Industry trends are driving growers to move away from “touch loads” and toward a rack loading system. For many growers, the “California stack” method of loading a truck is still the standard. This method entails stacking plant containers on top of other containers, using the rims of the pots to balance. The advantage to this system is its unprecedented payload. Growers can load the most product onto a truck using this method.
Gerson “Gary” Cortes, partner with FlowVision LLC, a green-industry consulting firm, identified shipping as an area with plenty of room for improvement for many growers. FlowVision focuses on finding ways to incorporate Lean Flow principles into green industry businesses. As part of that, Cortes researched the different methods as a way to optimize shipping. He believes the solution is an optimized rack loading system, paired with the dock supermarket concept. While the payload is 1.5 times more with a California stack method than racks, it typically takes four hours to load a 53-foot semi-truck, with multiple people working in the trailer. Some of the operations Cortes has helped are loading the same size truck in 30 minutes. Another problem with California stacks is the toll that higher payload takes on plant quality.
“When we do the California stack we can get a little more on the truck, but it takes longer to load and unload, for the customer, and you have more damage,” says Mark Luchtefeld, vice president of sales and marketing with Home Nursery, an Albers, Ill.-based wholesale grower that began using rack loading in February. Home Nursery was using a combination of California stack and wooden racks, depending on what exactly was being shipped.
Not every grower uses the California stack. Other growers ship plants using deck stacks, floor stacks or wooden pallets. Cortes says deck stacks offer 25 to 30 percent less payload capability than racks. Time is a problem because trucking companies want to work with companies that make it easy for them to do their jobs.
“Many nurseries have told us one of their biggest difficulties is that trucking companies are not dying to work with them,” Cortes says. “They waste a lot of time waiting for that truck to get loaded and unloaded.”
This problem has been exacerbated by the Department of Transportation’s adoption of electronic logs. Paper logs were entered manually by the truck’s driver, so it was easy to fudge or manipulate times, if a driver were so inclined. The new E-Logs track a driver’s time more closely, and according to the laws, drivers can’t exceed 11 hours of driving and 14 total hours of work, including drops.
“If they pull up to your nursery, and it takes you four or five hours to load, you’re eating into their driving time,” Cortes says. “They don’t want to be there waiting for you to load.”
Unrolling the idea
One of the key principles of Lean manufacturing is that a business needs to be flowing product and eliminating wasted time. If a grower is shipping 40 trucks a day, it needs to churn those docks to be efficient. But you can’t turn them quick because it takes so long to load. Racks can be staged ahead of time, so when the truck pulls in with the trailer, it can be loaded and out the door 30 minutes later.
Ann Tosovsky, Home’s president, was intrigued by the idea. She spoke with growers at a few other operations that had switched to rack loading, and visited Spring Meadow Nursery in Michigan before fully buying in. Tosovsky brought the entire shipping crew together for a two-day training session.
“The training focused on understanding the concept behind Lean Flow and understanding what we’d be doing differently so they can get an understanding and have some input where applicable to the process,” she says.
The biggest change was how the nursery applied the racks to the pulling part of the order placing and shipping process to get the plant material up to the loading dock.
First, the plant is pulled out of the field onto a rack. That rack makes its way to the dock into what FlowVision refers to as a supermarket. Next, the nursery pulls the orders and places them on a different rack. That rack will go on the truck after it goes through an inspection process for quality control.
Although it’s only been a few months, Home Nursery is already noticing efficiency increases in several areas.
“Right now we’re seeing a good savings in pulling the plants up to the loading dock,” Luchtefeld says. “We’re seeing savings when we can rack everything. Loading the truck takes a lot less time. We see a savings in plant damage, and short counts.”
Racking up investment
Cortes says the two biggest investments for a grower looking to try rack loading are the racks, and the concrete they roll on. Many shipping docks are dirt or gravel, neither of which are conducive for the rolling racks that are key to the process.
Home Nursery still has work to do, but first it needs the right supplies. The wholesale grower needs more rolling racks to take the next step.
“We don’t have all the racks we need yet. They’re still being made. But once we get those, we get away from having forklifts,” Luchtefeld says. “We can pull them on the rack, bring them up through the dock sort through them in the supermarket process. Pick and put them on the rolling racks that will be shipped out.”
Luchtefeld says his customers have already said they’re looking forward to the new rolling racks because wooden racks are more difficult to unload if you don’t have a forklift. And if the nursery doesn’t come back for the wooden racks, the customer has to handle disposal, which usually means crushing it and putting it in their dumpster. The rolling racks will be tracked, reused and picked up regularly as part of the shipping schedule.
“Garden centers like the rolling racks because they can unload them right off the truck,” Luchtefeld says. “And if they have concrete aisles or blacktop, they can roll them to where they want to set them and sell them off the rack.”
It’s a process, and one that hasn’t even been around for a year. But the progress they’ve seen so far is encouraging.
Matt McClellan is Managing Editor of sister magazine Nursery Management.
Get curated news on YOUR industry.
Enter your email to receive our newsletters.
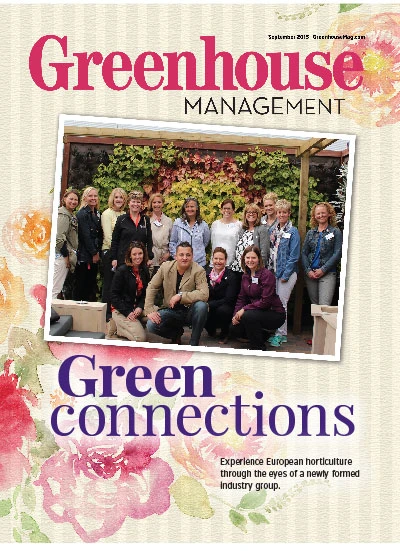
Explore the September 2015 Issue
Check out more from this issue and find your next story to read.
Latest from Greenhouse Management
- Flexible fungicides
- Super Charged Moon Juice from Moon Valley Nurseries now available nationally
- 2025 Proven Winners Horticulture Scholarship applications now open
- How to improve inventory and shipping management in the greenhouse
- Leading Women of Horticulture: Anna Ball, Ball Hort, and Terri McEnaney, Bailey Nurseries
- GM CEA HERB Part 2: A guide to increasing the sowing density of culinary herbs
- GM CEA HERB Part 1: Best practices for producing culinary herbs in controlled environments
- USDA fires experts on invasive pests, including Asian citrus psyllid, chilli thrips