![]() George recalls that they wanted to be environmentally responsible, but the tools and the demand to do more were simply not there. Like most growers operating at that time, margins were better able to absorb some product shrink resulting from irrigation problems and water quality issues. There wasn’t a lot of talk or concern about water restrictions and conservation. ![]() Thirty two years later, Lucas Greenhouses is finalizing the installation of one of the most sophisticated closed loop water conservation and treatment systems in the U.S. ornamental plant industry. There were several reasons for focusing on water conservation, including a sense of civic responsibility; concerns about crop safety; environmental issues and the financial aspect. Water management challenges, including having an adequate water supply, filtering large volumes of water, automating fertilizer injection, preventing pathogen contamination and limiting water and chemical runoff, had always been addressed as they arose. Addressing these challenges, the Lucases became more aware of the need for better water management and their plans to address them became more ambitious. “In the beginning I had no intention of ever getting this big, so my problem grew as we grew,” George Lucas said. “It became obvious we needed to come up with a solution quickly. Dangerous word: quickly. “The first step was realizing just how much irrigation water was running off,” Lucas said. “Once this was realized then it was both an environmental and a financial concern. It just seemed the right thing to do, but again, the question was, how do we do this? Water is a precious commodity and there is a limited supply of good quality water. Water is one of, if not the most important input in growing plants. I believe most growers do not fully understand all that is going on in their water, their water source, and how the way we use it affects the total picture.” Evolving water conservation efforts Initial steps toward water conservation and runoff control really began at Lucas in the 1970s with the digging of a runoff retention pond. The pond, which was expanded three times, is dedicated to capturing all of the rain runoff from the greenhouse roofs. The pond, which has 150,000 square feet of surface area, holds about 13.5 million gallons of water. Fed by natural springs, the pond is a key component of the company’s self-contained, zero runoff water management system. As more greenhouses were built Lucas incorporated more water conservation efforts. In 2002, Lucas installed the company’s first flood floor system and an Argus computer control system with automated irrigation. This was its first system that captured and reused the water automatically. The flood floors dramatically reduced the amount of water used and the amount of runoff. The computer controls improved water conservation by making more precise decisions about when to water. Similar expansions with flood floors and computer controls were made in 2004, 2007 and 2008. Total production area is about 770,000 square feet. During this period of expansion the company tried various chemicals to disinfect irrigation water, but found them to be too costly and/or time consuming to use. Lucas learned that proper monitoring of water treatment inputs and results is time consuming but critical to maintain proper pathogen kill levels with chemical solutions. The company also tried an ultraviolet light purification system, but never completed the installation. The system was improperly sized for the amount of water that needed to be treated. The “right” treatment Shortly after the last greenhouse expansion in 2008, the company turned its attention to the runoff that was leaving its property, particularly the discharge from collection cisterns. The company was looking for a way to remove any traces of pesticides, herbicides and plant growth regulators that might be in the water runoff. While attending a Water Education Alliance for Horticulture workshop in Florida, company officials learned about ozone treatment. They were introduced to the biochemical process of advanced oxidation, which combines ozone with either hydrogen peroxide compounds or ultraviolet light. This treatment method can be used to eliminate water-borne pathogens as well as many chemicals, including the herbicide glyphosate. Following the workshop, the company installed an ozone system to treat the flood floor water in one of its ranges. This will be third season the treatment system has been in operation. Water is re-circulated from three flood tanks through a pre-treatment filtration system that removes about 95 percent of the particulates down to 5 microns (microscopic size is 20 microns). The water is then circulated through a patented ozone contacting system, where it is disinfected using ozone gas and then returned to the tank from which it came. The system is designed to operate 24 hours a day, rotating from tank to tank. The system was also found to be effective against water-borne pathogens as part of a PhD research project sponsored by the Water Education Alliance for Horticulture and the University of Florida. Lucas said he has been so satisfied with the ozone treatment that a second system was purchased to treat the water in the flood floor, overhead hanging basket and boom irrigation systems in the rest of the facility. A custom-designed bio-filter system will provide a final treatment of the leachate runoff from the overhead basket and boom irrigation systems before the water is released into the pond. The bio-filters will remove remaining traces of fertilizers and other chemicals (i.e. fungicides, pesticides, plant growth regulators, etc.). The bio-filters and ozone treatment system will recirculate the pond water which will eventually remove any chemical residues that have been previously discharged into the pond. Lucas also installed a pond aeration system that is designed to generate 9.71 complete turnovers per day of all the water in the pond. The aeration system maintains a uniform temperature, clarity and oxygen level throughout the pond. It eliminates most algae, lowers turbidity and reduces pathogen levels, significantly improving this water source. Water treatment benefits Lucas Greenhouses head grower Joe Moore Jr. said the most significant benefit so far growing with the ozone system is “a substantial reduction in fungicide use”. Most of the crops are produced on flood floors, including a large poinsettia crop. Prior to the installation of the ozone system, the poinsettia crop was treated with a preventive fungicide application after rooted cuttings were planted. This treatment occurred when the plants were set out on the floor and then again during the third week of September and every four to six weeks through the third week of November. A final fungicide treatment was made prior to shipping. “With two seasons of experience with the ozone system, we are only making the preventive applications after rooting and prior to shipment with no applications in between,” Moore said. “With a little more experience, we may be able to eliminate even these applications.” Lucas’ spring crops are grown with no fungicide applications. This includes those crops on the flood floors, which tend to have higher pressure from disease pathogens. Moore said with a properly designed and installed ozone system it is possible to eliminate “most” fungicide treatments. He said it is critical to also use appropriate best management practices. Moore is still cautious about the results that have been achieved. “I still have some fear of disease infection from using recycled water and it will require another season or so of similar results to make us completely comfortable, he said” Benefits from installing the system have included reduced chemical applications, less fertilizer use, better plant health, zero or near zero water runoff and a higher level of grower confidence knowing the water has been treated properly. Overcoming obstacles George Lucas said the biggest obstacles to developing a water treatment program were finding the information and sufficient technology appropriate to our industry. “Clearly cost is always an important factor,” he said. “But developing confidence that recycled water was really suitable for growing crops and understanding how to monitor and manage fertigation, disease, pH and other components has been critical to our success.” Lucas said planning the treatment system prior to building the greenhouses would have definitely helped in the design and cost of the infrastructure. “We should have spent more time in research up front,” he said. “Which is why I said “quickly” is a dangerous word.” Lucas said one of the consultants he is working with on the company’s water treatment program asked him “What are your exact expectations?” The consultant asked Lucas to define his goals so he could understand what the grower wants to achieve once the system is complete. “Define exactly what it is you want and need, then go find the right people and the technology to accomplish that task,” Lucas said. For more: Lucas Greenhouses, (856) 881-0234; www.lucasgreenhouses.com. Al Zylstra is division manager, DRAMMwater, a division of Dramm Corp., azylstra@dramm.com; www.dramm.com. |
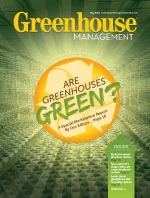
Explore the May 2011 Issue
Check out more from this issue and find your next story to read.
Latest from Greenhouse Management
- 2025 Proven Winners Horticulture Scholarship applications now open
- How to improve inventory and shipping management in the greenhouse
- Leading Women of Horticulture: Anna Ball, Ball Hort, and Terri McEnaney, Bailey Nurseries
- GM CEA HERB Part 2: A guide to increasing the sowing density of culinary herbs
- GM CEA HERB Part 1: Best practices for producing culinary herbs in controlled environments
- USDA fires experts on invasive pests, including Asian citrus psyllid, chilli thrips
- CEA Alliance celebrates bipartisan introduction of Supporting Innovation in Agriculture Act
- Dümmen Orange North America celebrating 25th anniversary in 2025