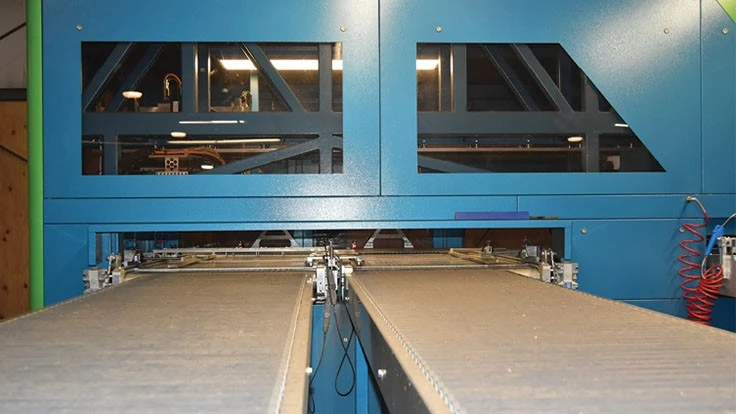

Producing about 100 million plugs every year, Kube-Pak in Allentown, New Jersey, adopted automation early to transplant plugs faster and reduce the headache of finding and training new labor.
In 1999, TTA USA made a 64-gripper transplanter specifically for the plug, rooted cutting and finished plant producer, says Kube-Pak General Manager and President Bill Swanekamp.
“We had probably 25 to 30 people manually transplanting — so, again, this is going back 20 years,” he says. “And it’s expensive, there’s a lot of management issues with people and we wanted to get away from that.”
Over the years, TTA USA’s technologies have continued to aid Kube-Pak’s operations.
This December, Kube-Pak will receive TTA USA’s PackPlanter Split-Frame Wireless 48 Gripper. It’s an upgrade — transplanters are faster now and the market has changed. Kube-Pak used to transplant 1,200 flats per hour. Now the business has significantly reduced its number of transplanted flats at 30,000 per week.
“Part of what has changed is that the demand for bedding plant flats has gone down and the demand for five-inch has gone up,” Swanekamp says. “So we don’t need as big of a machine now as we used to.”
Kube-Pak still does some hand-transplanting but has cut out about 90% of it. It has also automated about 70% of its plug-fixing with TTA USA’s CombiFix Gen II that it bought in 2018.
The plug-fixer works for growers who sell plugs, Swanekamp says, adding that Kube-Pak is one of about 10 major plug producers in the United States.

“We bought [plug-fixer] because we were having such difficulty getting labor to fix the plug trays,” Swanekamp says. “So that’s the main reason we got it. And the second reason is it has cut our expenses for fixing.”
Swanekamp, who calls the plug-fixer an “impressive piece of engineering,” says it has a two-step process to fix plugs significantly faster than even well-trained human labor could.
In the first step, the plug-fixer uses an infrared camera to map a plug tray to determine whether the tray has plants in it or just soil. It also uses jets to blow soil out of cells where there is no plant.
In the next step, the plug-fixer tells the user how many donor trays — which have plants in all their cells — he or she will need to do the fixing.
“Then there are these grippers that come down and take a good plant out of the donor tray and put it into the good tray,” Swanekamp says. “And then all the cells that were blown out are now refilled with good plants.”
After 20 years, Swanekamp says TTA USA continues to be a great vendor to do business with.
“They have good service, good equipment [and are] very reliable,” he says.
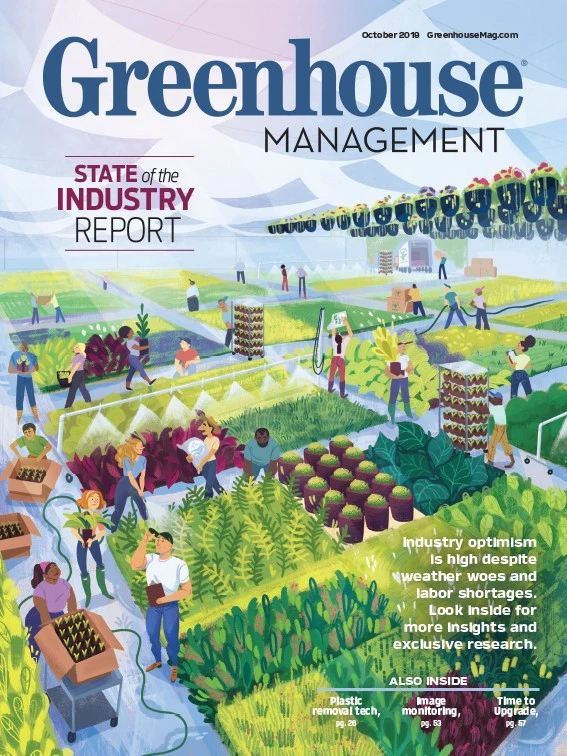
Explore the October 2019 Issue
Check out more from this issue and find your next story to read.
Latest from Greenhouse Management
- 2025 Proven Winners Horticulture Scholarship applications now open
- How to improve inventory and shipping management in the greenhouse
- Leading Women of Horticulture: Anna Ball, Ball Hort, and Terri McEnaney, Bailey Nurseries
- GM CEA HERB Part 2: A guide to increasing the sowing density of culinary herbs
- GM CEA HERB Part 1: Best practices for producing culinary herbs in controlled environments
- USDA fires experts on invasive pests, including Asian citrus psyllid, chilli thrips
- CEA Alliance celebrates bipartisan introduction of Supporting Innovation in Agriculture Act
- Dümmen Orange North America celebrating 25th anniversary in 2025