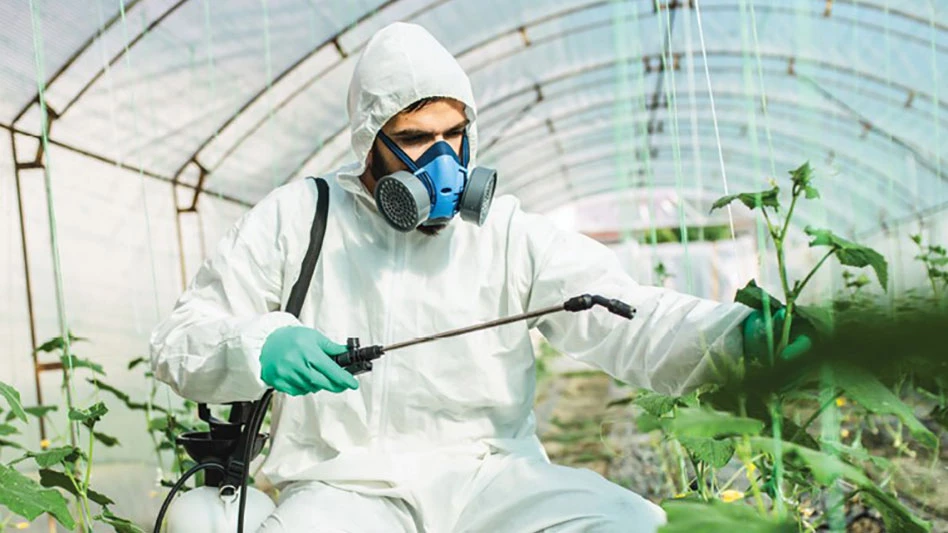

Although industrial hygiene isn't part of the daily vernacular at a greenhouse, this practice is applicable across the entire green industry.
“A good industrial hygienist should be aware of the different types of exposures in different industries,” Gooch explains. For Gooch, this means knowing what to look out for in different spaces. After knowing what those different exposures to hazards are, an industrial hygienist should be able to recognize where those specific hazards are, evaluate them and then finally control them.
Sentry hosted a webinar this May on industrial hygiene practices featuring Gooch as a speaker, as well as Ravi Vangipuram, senior industrial hygienist, and David McGill, senior industrial hygienist.
The webinar’s objectives were to “introduce industrial hygiene as a discipline, learn about different types of air sampling and noise sampling methods, and become familiar with industrial hygiene sampling plans.”
Workplace hazards
Workplace health hazards can be split up into four categories: chemical, physical, biological and ergonomic.
Chemical health hazards, including paint vapors, are the most common health hazards. Physical hazards include heat stress, cold stress and noise. Then there are biological hazards like mold and pathogens. Finally, ergonomic issues are things like awkward postures, high repetitions, heavy loads and moving great distances, which Gooch says can lead to musculoskeletal disorders.
Once growers know what the hazards are, the next step is making sure those hazards don’t affect their employees. To do that, growers must be aware of how environmental hazards can be internalized by employees, Gooch says.
“There are four main exposure entry routes where things can get into the body,” he explains, with the most common being through inhalation. “Inhalation can be problematic because the lungs are very sensitive, and they're meant to absorb as much as possible. They want as much oxygen per breath, so it's easy for toxins and contaminants to be absorbed into the body and into the bloodstream.”
The other three exposure entry routes are ingestion, absorption and injection.
There are two different types of exposure: acute exposure and chronic exposure. As Gooch explains, an acute exposure to a hazard would be a high concentration, short-term exposure that causes an immediate condition. Chronic exposure is “where you have a continuous or long periods of time at low doses of exposure, which can lead to illnesses later on in life,” Gooch says.
According to Occupational Safety and Health Administration (OSHA) data, some of the most common occupational diseases are respiratory illnesses such as occupational asthma or pneumonoconiosis, which Gooch defines as “a pneumonia-like disease spurred on by exposure to a particulate dust,” an example of which would be black lung disease in coal miners.
Another common type of illness is contact dermatitis, which occurs when employees work without protective gloves and come into contact with harmful substances.

Evaluating hazards
For Vangipuram, occupational safety and the fundamentals of industrial hygiene boil down to “figuring out where the exposures are and doing something about it.”
When evaluating employee exposures to chemical hazards, it’s important to establish a baseline. “We start at the current state, we evaluate employee exposure as it is now,” Vangipuram says. “We call that a baseline employee exposure. You quantify exposure and we treat that as a baseline and ensure that exposures haven't changed over time.” After establishing that baseline employee exposure, Vangipuram continues to perform ongoing evaluations to monitor if anything continues to change.
“That's ongoing evaluation,” he says. “OSHA requires you to do routine, ongoing evaluation.”
Two common evaluations that Vangipuram does are air exposures and noise exposures. Air exposures are most common in chemical agents, whereas noise exposures are often dependent on the length of the workers’ shift.
Air exposures have two types of sampling: active and passive.
Active sampling requires the use of an air pump to actively draw air through a filter media. This sampling is most often used for dust, mists, fumes, and gases. That air pump depends on the contaminant, the flow rate and the media it’s being filtered through, and an industrial hygienist examines those variables to figure out what to use. “Active sampling is a preferable way of sampling because by the very act of breathing, we breathe by forced air inhalation,” says Vangipuram. “It’s essentially an active flow, so if we actually force air through our nose, we're forcing air through a media.”
Passive sampling is also an option. For a passive sampling apparatus, “You simply take it out of the box and put it on the employee – on his collar, on his shoulder, somewhere within about 1 foot of his breathing area,” Vangipuram explains. Passive sampling doesn’t use pumps or hoses, so it’s simple. All that’s required is for the employee to move around in some manner to create air currents, which will take any contaminants from the air and put it through the media. Passive sampling is typically used for gases, vapors and organic solvents.
“This is not one-size-fits-all,” Vangipuram says. “It’s an industrial hygienist’s job to figure out what samples to take. That’s what we do.”
“The other type of sampling that we do are real-time meters,” Vangipuram says. “These are exposures that we measure real-time.” This can include using a direct reading instrument to take a measurement of things like carbon monoxide levels in the air.
Noise exposure can also be harmful, although it’s tricky.
“You might be exposed to harmful levels of noise and not know it,” Vangipuram says. “You could be sitting in a rock concert laughing, shouting, enjoying the ambiance, and you are exposed to probably 150 decibels, which is pretty darn loud. You enjoy it, but it's not good for your hearing.”
Working in a busy and loud facility can do similar damage to workers’ hearing, especially if they grow used to hearing the noise over time and start ignoring it. “That is why we do noise sampling.”
For noise sampling, Vangipuram looks at two criteria: hearing conservation and permissible exposure limit criteria. Hearing conservation criteria can trigger a hearing conservation program. Evaluating noise exposure can’t be done subjectively. It has to be quantitative and needs a simulator to provide a value over a whole shift to determine if the facility is at, above or below an acceptable noise threshold.
Sampling plans
After sampling and evaluating the present hazards, it’s time to create an industrial hygiene sampling plan.
According to McGill, “an industrial hygiene sampling plan is a structured approach to identifying and quantifying employee chemical exposures.” Importantly, McGill notes, this sampling plan should not be complicated. It should be a simple process of assembling a team, identifying any unique departments, identifying hazards in each department, assessing exposures and assigning reassessment frequency.
This team should consist of about four to six members, but no more than eight, and those members should be cross-functional and experienced. As for who should be on the team, McGill recommends a maintenance person, a senior operator, production people and QA people.
After assembling the team, the next step is to identify about six departments. Depending on the type of business, these could include departments such as production, maintenance, or shipping and receiving. In each department, identify the present hazards during routine tasks. What chemicals or noises are present? What ventilation controls are there? What equipment is involved? What PPE is there? Answer these questions to make the sampling plans.
Next is exposure assessment, which includes examining existing data and processes, as well as recently changed processes like new or relocated equipment and chemicals. When assessing exposures, rate them based on what percentage they meet of the occupational exposure limit (OEL).
Based on the assessment of exposures, determine how frequently to reassess those exposures. The closer an exposure is to the OEL, the more often it should be reassessed.
Anyone looking to improve their industrial hygiene practices can reach out to industrial hygiene specialists.
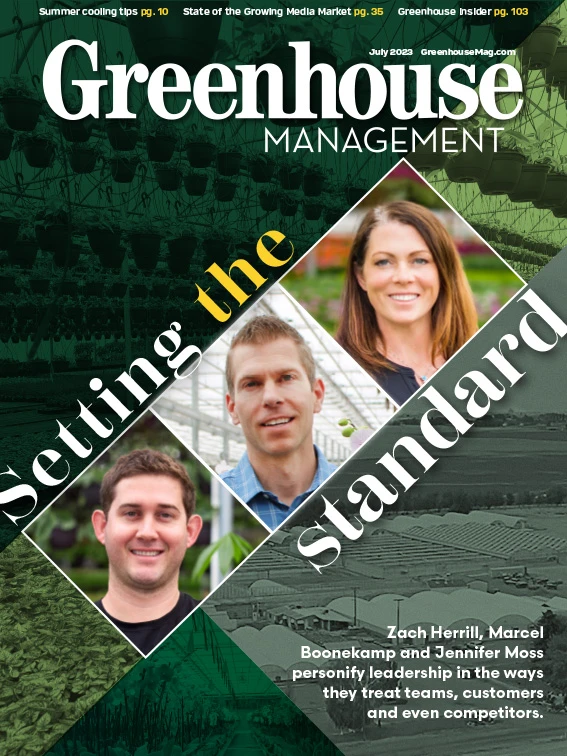
Explore the July 2023 Issue
Check out more from this issue and find your next story to read.
Latest from Greenhouse Management
- North Carolina Nursery & Landscape Association announces new executive vice president
- Plant Development Services, Inc. unveils plant varieties debuting in 2025
- Promo kit available to celebrate first National Wave Day on May 3
- Applications now open for American Floral Endowment graduate scholarships
- Endless Summer Hydrangeas celebrates 20 years with community plantings
- Invest in silver
- Garden Center magazine announces dates for 2025 Garden Center Conference & Expo
- USDA launches $2 billion in aid for floriculture growers