
Climate control can sometimes be a demanding and complex task in greenhouse environments. Growers must delicately balance lighting, humidity and temperature to optimize crop production and health, and often turn to both passive and mechanical systems to regulate the cultivation conditions.
These systems, in turn, can increase production costs, which either cuts into the growers’ margins or forces them to increase their sales price. That said, energy- and climate-smart implementation and use of these systems can allow growers to maximize plant quality and profitability.
Consider these tips and insights to help you maximize efficiency when managing heat and humidity in the greenhouse.
Resource-efficient heating and dehumidification strategies
Andrew Lee, global technical knowledge manager at RII member organization Grodan, recently led a European-based study with Philips Horticulture LED Lighting examining how to grow with low heat input while not impacting yield or quality.
The greenhouse trial used active dehumidification by Ammerlaan Construction, and with their other partners, including BASF, Ridder, Normec Groen Agro Control and Wireless Value, the group examined the impact of active air dehumidification on plant transpiration and nutrient uptake in a low heat input cultivation.
The study was built upon more than 20 years of greenhouse research related to heating and humidity management best practices, according to Lee.
In the early 2000s, “the research question regarding humidity control in greenhouse horticulture was, ‘Do we heat the greenhouse first and then vent?’” he recalls. “That research question was answered: It’s far cheaper to vent first than heat, because if you heat first, at some point you’re going to have to vent. And as you make the difference between the inside and outside air temperature greater, it costs you more money.”
In the decade following that revelation, energy prices surged, and growers looked toward climate screens to insulate the greenhouse.
“The research question then was for humidity control: ‘Do we keep the screens closed and vent above a closed screen, or do we gap the screens?’” Lee remembers.
The answer was that venting above a closed climate screen will offer a more uniform and stable greenhouse climate. Allowing the air above the climate screens to warm up before opening them will prevent cold air from being dumped on the crop (increasing the chance of condensation forming).
Grodan’s most recent study conducted with Philips Horticulture LED Lighting looked at how to stimulate plant transpiration for effective crop production and how to control the humidity with a lower (radiant) heat input.
It arrived on the heels of another energy price crisis that has seen HID lights replaced with LEDs, as well as growers using two climate screens. These setups have allowed greenhouse operators to reduce the temperatures at which they run their heating pipes from between 140° and 176° F (60 and 80° C) to no more than 113° F (45° C).
But lower pipe temperatures, double screens, LED lights and a minimum amount of radiant heat from the sun in winter caused growers to become concerned about the impact on transpiration and nutrient uptake (ml per mole light).
The Grodan/Philips study found that the stable greenhouse climate created by the dehumidification system and closed screens allowed for predictable water uptake and precise irrigation, as conditions remained consistent daily, making it easy to match water needs with transpiration.
Using a combination of convection evaporation via air movement supplied by an active dehumidification system, researchers swapped the hot, moist greenhouse air with cool, dry outside air, creating a humidity deficit that stimulated plant evaporation and nutrient uptake.
“At the same time, keeping the blackout and the climate screen closed for a total of seven weeks during the darkest, coldest days of winter, which is pretty much unheard of,” Lee shares, “we effectively saved 10 cubic meters of gas per square meter (approximately 32.79 cubic feet per square foot) and reduced heat input by over 50% compared to a reference grower.”
Lee says the group of research partners will be fine-tuning the experiment this coming lighting season in Europe, with a focus on improving energy efficiency in tomato cultivation.
The early results are promising, as “we’ve set the bar for what could be the new norm in energy-efficient greenhouse production, reducing gas consumption by half,” he says.
But Lee notes that whether this setup is cost-effective depends on a grower’s energy price balance. “The technology works, but of course, the investment is strongly dependent on how much you pay for your gas and your energy contract,” he explains.

Heating and dehumidification systems
Typically, greenhouses don’t need to be heated during the daytime, as the thermal energy from the sun is concentrated under the building envelope. However, heating may be needed at night, when temperatures cool. Additionally, cooler air has a lower capacity to hold moisture, leading to condensation buildup on surfaces and on plants, which can cause plant health issues.
Rather than simply heating the greenhouse air, Chip Seidel, head of business development for RII member organization Desert Aire, notes that commercial dehumidifiers often will be more efficient at managing the climate.
“Dehumidifiers are really an awesome tool because they convert latent energy into sensible energy efficiently, providing a drier, warmer space during most of the year,” he explains.
Running a mechanical dehumidification system at night can both reduce the moisture in the environment and add heat to it.
Passive systems and proper ventilation should be every grower’s first step in managing their cultivation climate during the day, but humidity can remain an issue, especially on those muggier days. In those periods, greenhouse operators may elect to button up their envelope and run a dehumidification system to manage that moisture load. The excess heat can then be dumped outside.
Even better, the byproduct heat can be captured and stored in a water tank for recirculation in the evening hours or used to heat colder groundwater or irrigation water, which in turn can make other systems more efficient.
“When you run cold water through an RO (reverse osmosis) machine, it uses a lot more energy,” Seidel notes. “We’ve had groups that say, ‘Hey, we want to have the ability to either use the heat for dehumidification and heating and be able to put it into our watering tank to keep that water up a little bit, and it takes a lot of energy to heat up water.’ A lot of times, we can dump all of (the dehumidifier) heat into that tank…like a great energy sink.”
Maintaining dehumidification equipment is also essential to their optimal operation. In particular, dehumidifier coils need to be kept clean.
“A lot of these (coil) fins are really thin, and they’re designed to have maximum surface area so they can transfer their energy,” Seidel explains. “If they’re all clogged up, then you’re not getting that really high heat transfer effect. … When that happens, the compressors have to work harder, and you’re putting a lot of stress on your unit.”
HVAC coil cleaning solutions can be purchased at most supply stores, Seidel says. Once the solution has been sprayed on, team members can simply brush off or use a jet of pressurized air to remove any dust, dirt or residue from the coils. Avoid using pressure washers, as these can bend or damage the coils, reducing their efficacy.
Evergreen Energy Partners (EEP) is an RII member organization whose mission as a full-service consulting firm is to help utilities connect their customers with expert knowledge and innovative solutions for commercial, industrial and residential energy efficiency programs. EEP Senior Solutions Manager Lauren Eagan highlights the opportunities that heat pumps present for greenhouse operators beyond dehumidifiers (and integrated HVAC-D systems).
“I’m really excited about the technology of heat pumps that’s coming out. There have been great advancements in heat pumps, particularly air-to-water heat pumps, which circulate water throughout a space,” she says. “They can cool or heat, so that really gives growers an opportunity to maybe cool the greenhouse if they haven’t been able to do that before, as well as better control and efficiency.”
Heat pumps use electric energy, which, depending on the local grid’s carbon footprint can be less carbon-intensive than traditional fossil fuel heaters used by some greenhouse operators.
Additionally, “manufacturers are doing a great job of producing lower global warming potential (GWP) refrigerants in them at the same time, having a really good efficiency,” Eagan notes.
Rebates and efficiency programs
System and structure design upgrades can be a costly venture for even the most well-funded greenhouse businesses, let alone for small- and medium-sized operators. Luckily, many utilities and governments have incentive rebates and efficiency programs to help cover the capital expenses associated with those upgrades — as long as growers can show the energy-saving potential.
To start down that path, Eagan offers two key pieces of advice: Reach out to the utility early and often, and start collecting data (if you’re not already doing so).
“A lot of growers, especially small ones that I see, will use inappropriate thermostats in their spaces,” Eagan notes. “I’ll see old residential thermostats that have not been calibrated, and that is so backward, because those plants rely so much on accurate temperature and humidity control and sensing.” She advises growers to have at least one wireless sensor in their cultivation environments — and ideally multiple sensors around the greenhouse.
Having multiple readings will both help build a baseline for a facility against which growers can compare system upgrades (and share with government or utility incentive providers) and identify any climate issues in the greenhouse, such as microclimates.
Fixing those microclimates can be as straightforward as patching leaks in the structure envelope. In the cases of polyethylene greenhouses that need sidings replaced, “that’s something that utilities can often help folks with,” Eagan notes. Depending on the grade of the film, polyethylene greenhouses need to replace their coverings roughly every five years (although some growers may stretch that to eight years).
Whether considering an update to a greenhouse envelope, an energy-efficient dehumidification system, a heat pump with a low-GWP refrigerant or a novel circularity system that reduces energy use and carbon emissions, utilities likely will need to know about the project before any purchases are made to offer rebates and incentives.
Thankfully, within the last few years, utilities have realized the value in working with greenhouses and indoor facilities, which has led to reinvestment in their controlled environment agriculture incentives, technical assistance and outreach.
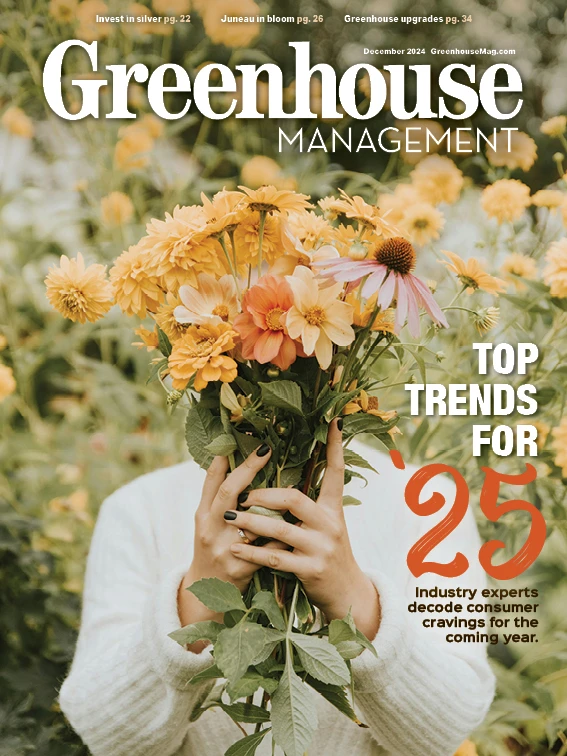
Explore the December 2024 Issue
Check out more from this issue and find your next story to read.
Latest from Greenhouse Management
- Pennsylvania Horticultural Society announces 2025 Gold Medal Plant winners
- GIE Media Horticulture Group wins five regional 2025 Azbee Awards of Excellence
- Terra Nova Nurseries introduces rust-free and disease-resistant heucherella
- John T. Nickel, founder of Greenleaf Nursery Co., passes away at 89
- Three tours offered at 2025 Farwest Show
- Garden Media Group announces sixth annual Women in Horticulture Week
- Star Roses and Plants announces National Knock Out Rose Day
- The Growth Industry Episode 4: How federal budget cuts are affecting horticulture nonprofits