![]() |
Although most greenhouses already have incorporated a certain level of automated environmental- and irrigation-control technology, they have to have proper installation and systems operations in order to reach their full potential. Advanced sensing can be used to not only reduce labor requirements but also improve plant quality.
An automated control system can be either open-loop or closed-loop depending on if sensor feedback is used to make control decisions. For example, a timer-controlled humidity management system is an open-loop system. The system triggers dehumidification at a pre-selected time for a pre-selected time period that is independent of the environmental conditions inside or outside a greenhouse or the crops being grown.
In contrast, a closed-loop system relies on sensor inputs to trigger control actions. For example, a closed-loop dehumidification system triggers heat-and-vent operations to remove humid greenhouse air only when a sensor senses the humidity is above a certain level. A closed-loop automated system generally performs better in a greenhouse environment where both environmental conditions and crop characteristics vary. The system's performance is dependent on accurate and reliable data collection for timely and proper control actions.
Collect the best information
GIGO — garbage-in, garbage-out — is an acronym typically associated with computer programs. The output of a program is only as good as the input supplied to the program.
This GIGO concept applies to greenhouse automation too, no matter how sophisticated decision algorithms or a control mechanism an automated system may have. Providing accurate information is absolutely critical for a system to deliver appropriate control actions. The location and protection of sensors can greatly affect performance of an automated control system.
Temperature control
Accurate temperature control is critical for optimizing plant growth. To provide a desirable production environment without wasting energy, it is important to make sure the temperature measured is truly representative of the plants' environment.
Temperature sensors should be placed at crop level just above the plants, regardless if they are in germination trays, growing on the floor or hung in the greenhouse ceiling. Thermostats mounted at convenient locations for easy operator access are not necessarily the same environmental conditions which the plants are experiencing. For example, a thermostat mounted on a space heater stand may be a convenient installation location, but the temperature measured in this location will likely be warmer and not representative of the temperature around the plants. To measure a more accurate temperature experienced by the plants, place sensors at crop level, not adjacent to a heater, or at eye level for the convenience of greenhouse workers.
Another common sensing error comes from sensors exposed to direct sun light. A thermometer exposed to direct light can show a much higher temperature than the one around the plants. It is essential to protect sensors with a radiation shield for accurate readings. Similarly, sensors should not be placed adjacent to hot or cold sources.
Sensor calibration
How much confidence do you have in your greenhouse sensor measurements? Do the thermostats turn on and off at the temperatures they are supposed to? Is the thermometer display also correct?
Accuracy of temperature sensors can be checked reasonably well with an ice water bath which provides a reference temperature of 32°F. Preparing an ice water bath using crushed ice, not ice cubes, and distilled water produces a reference temperature closer to water's ice point (32°F).
Fill a medium size cup with crushed ice before filling it with distilled water. Continue to stir the ice water bath during the calibration otherwise an error as large as 7°F may occur.
A temperature gradient may occur if the ice water bath is not well mixed. As higher density water sinks to the bottom of the ice water bath, the temperature at the bottom can reach 39°F at which temperature water has the highest density.
Calibration of relative humidity measurement sensors takes a bit more investment. Although handheld relative humidity meters are readily available and easy to use, my experience with them has been inconsistent, especially lower cost ones.
Three hand-held, electronic relative humidity sensors were tested at Ohio State University. Their readings were found to be 58.2 percent, 63 percent and 45.9 percent in the same greenhouse environment. It's essential to check the sensors' accuracy before trusting their measurements for greenhouse environmental or irrigation control.
A simple dry bulb/wet bulb psychrometer that consists of two thermometers is a good reference to check against. One of the thermometers (dry bulb) measures air temperature. The sensing tip of the second thermometer (wet bulb) is wrapped with a wick wetted with distilled water. By forcing air rapidly through the wick, the temperature of the wet bulb drops as water evaporates from the wick. Drier air causes greater temperature drop as a result of more water evaporation from the wick.
Irrigation technology ladder
An ultimate irrigation management goal is to produce quality plants with minimum resources. One basic irrigation objective is to provide water in time to prevent plants from suffering excessive drought stress.
Irrigation strategies can significantly affect plant quality. Excess water can make plants lush and soft while some mildly drought-stressed plants have improved postharvest quality. Further, irrigation management can also be a part of an integrated pest management program. By allowing the growing medium to dry down, growers can reduce root rot problems generally associated with excess water in the root zone. By minimizing excess surface water on greenhouse floors, growers can reduce algae growth that is a food source for insects, which can vector some diseases. From an environmental control perspective, minimizing greenhouse surface moisture can reduce evaporation which reduces greenhouse air humidity, lowering the energy requirement for dehumidification operations. The proper tools are needed to achieve each of the three irrigation objectives: water plants, enhance plant quality and manage pests.
Controlling irrigation
Automated irrigation can easily be achieved with a timer-based system if overwatering is not a concern. A more sophisticated system is needed to maintain growing media moisture in a proper range to control plant quality and pest management. This can be done either through estimation of plant water usage by modeling evapo-transpiration or by measuring the amount of available water or water tension in the root zone using soil moisture sensors or tensiometers. Recent advancements in using plant canopy temperature as a water status indicator have contributed to the development of several commercial infrared temperature sensors for irrigation automation.
![]() |
Horticulture professors Stephanie Burnett at the University of Maine and Marc van Iersel at the University Georgia discussed various tools for irrigation automation in a 2006 OFA Bulletin article entitled "Irrigation Automation: Looking at the Future." They suggested using various approaches to control irrigation events, including mathematical models and direct measurements. Estimating plant water usage based on mathematical models requires certain parameters (i.e. evapo-transpiration models, climate information such as temperature, relative humidity, solar radiation, wind speed, and plant property information such as canopy size, canopy density). For accurate model prediction, all environmental parameters need to be measured accurately and must truly represent the environment to be measured.
Sensor accuracy can be established through calibration. Sensors should be shielded from direct sunlight and placed away from heat, cold, draft, and moisture sources that are not representative of the growing environment.
Direct measurements of plant water usage can be done by measuring either the plants or the root zone. It is also possible to determine a plant's water status from the measured canopy temperature.
Transpiring plants move water out of their leaves which has a cooling effect, causing the plant temperature to drop below ambient air temperature. On the other hand, drought-stressed plants heated by solar radiation results in a warmer plant temperature than the surrounding ambient air due to the lack of transpiration to cool the leaves.
It can be a challenge to measure the true plant canopy temperature with an infrared sensor that sees not only the plant, but exposed growing medium, the container, the bench or the floor. However, measurement strategies have been developed to address this issue. An infrared sensor can be placed at an angle to the plants for a full crop view even before canopy closure. Researchers at Ohio State University have also developed digital signal processing methodology to compensate for background materials shown in the field of view of a sensor.
Using plant temperature
Plant temperature information can also be used to achieve better environmental control for growth and more efficient disease management. Photosynthetic rate is affected by leaf temperature. Being able to measure and maintain leaf temperature reliably, it is possible to control the greenhouse climate to achieve optimum growth.
It is also possible to reduce fungal disease pressure by controlling leaf temperature. Since wet foliage is prone to fungal diseases, condensate can be prevented from forming on leaves by keeping them dry. The leaf temperature should be maintained above the ambient air dew point to prevent formation of condensate.
Peter Ling is associate professor, Ohio State University, Department of Food, Agricultural and Biological Engineering, (330) 263-3857; ling.23@osu.edu.
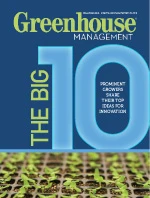
Explore the November 2011 Issue
Check out more from this issue and find your next story to read.
Latest from Greenhouse Management
- Super Charged Moon Juice from Moon Valley Nurseries now available nationally
- 2025 Proven Winners Horticulture Scholarship applications now open
- How to improve inventory and shipping management in the greenhouse
- Leading Women of Horticulture: Anna Ball, Ball Hort, and Terri McEnaney, Bailey Nurseries
- GM CEA HERB Part 2: A guide to increasing the sowing density of culinary herbs
- GM CEA HERB Part 1: Best practices for producing culinary herbs in controlled environments
- USDA fires experts on invasive pests, including Asian citrus psyllid, chilli thrips
- CEA Alliance celebrates bipartisan introduction of Supporting Innovation in Agriculture Act