
Sustainable practices were decades away when Jiffy Pots popped up in the U.S. nursery and greenhouse industry. It was the mid-1950s and George Ball discovered a Norwegian company that had found a way to turn peat into products.
Ball bought the rights and introduced what would become the first of the biocontainers, which was made of peat. Today, biocontainers are made out of everything from rice hulls and wheat straw to coir and cow manure.
Almost 60 years later, dozens of biopots are on the market or in the development stage, and claims about their effectiveness abound. Scientists decided it was time to investigate.
“There was information out there about the benefits of what are called biocontainers,” says James Schrader, an assistant scientist in the horticulture department at Iowa State University, “but no scientific evidence.” So researchers like Schrader began studies to determine if alternatives to the 800,000 tons of petroleum-based pots used by the nursery industry each year are viable for an increasingly green industry. Only about 2 percent of that mountain of plastic is reused or recycled, often because it’s inconvenient to consumers and labor intensive for growers to empty and clean.
“It’s a sea of plastic out there,” Schrader says. “Look across the landscape of a large operation and every one of those plants is in a plastic pot.”
The challenge is to find pots strong enough for production and shipping, but that break down quickly once they’re in the ground or compost pile. Biocontainers fall into two categories: plantable pots and bioplastic pots that are also made out of organic materials but are meant to degrade in a home or commercial composting situation.
With a $1.94 million grant from the USDA, Schrader and Kenny McCabe, research associate and graduate student in horticulture at ISU; led by William Graves, horticulture professor and associate dean of the university’s Graduate College, went to work on a five-year study that started 2011.
“We want to find a material that’s as good as or better than petroleum-based containers without the environmental consequences,” Schrader said.
They started with 46 different types of pots; some failed right away and were taken off the table.
Of the remaining containers, pots made of soy and polyactic acid performed the best. And the soy has the added benefit of providing nutrients as the mixture breaks down. The research continues.
Strength test
Additional studies on biocontainers are being done by Michael Evans at the University of Arkansas; Jeff Kuehny at Louisiana State; and Andrew Koeser at the University of Florida.
“We wanted to find out: Are they strong enough to stand up in the greenhouse and be shipped to retail outlets?” Kuehny says. “If it doesn’t have that, a container is not going to be much use.”
One of the studies was carried out at Longwood Gardens in Pennsylvania, where ‘Score Red’ geranium, ‘Grape Cooler’ vinca and ‘Dazzler Lilac Splash’ impatiens were planted into the soil. The researchers didn’t find any difference in growth between the nine pots, which included those made from rice hull, cow manure, peat, cocofiber, paper, straw, wood, bioplastic and plastic. All produced quality plants, but some needed more water than others. That’s a concern.
The environmental impact of additional water use can offset the benefits of biodegradable pots, Koeser points out. Some pots held water better than others, especially bioplastic types. And Schrader in Iowa has determined that thin coatings of bioplastic can reduce evaporation. One containing castor oil and water is far and away the best, he said, but not yet in production.
In commercial greenhouses, Koeser and his group looked at water use as part of a study looking at the overall carbon footprint of biocontainers.
“We looked at the production of a flower from seed to store,” Koeser explains. “We didn’t look at the manufacturing process, only the things a grower would have control over.”
Using ‘Yellow Madness’ petunia, they tested:
- Plant growth, appearance and time to market ready
- Container strength
- Algae growth, which was a measure of attractiveness to consumers
- Water demand
In the landscape, the group looked at plant growth and appearance over a growing season; and how fast the pot degrades.
Also studied were production systems such as pot-filling speed; damage from equipment, lifting and shipping; and the amount of unfilled pots.
The more porous pots, not surprisingly, needed the most water.
rEarth pots save landfill space, offer green container alternativeDuring the past three years, a new eco-friendly pot has begun to win over the market. Colorama, a California-based nursery, and Smith Garden in Washington are sold on rEarth pots, a new line made entirely of plastic water bottles. Manufactured by nursery supplier McConkey Co., rEarth pots look like traditional, petroleum-based plastic containers. And according to Steve Haston, director of operations at Colorama Wholesale Nursery, perform like them, too. “If you didn’t know what they were, you’d never know the difference,” Haston says. “There are no issues in production or at the consumer level. Absolutely, no issues.”
The rEarth containers, which take 60 percent less energy to make than petroleum-based products, have convenience going for them, too. They can be recycled at the curb, which appeals to consumers who increasingly want to be green. To get the sustainability message across, McConkey stamps the made-in-America containers with a recycled symbol. The new line of pots makes sense for Colorama, grower of annuals, perennials, herbs and vegetables, including an organic line. The company has made sustainability part of its mission, and is certified by CCOF and Veriflora. So far, the nursery uses four of the eight sizes offered by McConkey and is working with them to make sizes mandated by certain customers. “Where we can, we use rEarth,” Haston says. “Anything we can steer toward recycling, that’s where we’re headed.” Smith Garden Nursery, another sustainably minded grower that supplies annuals and perennials for the Northwest region, is on board, too. Cheryl Atwater, the company’s hard goods buyer, echoes Haston in her praise of rEarth. As soon as they came on the market, the company started using pint-size rEarth containers and is looking to add four- and six-packs. Again, results have been positive. “It performs just like regular plastic,” Atwater says. “And the concept that you can put them in your curbside bin is really cool.” Going green often means extra expense. Not with rEarth. Because the supply of material isn’t at whim of the petroleum market, the cost remains level. Overall, the price averages the same or less than virgin plastic products. Smith Garden hasn’t promoted the containers to customers yet, but Atwater said as attention to the environment and recycling grows, they will. “So far no news is good news,” she says. “The change went through seamlessly.” |
“If saving waste in the landfill is your goal, biocontainers are a suitable substitute for plastic,” Koeser says. “Any reductions in plant development, increases in irrigation and losses due to breakage will not void out biocontainers as a viable replacement for plastic.
“I think the take-home message,” he adds, “is that more natural biocontainers tend to be more fragile and slower to process than the plastics and bioplastics.”
As for the bottom line, biocontainers are more expensive than those made of virgin plastic, but as the cost of petroleum continues to rise and the amount of bioplastic becomes more available, costs are coming closer together.
“Yes, it is a little more expensive,” Kuehny says. “You have to pass that along to the customer. But it’s something you can add to your business profile. Customers want greener products.”
In the end — at least for now — growers have to weigh the benefits for themselves. As sustainability becomes more marketable and more of these types of pots hit the market, the decision will become easier.
“Biocontainers can capture the interest of consumers,” Kuehny concludes. “I see biocontainers as a visible way to show consumers one’s commitment to sustainable production.”
Kym Pokorny has written about the horticulture industry for 16 years. She grew up on her family’s wholesale nursery in Northern California. You can reach her at madrona29@yahoo.com.
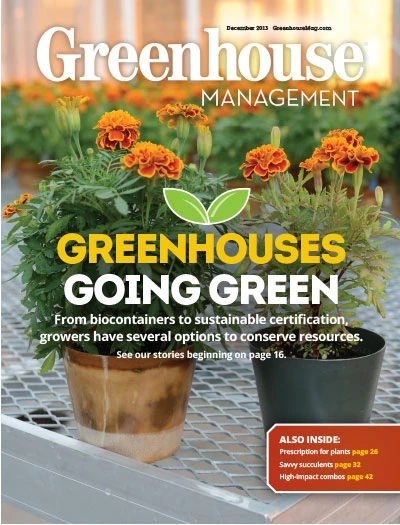
Explore the December 2013 Issue
Check out more from this issue and find your next story to read.
Latest from Greenhouse Management
- Flexible fungicides
- Super Charged Moon Juice from Moon Valley Nurseries now available nationally
- 2025 Proven Winners Horticulture Scholarship applications now open
- How to improve inventory and shipping management in the greenhouse
- Leading Women of Horticulture: Anna Ball, Ball Hort, and Terri McEnaney, Bailey Nurseries
- GM CEA HERB Part 2: A guide to increasing the sowing density of culinary herbs
- GM CEA HERB Part 1: Best practices for producing culinary herbs in controlled environments
- USDA fires experts on invasive pests, including Asian citrus psyllid, chilli thrips