

When Jessica Lowery started working in a small greenhouse 20 years ago as a freshman in high school, she experienced “a full spectrum of job duties from starting the cuttings to finishing the crops and sending to customers.” Now, as production manager overseeing a much larger operation at Creekside Nursery in Hempstead, Texas, her encompassing knowledge and enthusiastic passion continue to make every day exciting.
“Without plants, the world would be a very gray place, so I’m honored to work in such a unique industry,” says Lowery, who was promoted to her position in March 2018. “Working in greenhouses was always my favorite place to be, and I take pride in the crops I’m asked to care for.”
Although each day can be vastly different from the last, Lowery keeps her team focused on producing the highest possible plant quality for Creekside’s customers while embracing the changing landscape of the greenhouse industry.
The business of growing
At first, Lowery admits her high school job at the small wholesale greenhouse in her hometown of Brenham, Texas, was just a way to earn some extra spending cash. But she quickly fell in love with the atmosphere. By the time she was a senior, she knew she wanted to be a head grower someday.
Lowery studied horticulture at Texas A&M University, with an emphasis on greenhouse production and a minor in business. “I graduated in 2006 with a bachelor of science in horticulture,” she says, “and I started my career at Creekside Nursery just three days after graduation.”
Initially hired as an assistant grower in the perennial department, Lowery was promoted to propagation grower within two years. Since her recent promotion last spring, she continues to manage propagation while now overseeing the rest of production as well, “ensuring that all the departments are staying on schedule and getting quality product out the door to keep clients satisfied.”
“There’s some business behind being a grower,” she says, “so having a business background and basic knowledge in accounting, finance and management has really helped pay off with some of my new job duties,” which include everything from purchasing to managing personnel.



Open communication
Creekside’s production team is 250 employees strong, with 40 people dedicated to propagation. The team is headed up by five growers and five assistant growers, along with a tech services manager and plant health supervisor.
“Without the great team Creekside has in place, my job duties would be much more challenging,” Lowery says. “All the growers have been here 13+ years, except one who’s been on staff for about three years. We’ve all worked together for so long, it’s like we’re family.”
Lowery is constantly on the move monitoring operations across Creekside’s 500 acres of production space — 45 acres of which is under cover, with 25 acres dedicated to propagation. While plant quality is obviously a top priority, maintaining open communication among the production team is critically important to achieving that goal.
The production team meets once a week for “a sit-down roundtable discussion” to address upcoming needs and projects. Day-to-day, they communicate frequently via two-way radios and cell phones, while Lowery makes constant rounds to check on each department.
“Needless to say, I don’t sit still very long,” she says. “I always begin and end my days in the propagation area, ensuring that my employees are staying on task. The rest of my day is spent checking on various operations within the nursery.”
To maintain the highest possible productivity, Creekside cross-trains employees so they can move fluidly into other departments when daily work needs shift. “Team leads that are pulling orders may be taught how to run equipment or do production practices too,” Lowery says, “so no matter what the day holds, we can utilize the people who are here to get things done.”
Expanding innovation
Creekside Nursery is practically a one-stop shop for the landscapers and retailers it supplies — offering wholesale plant material “ranging from four-inch trays of annuals all the way up to 200-gallon trees, and a lot of material in between, including annuals, perennials, ground covers, shrubs and roses,” Lowery says.
Keeping customers satisfied requires steady growth and changes over time.
“We have expanded our production areas to keep up with customer demand. For example, we’re adding 16 acres this year to grow larger trees,” Lowery says. “We’ve also added potting machines with conveyors, and in 2014 we added four spacing robots to increase productivity, efficiency and plant quality without impacting our labor availability.”
By keeping customers’ expectations top-of-mind and leveraging her understanding of the entire production cycle, Lowery stays flexible to make the most of these changes.
“Keep your eyes and mind open to the changing trends within our industry, whether that’s adapting to new plant varieties or business innovations,” she advises other growers. “We need to rely on fresh new ideas to stay relevant.”
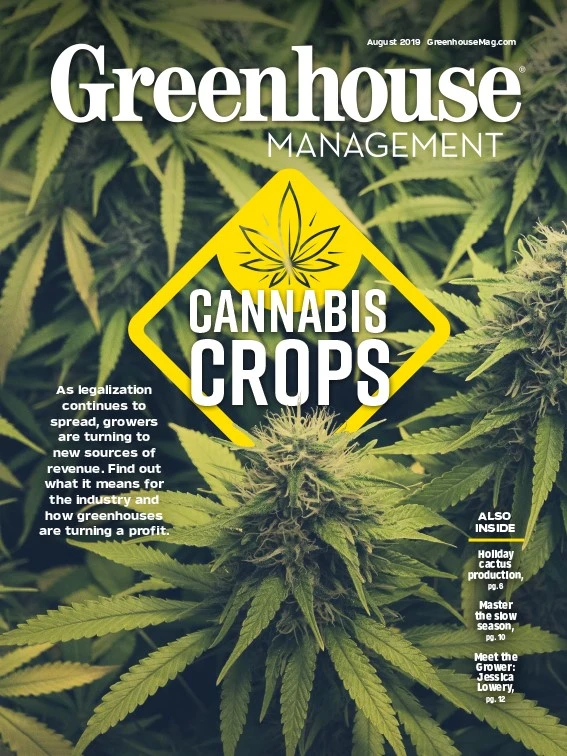
Explore the August 2019 Issue
Check out more from this issue and find your next story to read.
Latest from Greenhouse Management
- Flexible fungicides
- Super Charged Moon Juice from Moon Valley Nurseries now available nationally
- 2025 Proven Winners Horticulture Scholarship applications now open
- How to improve inventory and shipping management in the greenhouse
- Leading Women of Horticulture: Anna Ball, Ball Hort, and Terri McEnaney, Bailey Nurseries
- GM CEA HERB Part 2: A guide to increasing the sowing density of culinary herbs
- GM CEA HERB Part 1: Best practices for producing culinary herbs in controlled environments
- USDA fires experts on invasive pests, including Asian citrus psyllid, chilli thrips