

Steve Garvey doesn’t look like a typical flower grower, so people are often shocked to learn that he’s spent his entire career in greenhouses. That’s why you can never judge a book by its cover — or a grower by the tattoos covering his arms.
Garvey repeatedly challenges the status quo to push greenhouses toward new technologies and growing methods. Since joining Dallas Johnson Greenhouses in Council Bluffs, Iowa as head grower four years ago, Garvey has implemented automation equipment and other improvements to improve quality and efficiency — resulting in expansion as the company continues to grow.
“My No. 1 priority is that we have top-quality plant material leaving our building,” Garvey says. “There’s a lot of plant material in the market that’s just okay, so I stress that we don’t want okay — we want top-quality.”
Evolving to improve
Garvey started working in the garden at a young age, alongside his grandmother. He pursued plants as he grew up — working at a greenhouse during high school, and then earning a horticulture degree from South Dakota State University.
After college, Garvey worked at a greenhouse for about a year, and then went to work at an independent garden center as head grower. The garden center didn’t even grow any of its own plant material when Garvey first joined, but by the time he left 15 years later, they were growing all of their annuals, perennials, shrubs and trees.
“Nobody taught me how to grow plants, so those first couple years, I just dabbled,” Garvey says. “Every year I got better, and every year I refined my approach using technology and chemicals.”
This hands-on experience taught Garvey that growers and greenhouses had to evolve to improve. When hand-watering and spraying several acres became too time-consuming, for example, he helped the garden center adopt automated watering booms for greater efficiency.

Embracing automation
When Dallas Johnson Greenhouses recruited Garvey four years ago, he was relieved to see that they already had booms and flood floors. But he saw opportunities to utilize these tools more effectively.
“A lot of people have technology, but they don’t use it when they should, or they use it when they shouldn’t, or they don’t use it properly,” Garvey says. “A lot of young growers don’t know what it’s like to not have technology. They don’t know how to water properly with a garden hose, so I teach them: ‘This is how you water properly with a hose, and this is how we use technology to make our day easier and more uniform.’”
By giving newer growers a glimpse into the once-manual processes that he learned the hard way, Garvey reminds his team not to take technology for granted. He says automation can make growers more efficient, but it shouldn’t replace the hands-on approach of monitoring crops the old-fashioned way.
“Someday, we’ll be able to control the booms from our phones, but I’m not going to give [my growers] that option,” he says. “If you don’t walk your crops, you don’t know what to [program the automation equipment] to do.”
The last thing Garvey wants is a team full of “recipe growers” who just push buttons to follow production schedules, instead of tuning into the tiny adjustments that plants need as conditions change.

“A recipe grower says, ‘I did this last year at this time, so I’m going to do it this year,’” he says. “Just because you did something last year doesn’t mean you necessarily need to do it this year. You’ve got to read the weather, read your customers and read the plants.”
For example, when Dallas Johnson switched soils last November and started using HydraFiber, there was no recipe to follow. Garvey and his team had to closely monitor how the new growing material held moisture and adjust their inputs and application rates to maintain high quality.
Growing more efficiently
Over the past two years, Dallas Johnson has added almost 17 acres — bringing the total to nearly 85 acres of covered production space spanning two locations. Garvey tries to walk (or bike) all of it once or twice a week while checking in with his team of 30 growers.
As Dallas Johnson has grown, Garvey has helped implement more automation technology to streamline production. About three years ago, the company installed an Echo Veyor conveyor shipping system to move plants from the greenhouse to the loading dock more efficiently.
“We used to struggle to get 30 semi-loads of product out a day, and it would take eight to 10 people nearly 12 hours,” he says. “Now with this Echo Veyor system, we can do 50-plus semis; we actually had a 74-semi day this year — with the same amount of people working a 10-hour day.”
This year, Dallas Johnson also added an automated sticking machine. “This takes our unrooted cuttings and sticks them for us,” Garvey says. “We can do about 11,000 of them an hour, so it will replace about 11 people, but the consistency is the same every time.”
As labor challenges escalate across the industry, Garvey says automation will be essential for growth and quality improvements.
“We can always do better,” he says. “We can always be more sustainable or more profitable, and that’s how I want to evolve.”
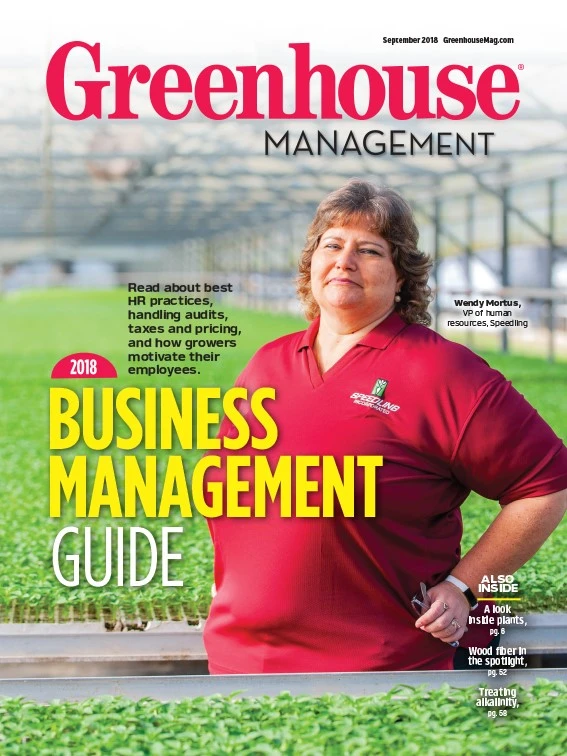
Explore the September 2018 Issue
Check out more from this issue and find your next story to read.
Latest from Greenhouse Management
- Flexible fungicides
- Super Charged Moon Juice from Moon Valley Nurseries now available nationally
- 2025 Proven Winners Horticulture Scholarship applications now open
- How to improve inventory and shipping management in the greenhouse
- Leading Women of Horticulture: Anna Ball, Ball Hort, and Terri McEnaney, Bailey Nurseries
- GM CEA HERB Part 2: A guide to increasing the sowing density of culinary herbs
- GM CEA HERB Part 1: Best practices for producing culinary herbs in controlled environments
- USDA fires experts on invasive pests, including Asian citrus psyllid, chilli thrips