Greenhouse thermal imaging
Thermal imaging could eliminate costly damage to equipment, structures.
In 2009, Hortica Insurance & Employee Benefits determined 48 percent of its property claims payments were fire related. To reduce customer fire claims, the company began testing a Thermographic Imaging program. We found this program may have successfully led to reduced fire-related claims of 43 percent, ultimately creating a savings for policyholders.
Thermography has became a service Hortica provides to all of its customers. Common problems identified by thermal imaging have been overloaded, worn-out and broken circuit breakers, overheated circulating fans, failing fuses and contacts, loose connections and energy loss.
Identifying problems
Thermal imagers identify potential problems quickly without shutting down equipment or an operating component because the thermal imagers operate on infrared principles.
Electrical optical devices are used to detect and measure radiation which is then correlated to the surface temperature. A thermal exception often appears using the thermal imager even when a visible inspection reveals very little, if anything.
Thermal imagers are a cost-saving tool for maintenance and inspection of electrical systems, troubleshooting mechanical systems and analyzing building envelopes. Thermal imaging has long been used for various applications such as building insulation inspections for energy, air leakage and moisture detection.
Troubleshooting equipment
Thermal signatures are snapshots at a single point in time of the heat being given off from an object. Comparing the thermal signature of a normal operating piece of equipment to one being evaluated for abnormal conditions offers an excellent method of troubleshooting. Excessive heat produced by an electrical system is a sign of impending trouble. High temperatures indicate excessive electrical resistance, failing components or other common problems in electric equipment that can lead to expensive or even catastrophic failures.
Motors are thermally inspected because they are susceptible to heat-related failure. Thermal imagery can help identify horizontal airflow fan motors that are running hot.
Access to operating and loaded equipment with a thermal imager is a requirement for detecting conditions that are possible problems. While not all equipment can be running all the time, it is possible to maximize the number of pieces of equipment that can be scanned if the visit is made during a time when the facility is at or near full operation.
Electrical components must be energized and loaded. A full load at a normal operating level is desired and should be loaded to at least 40 percent. Low loads may not show problems.
Electrical cabinets must be accessed by having panels opened to gain a clear line of sight between the infrared camera and the points of interest. All opening and closing of equipment must be conducted by site personnel who are properly trained and experienced with working around live electrical circuits and who are permitted to do so.
Using thermography reduces opportunities for fires, assists with preventive maintenance to avoid business interruption and decreases overall energy costs.
For more: Steve Woods, Hortica Insurance & Employee Benefits, swoods@hortica-insurance.com; www.hortica-insurance.com.
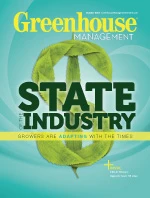
Explore the October 2011 Issue
Check out more from this issue and find your next story to read.
Latest from Greenhouse Management
- Flexible fungicides
- Super Charged Moon Juice from Moon Valley Nurseries now available nationally
- 2025 Proven Winners Horticulture Scholarship applications now open
- How to improve inventory and shipping management in the greenhouse
- Leading Women of Horticulture: Anna Ball, Ball Hort, and Terri McEnaney, Bailey Nurseries
- GM CEA HERB Part 2: A guide to increasing the sowing density of culinary herbs
- GM CEA HERB Part 1: Best practices for producing culinary herbs in controlled environments
- USDA fires experts on invasive pests, including Asian citrus psyllid, chilli thrips