At a workshop last week, a grower was telling me that to save energy he checks his thermostats at least twice during the heating season. This makes sense as it costs an additional 3 percent in fuel use for each degree that the temperature is above the desired setpoint. This article provides a few pointers to get better control of the equipment that is used in greenhouses.
Replace old thermostats
When selecting a thermostat for use in the greenhouse, look for one with moisture and dust tight boxes. Typical home thermostats have an exposed bi-metallic strip sensing element that can give erroneous signals when covered with dust or moisture. A better choice is a thermostat that has a hydraulic capillary tube filled with a liquid or gas that expands to activate the switch.
The movement of the switch between the “on” signal and the “off” signal is called the differential. This can vary from 1°F to 8°F for mechanical thermostats. Many of the Dayton, Penn and Honeywell thermostats used in greenhouses have a differential of 6°F or more. If you want to maintain a minimum 60°F (setpoint) in the greenhouse and have a thermostat with a 6°F differential, the furnace will start when the temperature falls to 60°F but doesn’t turn off until it reaches 66°F. This override overheats the greenhouse and increases both the heat loss and the heating cost. Some thermostats have a heat anticipator that shuts the furnace off just before the shut-off point. This will save some fuel.
If we have a 30 x 100 foot double-glazed greenhouse and compare a thermostat with a 6°F differential to one with a 2°F differential, the lower average temperature that can be maintained will save about 500 gallons of fuel oil, 750 gallons of propane or 700 therms of natural gas over a 2000 hour heating season. This is significant and at the price of fuel today will give a short payback. Replacing an old thermostat with an accurate one costs $100 or less and has a short payback.
If the greenhouse has both heating and cooling equipment, an electronic step controller with a +/- 1°F differential should be considered. The controller integrates all the equipment and prevents overlap of heaters and fans. Although the heating equipment may cycle more frequently, modern heaters and furnaces reach peak efficiency quickly and short cycling does not affect efficiency much.
Careful installation
Proper installation can also have an effect on the operation of heating and cooling equipment. The thermostat must feel the air that the plants feel if you want to control the temperature in the plant zone. A good location is at plant height near the center of the growing area. Some growers install the thermostat so that it can be raised or lowered for different crops. A thermostat mounted on an endwall or sidewall of the greenhouse, a location that heating equipment installers usually choose, will not give good results. Also be sure that it is not located directly above heat pipes or in the direct line of a heating duct outlet.
Thermostats and sensors should be shielded so that they are not in direct sunlight as this can give false readings. Installing the heating and cooling thermostat in one location is desirable as it reduces the chance of both systems operating at the same time. Also setting them at least 10°F apart reduces the chance of overlap.
Placing thermostats inside a closed aspirated box that is painted white will give more accurate sensing. The box has a small muffin fan that draws air past the sensors. Tests at Rutgers University have shown that the temperature spread (difference between high and low) in the greenhouse was reduced from 8°F to 2°F when the heating thermostats were aspirated. Energy is wasted any time the greenhouse air temperature is above the setpoint.
A thermostat for root zone heating should have a remote bulb that is centrally placed in the growing medium in the bed, bag or container. This is needed to sense the temperature in the root zone area not the air temperature above the plants. Air temperature can usually be 5°F to 10°F lower saving on fuel.
Check the controls for accuracy
All thermostats and sensors should be checked for accuracy at least once a year. They can get out of calibration due to dust and dirt on the sensor, being knocked out of level (mercury type) or if the dial is forced too far in one direction. Clean the sensor with a can of compressed air and wipe it if it remains dirty. Check the wire connections to be sure they are tight and not broken.
Although thermostats are calibrated at the factory they may get out of adjustment from handling. I have had growers tell me that new thermostats they purchased were inaccurate by 10°F. Start by checking the accuracy of a thermistor or thermocouple thermometer. These are inexpensive and work well because they’re fast acting and have an easy readout. Insert the probe into an ice water bath. The reading should be 32°F.
After allowing the thermometer to reach room temperature, place it next to the thermostat sensor. Slowly move the dial until the heater turns on. The reading should be the same temperature as the thermometer reading. If not, determine the temperature difference and mark the thermostat accordingly. Next time the heating system is serviced have it recalibrated.
Heating system control maintenance
Besides the thermostatic control, check gas valves, regulators and ignition mechanisms for clean, smooth operation. Inspect safety valves, low-water regulators, limit switches and stack controls frequently.
Low voltage causes heater and fan motors to burn out by overheating the windings. It can also affect the operation of the transformer creating a weak spark. Voltage at the motor should be at least 110 volts. Two causes of low voltage are inadequate power to the electric distribution panel in the greenhouse and too small a wire size that feeds the motor. This problem is quite common in hoophouses where long wires are needed to power heaters that are located at opposite ends.
On heating equipment, a barometric damper (oil fired) or draft hood (gal fired) should be used. The draft on the fire is affected by the height of the chimney, the temperature of the flue gases and the temperature and wind speed of the outside air. Increasing the height of the stack, the flue gas temperature or wind speed will increase the draft. Draft is also greater in the winter due to cold temperatures. Excessive draft increases the heat loss when the heating unit is in the standby. A barometric damper or draft hood should be located in the first 12” of the stack nearest the burner. Its purpose is to maintain a constant draft on the fire. A savings of up to 15 percent can be achieved with installation and proper adjustment. Barometric dampers and draft hoods are available at most heating equipment supply houses and home centers.
Accurate control of heating and cooling equipment will provide better quality plants and a significant savings in fuel. The small amount of labor that it takes for maintenance will have a short payback.
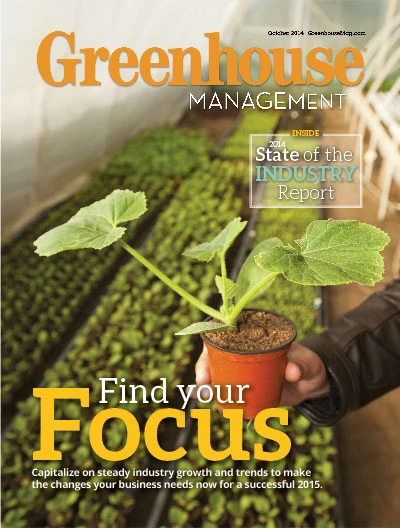
Explore the October 2014 Issue
Check out more from this issue and find your next story to read.
Latest from Greenhouse Management
- Trends: Proven Winners 2025 perennial survey shows strong demand
- Online registration opens for the 2025 Farwest Show
- Sustainabloom launches Wholesale Nickel Program to support floriculture sustainability
- Be the source
- pH Helpers
- Society of American Florists accepting entries for 2025 Marketer of the Year Contest
- American Horticultural Society welcomes five new board members
- Color Orchids acquires Floricultura Pacific, becoming largest orchid supplier in U.S.