
The plant shipping process involves considerable labor. Research has shown that more than 50 individual tasks are required to get a container of plants from the greenhouse to the retail outlet. Each of these tasks has a labor cost associated with it. When totaled, it equals your total cost for shipping the plants.
Develop a method to locate the right plants quickly
Many growers hire new or part-time employees for the shipping season. Most are not familiar with the type and variety of plants. With several hundred varieties, sizes and colors of plants grown, an orderly method of identifying and marking these is important. Plants may be grown in many hoophouses or spread out in a large gutter-connected range. Most greenhouses segregate the plants by type and color. Most also try to keep the like plants in adjacent bed or bench areas. This is not always possible, especially during the busy spring season, when transplants that come off the production line are placed in any available open space.
In many greenhouses, identification signs are placed next to each variety and color of plant. The grower is usually responsible for keeping the identification signs up to date. Frequently because of time constraints, this doesn’t get done.
Many times, the shipping crew boss walks long distances looking for the next plants on the order form while two or three employees wait until the right plants are found. This wastes valuable time during the rush season.

Use technology to speed the process
A handheld computer can be programmed using barcoding to identify and locate plants in the growing or shipping area. When plants are placed in the growing area, they are identified by a barcode. This can be on each container, as is sometimes required by the garden center, or on a sign located in front of the block. The location and count are entered into the computer.
When ready to ship, punching in the ID number will locate the plants and indicate how many are available. When plants are removed, they are subtracted from inventory, and the numbers are transferred to the computer at the office for invoicing. This saves considerable time in preparing the invoice.
Software can aid in supply purchasing, accounting, space needs and sales trends. When selecting a system, consider initial and yearly costs, frequency of updates, hardware needed, system support and available training. A web search will identify several companies with greenhouse-specific software.
Alternate methods
A method practiced by some growers is to pre-locate the plants before starting the assembly process. The crew boss or greenhouse grower locates plants needed to fill a particular order and places a colored ribbon on them for identification. Each order has a different ribbon associated with it.
Another method used by smaller growers is to total the number of plants by variety and color for all the orders for a day. Crews then collect and move the total day’s needs to a central assembly area, where the orders are filled. This adds extra handling but may be necessary when plants are in separate greenhouses. This method works well when orders are made up of a few plants or containers of many varieties.
Improvements in shipping methods and equipment are still high on most growers’ lists for improving overall plant handling efficiency. Significant reductions in cost can be realized by adopting computer technology that uses an identification system.
This article appeared in the March 2025 issue of Greenhouse Management magazine under the headline "No more seek and find."
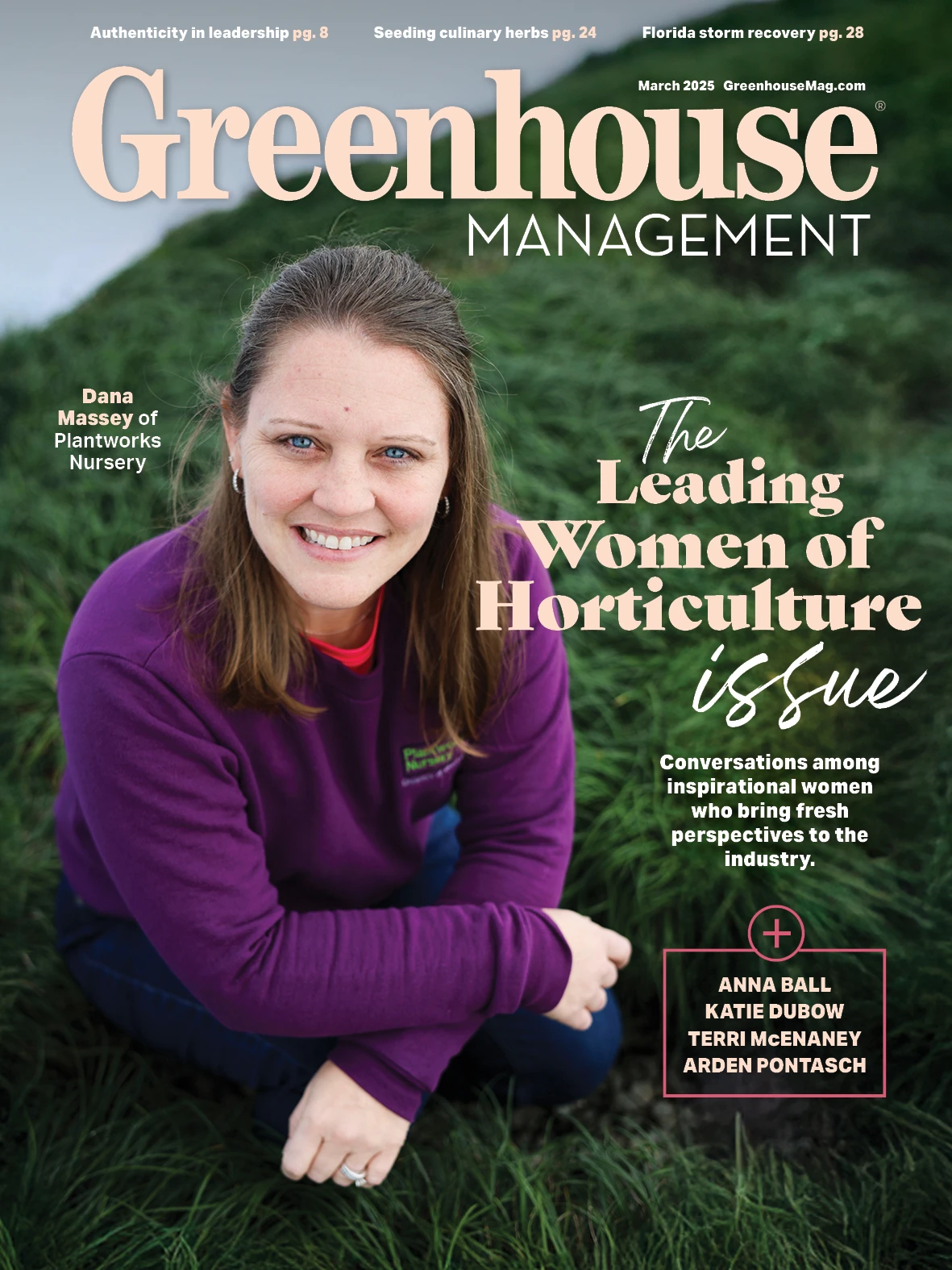
Explore the March 2025 Issue
Check out more from this issue and find your next story to read.
Latest from Greenhouse Management
- How Izel Native Plants is solving the native plant conundrum
- Trends: Proven Winners 2025 perennial survey shows strong demand
- Online registration opens for 2025 Farwest Show
- Cashing in with customization
- The Ball Seed Difference
- Lawsuit challenges new H-2 visa rules
- The Growth Industry Episode 3: Across the Pond with Neville Stein
- Green Gear: Battery-powered backpack sprayer and a hoodie