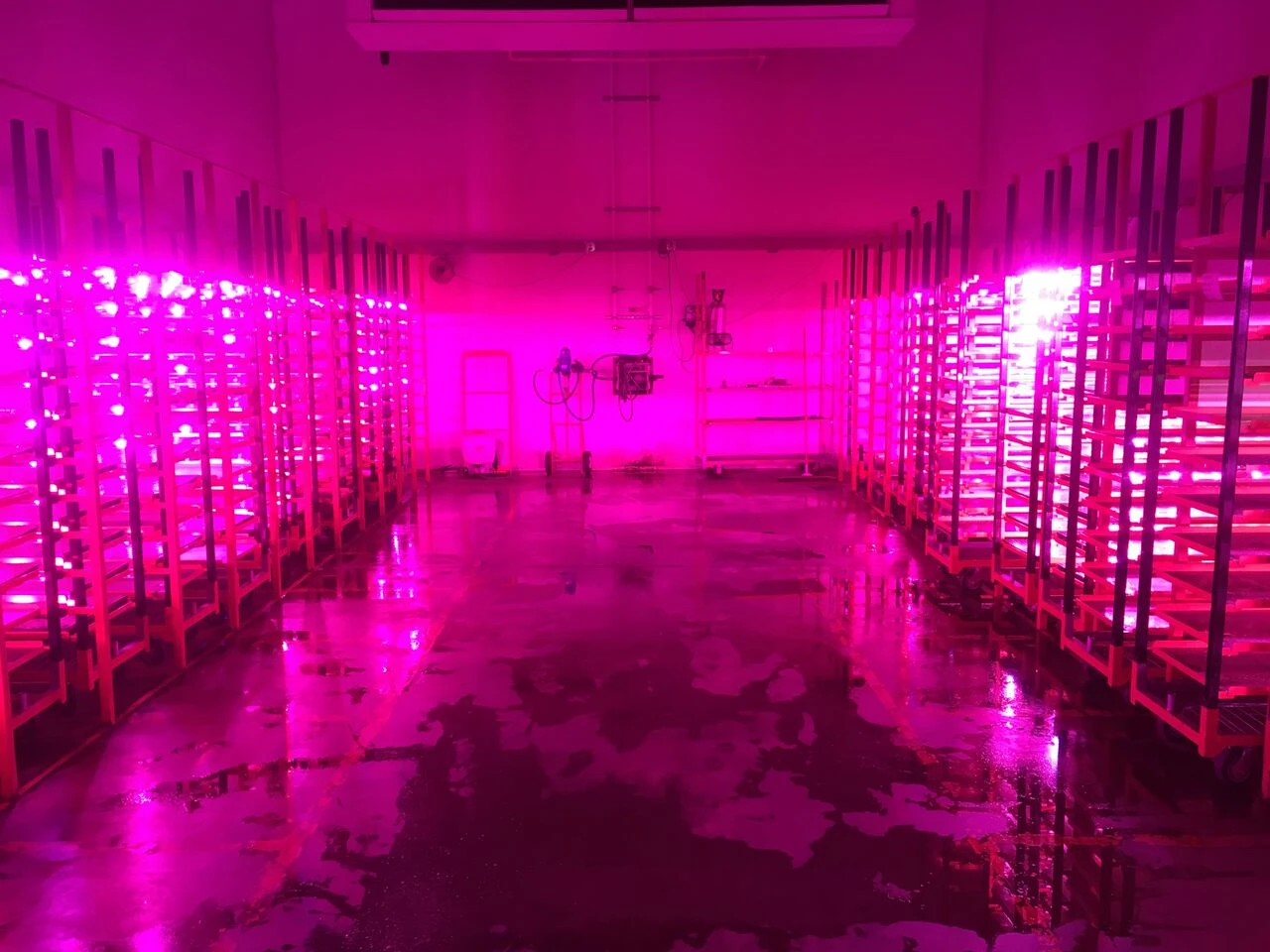
In Rapidan, Va., temperatures and light intensity rise to extremes that are not always conducive to acclimating stage three tissue culture in a greenhouse. To satisfy perennial orders in later times of the year, Battlefield Farms, an annual, perennial and poinsettia grower with 45 acres of undercover production area based in Rapidan, previously propagated sensitive tissue culture (TC) in the greenhouse. And it came at a cost.
“With the environmental conditions we had at the time, on certain varieties – certain cultivars – we were having up to probably 40 percent losses,” says Travis Higginbotham, research and development manager at Battlefield. “And it wasn’t due to practices – we had tried our best to manipulate the greenhouse as best as possible. We had taken an entire section and wrapped it. We had 50 percent shade cloth installed, we had foggers to increase the humidity to try to make it as successful as an acclimating area as possible. But we were still having a lot of problems with many different cultivars.”
Enter LED propagation research from Cornell University and Michigan State University and the Philips GreenPower LED Production Module. About two years ago, Higginbotham linked up with Philips to trial the module, and followed the company’s exact design specifications in a sole-source environment, emitting blue and red spectrum lights to the TC liners. “We started to get quicker rooting time, more compact growth and consistent growing throughout the entire tray, whereas, in the greenhouse, with the environmental conditions we had, the plants would grow all at different speeds in the same tray, and so it was very inconsistent in the greenhouse,” he says.
Based on trials that weren’t as successful as others, Higginbotham and his associates altered Philips’ design to fit specific applications that worked with different types of plant material. Originally, the lights were mounted above the plants. But he and his colleagues put the lights on their sides to fit a layered production method. The material is on about 30 carts, which each have 100 square feet of space, making the total production area around 3,000 square feet. When the trials began, Battlefield was acclimating around 600,000 TC liners. That number has since more than doubled.
In the controlled environment – a cooler – Battlefield Farms grows hundreds of different cultivars that they can separate by curtains and provide different photoperiods for, Higginbotham says. Depending on the species, he and his colleagues can change the photoperiod from 12 to 16 to 24 hours. “Now we’re starting to play around with a few different seed species, and kind of trying to get away from ordering plugs in that we had trouble germinating seed for, and now germinating our own seed in that environment,” he says.
In general, propagating in a completely controlled environment has its benefits, Higginbotham says. Carbon dioxide levels and temperatures, between 68 to 72 degrees, are consistent, and light photoperiod can be manipulated, he says. As a result, rooting has improved, growth is more compact and crop times are shorter. “With the ability to completely determine the environmental conditions, including the light, we’ve been able to speed up production probably up to a week,” he says.
Higginbotham and his associates at Battlefield Farms are thinking about how to improve lighting and production in the cooler even more. They are considering turning the cooler into a certified organic cooler, which is feasible given how temperature, irrigation and light are controlled. “Everything can be regulated by biocontrols, and we can now move forward and have a totally environmentally friendly system, without it just being environmentally friendly from energy savings from the light,” he says. “And we also are thinking now of doing different applications. So now, we want to go back and do applications with the lights from above, not just the sides, because we feel if we can do it from above with a higher intensity, we can probably propagate cuttings, and not just TC and seed.”
When he originally designed the lighting system, Higginbotham says he has frequently measured light levels, but he has seen consistent results over the years that have allowed him to measure less often. He uses a quantum sensor that reads micromoles to gauge light intensity. For each light pointing in from the side, the maximum output is 125 micromoles.
Between ornamental production, vertical farming for produce and cannabis cultivation, LEDs offer multiple possibilities, Higginbotham says. “I feel that there’s multiple uses for each individual spectrum, even going into the UV spectrum, that we can possibly maybe in the future use with LEDs,” he says. “I, personally, am interested in the possibility of how growers can become more environmentally friendly, not only in regard to plant growth with LEDs, but also with control of insects, control of mildews, Botrytis, other issues that growers have – not just plant growth – but also using this as an environmental tool for IPM and IDM.”
Photo courtesy of Travis Higginbotham
Latest from Greenhouse Management
- North Carolina Nursery & Landscape Association announces new executive vice president
- Plant Development Services, Inc. unveils plant varieties debuting in 2025
- Promo kit available to celebrate first National Wave Day on May 3
- Applications now open for American Floral Endowment graduate scholarships
- Endless Summer Hydrangeas celebrates 20 years with community plantings
- Invest in silver
- Garden Center magazine announces dates for 2025 Garden Center Conference & Expo
- USDA launches $2 billion in aid for floriculture growers