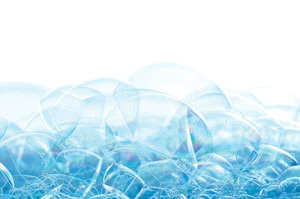
Researchers with the University of Vermont Entomology Research Laboratory are testing an innovative insulation system that could potentially cut energy costs for traditional greenhouses in about half.
“The basic philosophy of our research is to … directly address problems that our clientele or growers have,” said Bruce L. Parker of his team. “And one of the biggest problems faced by the greenhouse business is the high cost of energy usage in their greenhouses. Particularly here in the northeast, it costs them a lot of money to heat their greenhouses in the winter time.”
Thus, the UVM Conservation Project team saw an opportunity to pick up where a defunct Canadian company left off in testing a unique method for insulation that reduces energy requirements – dubbed the bubble project.
Funded by the Northeast Sustainable Agriculture Research and Education (SARE) program, the bubble project is being conducted at Claussen’s Florist and Greenhouse, Vermont’s largest greenhouse operation. The project aims to compare the energy savings of the bubble method to those of traditional air insulation and shade curtain methods and determine its feasibility for commercial use.
The bubble method boosts insulation by incorporating soap bubbles between the double layer of plastic used to cover many hoop and gutter-connected greenhouses, as opposed to the traditional method of pumping air between the layers. The UVM project has shown the bubble method to have an R-value (a measure of insulation ability) between 30 to 40, as opposed to the group’s control method using air, which results in an R-value of one to two.
“The insulation ability of those tiny bubbles is much greater than if you just blew air between the upper and lower (plastic) levels,” Parker said. “The bubble system will cut costs … by approximately 43 percent (compared to the control).”
The bubble method also shows improvement over shade curtains, an existing commercial method aimed at reducing greenhouse energy requirements. The curtains, which are drawn in the evening over the plant canopy within a greenhouse, are designed to provide heat insulation.
“(Shade curtains) had very little data on it to compare energy conservation with this bubble system,” Parker said. “We wanted to know, bottom line, how much money can growers save using the curtain system using this bubble system? That’s why we got involved, to try to answer that basic question. If we compare the bubble system to the energy curtain system, we can save about 20 to 25 percent.”
Both the bubble insulation and energy curtain systems provided significant reductions in natural gas usage and associated heating costs compared to the standard house. Greenhouses that use propane or fuel oil would experience even more savings than natural gas users. The bubble insulation system was more energy efficient than the other two. However, the bubble system required more ongoing maintenance to keep it operational.
The initial costs between the soap bubble system and a thermal energy curtain are significant — approximately $16,000 for the bubble system and $10,800 for the energy curtain.
The UVM Conservation Project team was able to retrofit the test bubble system from a 220-foot greenhouse at the defunct Canadian operation into an 88-foot, traditional cathedral-style greenhouse at Claussen’s. However the retrofitting process identified engineering flaws in the system that make it promising, but not yet ready for commercial application.
“Greenhouse growers are saying, ‘Wow, these energy costs are something else again. How can we reduce our energy costs?’” Parker said. “I’m hoping that we can find sufficient funding to specifically address the engineering problems that we have been able to identify during that would make (the bubble system) practical for use by growers.”
For more: http://bit.ly/17XEdJC.
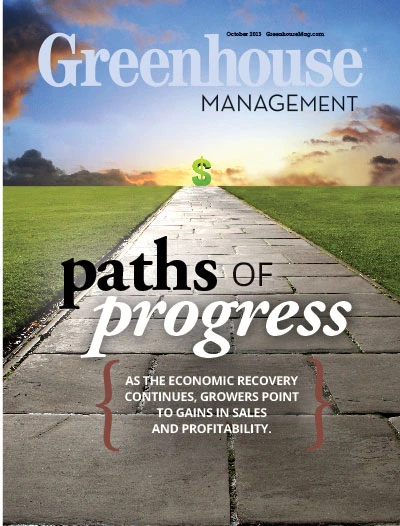
Explore the October 2013 Issue
Check out more from this issue and find your next story to read.
Latest from Greenhouse Management
- CEA Alliance celebrates bipartisan introduction of Supporting Innovation in Agriculture Act
- Dümmen Orange North America celebrating 25th anniversary in 2025
- Illinois Landscape Contractors Association changes name to Landscape Illinois
- 2025 Proven Winners Horticulture Scholarship applications now open
- ICL’s Gemini Granular herbicide now registered for use in California
- Eurazeo Planetary Boundaries Fund acquires Bioline AgroSciences
- Spring Meadow Nursery's Freedom Shelley finds joy in plants
- Leading Women of Horticulture: Dana Massey, Plantworks Nursery