and we didn’t know what to do with that, so we came up with something else. The backwash water goes into another tank, and every couple days that is run through really fine bag filters down to five microns. We put that water back into the tank and reuse it,” explains George. Nothing is wasted at Lucas Greenhouses.
Costs and benefits
George Lucas has invested about $425,000 in his water disinfection system, including ozone, UV, and biological treatment. “Then the only costs that are continuous are the paper filters, bag filters, and whatever energy sources you have. But we’re not adding a chemical to the water constantly- it’s just running.” These maintenance costs are estimated at $43,250 per year.
George encourages the use of ozone because of its residual effects, but insists that “you need to understand your water chemistry and what (the ozone) is doing to it. Ozone can take out the iron and manganese in the water, and in certain crops that’s critical.”
He advises other growers to consider water collection in the initial design of their greenhouses. “The water collection process is hard to retrofit; it’s got to be a concept from the beginning.”
While George says if he had the opportunity to do it over again, he would build smaller flood systems to have increased versatility. But the Lucas water-disinfection system has reduced expenses related to fungicide and chemical applications, while yielding healthier plants and more satisfied customers. Not bad for a first-time.
Alyssa DeVincent is a recent graduate from Rutgers University. She completed her honors thesis on water disinfection and recycling at horticultural operations throughout New Jersey under the guidance of Dr. Robin Brumfield, professor and Farm Management Specialist, and Dr. Paul Gottlieb.

Explore the August 2014 Issue
Check out more from this issue and find your next story to read.
Latest from Greenhouse Management
- Showing up at your horticulture business as your whole self
- Leading women of Greenhouse Management
- Leading Women of Horticulture: Katie Dubow, Garden Media Group, and Aubry Field, Lizzy Blossom
- USDA fires experts on invasive pests, including Asian citrus psyllid, chilli thrips
- Farwest Show calls for 2025 New Varieties Showcase entries
- Leading Women of Horticulture: Arden Pontasch, North Creek Nurseries
- Leading Women of Horticulture: Emily Showalter, Willoway Nurseries
- Leading Women of Horticulture: Anna Ball, Ball Hort, and Terri McEnaney, Bailey Nurseries