Are you getting the most from the lighting fixtures used throughout your growing operation? Think of a light fixture like your car or truck. When new the vehicle provides the best performance possible. But as the vehicle is driven it requires regular maintenance to keep it running smoothly in order to provide efficient performance. The same is true with light fixtures. As light fixtures and their bulbs are operated over many hours they start to wear down. Bulbs start to fade in output, capacitors start to weaken and after a few years they’re not operating at the same level of performance as when they were new. Some growers maintain a re-lamping schedule that lets them know when parts need to be replaced. Some choose to wait until the bulbs begin to dim and wonder why their plants aren’t growing like they used to. Maintenance tips Here are a few things that can be done to ensure plants continue to receive the optimal amount of light from light fixtures. Wire for correct voltages. Make sure the voltage specified for the light fixture is what is actually wired in the greenhouse. Bulb selection. Some greenhouse growers looking to save money may choose to purchase inexpensive bulbs. Remember you get what you pay for. ![]() While two bulbs may put out the same number of footcandles or lux, they can dramatically differ in PAR outputs. Most light meters read what people see. A PAR or quantum (light) meter is needed to read the micromoles of PAR from a bulb. Bulb replacement. High pressure sodium bulbs should be replaced after about 10,000 hours of operation. After 10,000 hours most high pressure sodium bulbs begin to lose more than 10 percent of their output. A 10 percent PAR loss means a loss of 10 percent of growth from the supplemental light. Always remember to wear cotton gloves before touching a new bulb. The skin’s oil can affect lumen output and creates a hot spot on the glass that can lead to early failure. Metal halide bulbs, while used in some greenhouse applications (i.e., growth chambers, low natural light areas), depreciate in output much quicker than high pressure sodium bulbs. These bulbs usually need to be changed after 8,000 hours of operation. Determine bulb light loss. To determine the amount of light loss from a bulb, buy a new bulb and install it in a light fixture. Burn the new bulb for 100 hours to stabilize the gases in the bulb. Take a light reading at night at a set distance from the bulb. Record the reading. Now put the old bulb back in and take a reading. Calculate the percentage of difference between the two bulb readings. If the old bulb has experienced a 30 percent loss it is still using the same amount of energy. The result is the plants are just going to grow slower. Reflectors Check the fixture reflectors to determine if they are dirty. Also, look for calcium spots from splashing water or pesticide residue. These spots affect light reflection wasting output from the bulb. If a reflector is at a 20 percent loss of reflectivity, light and efficiency are being lost. Up to 60 percent of the light emitted by the bulb needs to be caught by the reflector and directed back toward the plants. Cleaning. Reflectors should be cleaned every two to four years depending on greenhouse conditions. A reflector can be cleaned with a 1:100 vinegar/water solution. Dip the reflector in this solution for a few seconds (depending on the condition of the reflector) and if necessary rub lightly with a fine fingernail brush to loosen the dirt. Do not scratch the reflector’s finish. Once the dirt is loosened, rinse the reflector in distilled water. Rinse the reflector once more in distilled water and let it dry. The distilled water eliminates any calcium or water impurities from drying on the reflector. Once dry, if there are still heavy deposits of calcium or chemical residues on the reflector that cannot be removed, it may be time to replace the reflector. If the reflector is clean and dry, it can be re-installed and is ready for operation. Replacement. Reflectors should be tested every three to five years. Reflectors should be replaced if they are found to be bent, have dings or major scratches. In general, reflectors should be inspected to look for anything that reduces their reflect ability. Capacitors Growers often complain about capacitor issues. A capacitor should be changed about every three bulb changes or 30,000 hours. Capacitors weaken over time. Heat and power fluctuations are the main reasons for capacitor failures. A capacitor levels out the current to the lamp bulb, assuring a correct and steady voltage. As a capacitor weakens it releases less energy to the bulb. This causes more heat to build up in the ballast and less light is emitted from the bulb. A capacitor is manufactured to swell up and break the connection when it finally fails. This swelling is like a fuse that breaks the circuit to prevent an open circuit from damaging other internal components. Fixture installation Installing light fixtures in the peak of a greenhouse structure with no ventilation can cause the fixtures to heat up very quickly. It is not uncommon for a fixture running in a 130°F-140°F greenhouse air temperature to have an internal temperature at or above the 105°F capacitor maximum causing the capacitor to fail. Installing remote ballasts on greenhouse sidewalls or in the head house is a good way to keep the fixture components cool and assure long life. James Grouzos is U.S. sales engineer, Laura Battle is sales coordinator, PL Light Systems, (800) 263-0213; www.pllight.com. PL Light Systems does reflector and lamp testing through its light care department. |
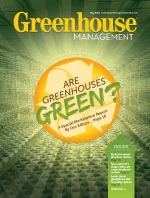
Explore the May 2011 Issue
Check out more from this issue and find your next story to read.
Latest from Greenhouse Management
- 2025 Proven Winners Horticulture Scholarship applications now open
- How to improve inventory and shipping management in the greenhouse
- Leading Women of Horticulture: Anna Ball, Ball Hort, and Terri McEnaney, Bailey Nurseries
- GM CEA HERB Part 2: A guide to increasing the sowing density of culinary herbs
- GM CEA HERB Part 1: Best practices for producing culinary herbs in controlled environments
- USDA fires experts on invasive pests, including Asian citrus psyllid, chilli thrips
- CEA Alliance celebrates bipartisan introduction of Supporting Innovation in Agriculture Act
- Dümmen Orange North America celebrating 25th anniversary in 2025