In 1998 with grant assistance from the Jefferson Solid Waste Management District in St. Louis, the staff at the Missouri Botanical Garden initiated the first effort to collect plastic gardening containers. The garden’s membership of 30,000 responded enthusiastically and with curiosity to learn the Garden’s intent to recycle the containers into molded plastic lumber. After collecting 10,000 pounds of containers in 12 hours over three separate Saturdays, the Garden staff was convinced that this was not only productive but passionately desired by the public. The demand for the trailers from garden centers is high. However, since they cost $9,000 apiece, careful consideration is made regarding geographical distribution, transportation capability, retail activity, liability coverage and dedication to environmental efforts. The satellite collection system works well. It engages the garden centers and their customers and is an important part of expanding the program in the future as funding becomes available. Currently about 150,000 pounds of plastic containers are collected during the six month season. Grower participation Commercial growers have also responded to the program, but they have the opportunity to become even more involved. Currently, Wednesday mornings have been designated as the time for growers to deliver truckload quantities of discarded pots and trays. The Garden requires that the growers sort the containers by plastic type and provide offloading assistance. Presorting the containers prior to delivery can save the growers time and money. The recycling response from growers has not been as good as anticipated. This may be due to the fact that growers have adequate space on their property to store old containers and don’t feel pressed to discard this plastic. Also, the labor required to sort the plastic and the transportation costs to haul the containers to a recycling site are factors for less grower participation. The Garden has also started to offer off-season times for the delivery of truckload quantities that are more convenient for some growers. Some incentives may be in order to increase grower participation. Processing the plastic With the collection process working well, the next step is to sort containers into trays/cell packs (No. 6) and co-mingled pots (No. 2 and No. 5). These containers are either baled or granulated into flakes. The equipment for this part of the process is costly but makes it much easier to manage the bulky nature of plastic pots and trays. Initially the Garden contracted to have the containers ground into flakes. Because of the cost to grind the plastic and the fact that companies available to do this were in and out of business, the Garden made the decision to take control of this process by acquiring its own equipment. The first grinding machine was purchased in 2004. In 2006, a more heavy duty grinder was purchased for $150,000. This machinery has enabled the Garden to process the containers onsite in a canopy-covered outdoor location. The granulation process, which handles the No. 2 polyethylene and No. 5 polypropylene pots, involves a conveyor, granulator, blower and aspirator. One of the earliest processing issues was with the amount of dirt and foreign contaminants that remained with the re-ground material, preventing manufacturers from using it. The solution was to remove any residual soil, metal clips/hangers and loose paper by hand prior to granulation, then use an aspirator to clean the plastic further. The granulated flakes (regrind) are stored in 1,000 pound capacity Gaylord boxes and kept dry in steel storage containers in a nearby parking lot. The No. 6 trays and cell packs are sorted and baled. East Jordan Plastics in East Jordan, Mich., donated a vertical baler in 2010 to handle the trays and packs. The company has the right of first refusal to buy the polystyrene bales and transport them to its Michigan facility, where the plastic is incorporated into its containers. Major investment The Garden has invested nearly $500,000 in the collection and processing of recycled plastic containers. All of the money has come from grant money provided by state government and from business donations over a 10-year period. Monrovia has supported the program from the beginning and provided many of the sorting trailers. The Garden has hired four part-time employees to process the containers during the six-months collection period. The yearly operational cost is about $25,000. Sales of the regrind plastic and baled trays help to offset the operating costs. As petroleum costs continue to increase, plastic feedstock prices will also rise making the container recycling process a more sustainable practice. The success of the program lies in being able to develop an end product that can be sold commercially. The recycled containers have been used to produce plastic lumber by local manufacturers. Unfortunately these companies are not always viable in their ability to stay in business. There is a demand for plastic lumber for raised gardening beds. When the lumber is available, the Garden has been successful in selling it at its recycling site. The Garden is hoping to continue its “From Pots to Planks” program. The recycling program collected a record 138,000 pounds of horticultural waste in 2010. This year the Garden expects to surpass 1 million pounds of collected containers. That’s a lot of plastic diverted from landfills.
|
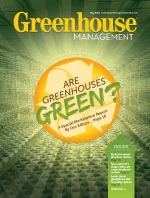
Explore the May 2011 Issue
Check out more from this issue and find your next story to read.
Latest from Greenhouse Management
- 2025 Proven Winners Horticulture Scholarship applications now open
- How to improve inventory and shipping management in the greenhouse
- Leading Women of Horticulture: Anna Ball, Ball Hort, and Terri McEnaney, Bailey Nurseries
- GM CEA HERB Part 2: A guide to increasing the sowing density of culinary herbs
- GM CEA HERB Part 1: Best practices for producing culinary herbs in controlled environments
- USDA fires experts on invasive pests, including Asian citrus psyllid, chilli thrips
- CEA Alliance celebrates bipartisan introduction of Supporting Innovation in Agriculture Act
- Dümmen Orange North America celebrating 25th anniversary in 2025