
room and waste energy.
It’s surprising how much heat an uninsulated pipe gives off. One grower with two large boilers that heat a gutter-connected range told me that before insulating the supply/return pipes in his boiler room, he frequently had to leave the windows and doors open so that maintenance personnel could work in there. Once the pipes were insulated, they had to add extra heat to make it comfortable.
Heat loss from pipes depends on several factors, including the diameter and length of the pipe, the water temperature inside the pipe, the air temperature surrounding the pipe and the length of time that the pipe is carrying hot water. Adding insulation slows this loss and lowers the fuel bill.

Estimating your savings
Table 1 gives approximate annual savings from insulating a linear foot of different diameter pipe with 1 inch of fiberglass or foam. It assumes 2,000 hours of annual use, which is typical of a heating system in a northern climate.
To use the table, select a pipe diameter and multiply the length of pipe by the savings from the table. For example, a grower can save $640 each year by insulating 100 feet of 2-inch diameter heating system pipe carrying 180°F water if the boiler is fired with natural gas costing $2/ccf. (Savings: 100 feet x $6.40/linear foot = $640).

Insulation material selection
Pipe insulating materials are selected based on where the pipes are located, maximum temperature of the water and the insulating value of the material. Most materials are available with formed pieces to fit over elbows and tees.
All pipe insulation materials are flexible or semi-rigid, except for those that are enclosed in a protective jacket. This makes them easy to install in tight locations. Depending on the material, the length of individual pieces may be 2 to 6 feet. These can be cut with a utility knife to the desired length. All materials can either be slit to fit over an existing pipe or come in two pieces.

Due to the low service temperature, polyethylene materials are fine for use in domestic hot water systems but should not be used where the boiler water is greater than 200°F. All other materials can withstand higher temperatures.
Table 2 gives the insulation factor for the different materials. The lower the K value, the better the insulation value and the greater the savings. All piping that carries hot water should have at least 1-inch insulation.
Installation time will depend on the material and access to put it on. Average time varies between 250 feet/day for the smaller sizes to 80 feet/day for the larger sizes. Scaffolding or a lift may be required in some greenhouses. Installation with your own labor can frequently be done during slack time to save money.
Payback for most pipe instillation will be less than two years. USDA’s Natural Resources Conservation Service Environmental Quality Incentives Program or state incentive funding may be available to offset some of the cost. For more information on grant programs, visit dsireusa.org.
John Bartok Jr. is an agricultural engineer, an emeritus extension professor at the University of Connecticut and a regular contributor to Greenhouse Management. He is an author, consultant and certified technical service provider doing greenhouse energy audits for USDA grant programs in New England. jbartok@rcn.com
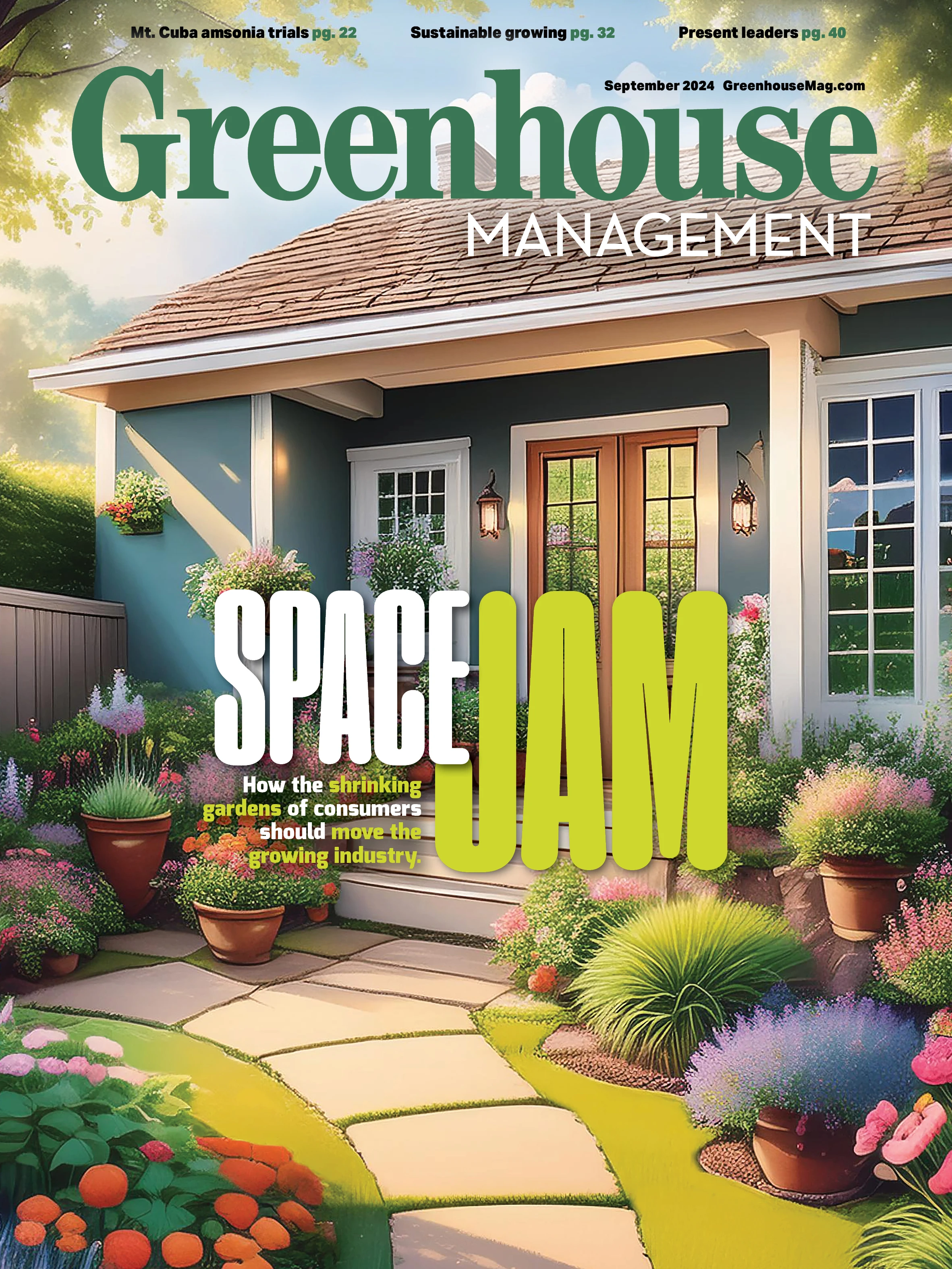
Explore the September 2024 Issue
Check out more from this issue and find your next story to read.
Latest from Greenhouse Management
- The Growth Industry Episode 3: Across the Pond with Neville Stein
- A nation of gardeners: A history of the British horticulture industry
- How Izel Native Plants is solving the native plant conundrum
- Trends: Proven Winners 2025 perennial survey shows strong demand
- Online registration opens for 2025 Farwest Show
- Cashing in with customization
- The Ball Seed Difference
- Lawsuit challenges new H-2 visa rules