

In the first installment in this series, acclimatization factors associated with plant quality coming from a tissue culture lab were discussed. In this segment, we will discuss shipping and temporary storage prior to transplanting.
Shipping in Vitro plants
Physical damage
A primary shipping consideration is ensuring that plants are not physically damaged. Arrival of gel-disturbed tubs where plants have been found sticking to the walls is obviously an issue. This is often the result of shipper handling during transit, particularly of smaller packages that may more easily get tumbled in transit. It can also be due to the gel strength of the media, either due to low gelling agent concentration in the recipe or due to a media-making error. While too high of a gel percentage will impact plant performance, sometimes if shipping-induced gel breakage is frequently observed, a moderate increase in gel agent percentage can alleviate the issue. Where gel damage cannot be avoided, ex vitro shipping of plants immersed in Petri plates (or other containers) partially filled with autoclaved water, or on sterilized moist toweling, can be considered. Success for these ex vitro approaches will be greatest for stage 3 plants where shipping and temporary storage duration is not extended.
Physiological damage
Temperature is the single most critical factor in the shipping process. Plants in culture can generally withstand being cold during transit, and in fact may benefit being at 5-15o C due to the decreased respiration while in dark transit. However, freezing or near freezing of tissue culture plants should always be avoided. Freezing most frequently occurs from improper packaging practices of the freeze packs. Containers with plants should never be placed in direct contact with any frozen packs, and the frozen temperature of the freeze packs should be known. Is it 0o C or -150o C? While both are acceptable temperatures, they will influence the degree of separation and insulation of cultures from the packs. I developed a method over the years where I package frozen packs well away from cultures, and place a layer of cold, but unfrozen packs as a moderating buffer layer of significant thermal mass to avoid freezing events to the cultures while the frozen packs initially warm. Where culture vessels do not make up a large thermal mass themselves, addition of these cold packs in addition to freeze packs adds further cold mass, which can help reduce the warming rate and extent of the cultures.
When shipping during the extreme heat in summer or for extended shipping durations, one must balance avoiding freezing risk while ensuring the package reaches its destination at no more room temperature (~20o C). Several factors can help ensure this. The first is to pre-chill (but not freeze) cultures, dunnage and where possible even the shipping container itself for 12 hours prior to final packing. Packaging the shipper in a cold room or cool space then helps maintain this reduced temperature as the box or cooler is packaged until the container is closed up. Such practices greatly reduce the starting heat load inside the container. Another best practice is to pack cultures in tightly and fill any remaining space with enough dunnage (paper, foam, bubble wrap) to minimize free moving air space in the container and reduces changes of containers shifting in transit. Labeling the box as “Plant Perishable,” “Keep out of direct sun” and “This side up” is a best practice as it alerts workers throughout the shipping chain that the package requires special care and consideration. Note, use of printed label warnings will always garner more attention than those that are handwritten. Lastly, timing the packing and pickup by the carrier to be as close in time as reasonably possible, and obtaining the tracking number, are the last critical pieces of the shipping process.
In extreme situations of prolonged international shipping durations of a week or more, a double container (box in a box) can be considered, where the outside insulated box or ice chest containing only frozen packs becomes the initial buffer to absorb heat so that the inner container temperature is maintained for a longer period of time. I have successfully shipped bareroot plants from Florida to Australia for greater than a week using this type of method (see graph).

Test shipments
When receiving plants from a new laboratory location or vendor, a downloadable USB temperature-logging device should be included in the initial shipment. Where shipment of high-value germplasm is to be made, it is a good insurance policy to have the lab send you a test shipment before ever sending high-value germplasm. A test (or dummy) shipment containing plants of nominal value may also uncover any unknown freight logistics, broker or customs clearance issues that may delay the speedy transit of the package. Always consider possible holiday dates along the transit path and at the destination that could cause day-level or greater delays. Where a destination is deemed risky for any number of possible reasons, shipping high-value plants in more than one package and on different days should be considered.
Temperature monitoring
Where shipping conditions are erratic or unknown, including a disposable, USB temperature tracking device is a best practice for quality control and investigation when acclimatization issues arise. Such devices are readily available from the food transport industry. Having these devices take a reading every 10 to 15 minutes should catch any significant events should they happen. Knowing the actual temperature profile during shipping can be quite important as the feel of the TC containers upon arrival can be misleading. An example is where cultures warm after sitting on a very hot airport tarmac, then are stored in a cooler for 2 days before final delivery. Where possible, the most complete picture of the shipping environment is where tracking devices are placed both inside with the cultures and attached/taped on the outside of the shipper. This provides a dual temperature profile that allows the viewer to see when events occurred in the external environment, and how internal temperature was affected. Ahead of shipping, make receiving parties aware the devices will be present, and that you would like them to download and ship you the resulting data. Where routine use of devices is required, devices that can be reused are also commercially available.
Temporary storage prior to planting
Plants usually arrive as either stage 2 (unrooted) or stage 3 (rooted) plants in an agar-based media. These plants are photosynthetically active and growing when shipped from the lab. Lab light rooms are generally kept between 19-25° C (depending on species) with only moderate diurnal temperature swings to avoid excessive condensation buildup. Light levels generally are between 50-200 µM/m2 under a long day photoperiod of 16+ hours unless there is a species-specific need for short photoperiod. Knowing these laboratory conditions for TC plants is a critical first step in effectively determining proper storage conditions.
In a perfect world plants arriving from the lab are transplanted the same day of arrival, but this is very rarely the case, with transplant frequently stretching out for many days up to a week. This can at times place cultures in a no man’s land between lab and acclimatization spaces. Unless considered as part of the production system, improvised storage spaces often lack optimal temperature control and may have suboptimal lighting levels. The impact on resulting acclimatization outcomes is difficult to know without experimentation. However, it is prudent to give a hard look at this “storage” space when holding plants more than a few days. Ensuring the best possible shipping and storage conditions will increase the likelihood that transplant acclimatization and growth will be successful and optimal.
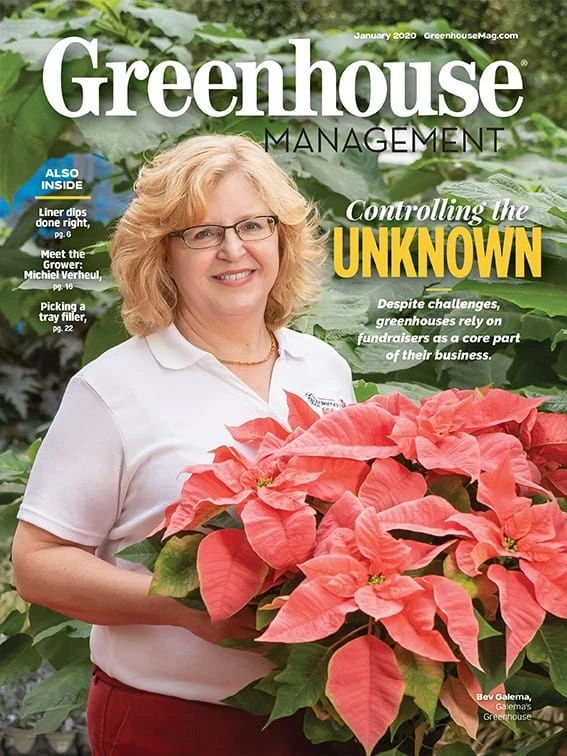
Explore the January 2020 Issue
Check out more from this issue and find your next story to read.
Latest from Greenhouse Management
- How Izel Native Plants is solving the native plant conundrum
- Trends: Proven Winners 2025 perennial survey shows strong demand
- Online registration opens for 2025 Farwest Show
- Cashing in with customization
- The Ball Seed Difference
- Lawsuit challenges new H-2 visa rules
- The Growth Industry Episode 3: Across the Pond with Neville Stein
- Green Gear: Battery-powered backpack sprayer and a hoodie