
Excluding insects from the greenhouse has many benefits including reduced pesticide use, less employee exposure to chemicals and higher-quality plants. Screens can be the first line of defense.
With greater resistance to pesticides, effective chemicals are becoming more difficult to find. Environmental concerns and stricter regulation on pesticide use are making the grower’s job more difficult. When designed and installed properly, screens will do a good job of exclusion.
Screens work best with exhaust fan ventilation systems. The positive airflow from exhaust fans gives a constant pressure difference. With a natural ventilation system, the airflow is dependent on buoyancy and wind for movement and varies considerably. This requires a greater amount of screen area.
Airflow
The airflow through screen material varies with the size of the openings. This is determined by the smallest insect you are trying to exclude. The openings for thrips are less than 0.006 inch, whereas openings for flies can be 0.040 inches. The larger the opening, the less material is blocking airflow. Table 1 shows approximate insect dimensions, typical insect screen openings and air reduction.

To provide adequate airflow for ventilation, the area of the screen that covers the vent/shutter opening must to be increased. This is usually done by providing a frame or structure over the intake that will support additional material. For a greenhouse with fans on one endwall and a vent or shutters on the opposite endwall, adding an extra hoop covered with screen material to the intake end will provide the extra area. For greenhouses with fans along one sidewall and vent on the opposite side, a lean-to structure or box frame over the vent will usually be adequate. Pleated screens are that attach to existing motorized vent windows are also available.
Sizing
The calculations for determining the amount of screen material needed are fairly complex and best determined by computer. Contact the manufacturer or supplier to get the needed size. Factors that affect the amount of screen area include:
Location:greenhouses in the South require more ventilation due to greater thermal load. The solar load may be 25-percent greater in Arizona as compared to a location in Michigan. Clouds and smog also affect this.
Existing greenhouse shading: Less ventilation and therefore screen material is needed if a thermal screen, exterior shade material, whitewash or evaporative cooling is in place.
Existing ventilation system: the number and size of fans, their output and air inlet size. After closing all openings except the intake shutters or vents, a monometer should be used to get the pressure drop (inches of static pressure) of the existing system before the screen is installed.
Size of the greenhouse: floor area and height.

Resistance of screen material: The opening size for thrips is much smaller, requiring three to four times the area of material.
Shrinkage: Allow for 1- to 2-percent shrinkage when installing the screen.
Maintenance
Keeping the screen system in good condition requires proper maintenance.
1. All openings (doors, gaps under baseboards) other than the screened vents should be closed to reduce access to insects.
2. Dust, dirt and pollen can plug up the tiny screen openings quickly. Washing with water from a hose and nozzle from the inside out works well. Do it on a warm day so that the screen dries quickly. Do not use high pressure from a leaf blower, as it may tear the material or alter the hole size.
3. A check on the operation of the system can be made by monitoring and recording the static pressure drop across the screen. When it increases above 0.4 inches of water, it probably should be cleaned.
Get curated news on YOUR industry.
Enter your email to receive our newsletters.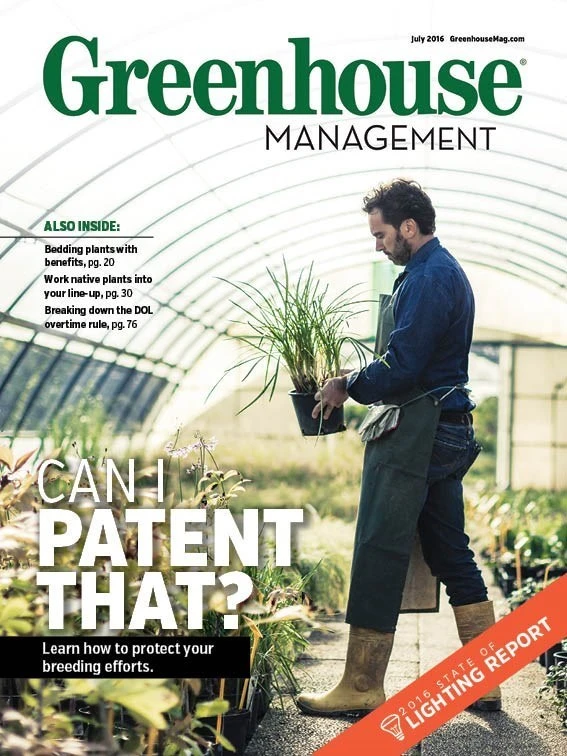
Explore the July 2016 Issue
Check out more from this issue and find your next story to read.
Latest from Greenhouse Management
- pH Helpers
- Society of American Florists accepting entries for 2025 Marketer of the Year Contest
- Sustainabloom launches Wholesale Nickel Program to support floriculture sustainability
- American Horticultural Society welcomes five new board members
- Color Orchids acquires Floricultura Pacific, becoming largest orchid supplier in U.S.
- American Floral Endowment establishes Demaree Family Floriculture Advancement Fund
- The Growth Industry Episode 3: Across the Pond with Neville Stein
- 2025 State of Annuals: Petal power