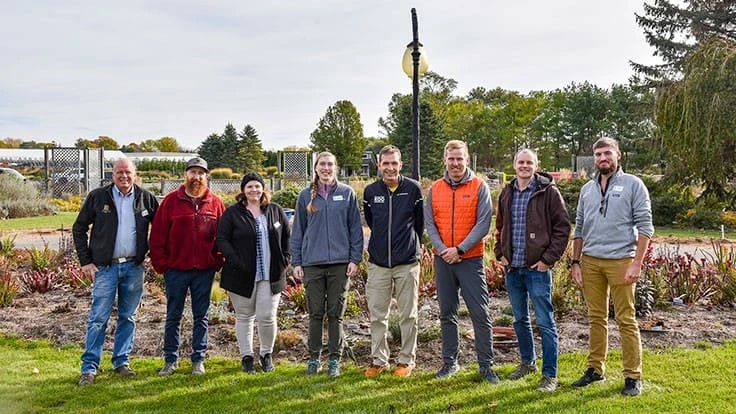
_fmt.png)
Drew Koschmann developed his love of the outdoors as a child, taking nature walks in state parks with his father, a retired science teacher. After high school, Koschmann began to study natural resources, but a side job at a local greenhouse changed his career trajectory. Now, as a head grower with 18 years of experience, Koschmann is passing down his plant knowledge as he innovates more efficient ways to grow.
After switching his major to horticulture production at Purdue University, Koschmann started an internship at Midwest Groundcovers in his home state of Michigan. By the time he graduated, they offered him a role as perennial grower. He spent eight years there, eventually taking over as nursery manager before moving to Andy Mast Greenhouses, where he served as head grower for four years producing annuals.
That’s when the head grower position at Walters Gardens opened up, and Koschmann jumped at the opportunity to get back into growing perennials.
“I had come to know Walters Gardens pretty well from working at Midwest Ground Covers, and I had purchased a lot of plants from them,” he says. “I was really impressed with the high quality that came from Walters.”
Koschmann joined Walters Gardens in 2015. Since then, he’s played a pivotal role in building the team and the automated processes that help the company produce more than 1,000 varieties of perennials in 13 acres of greenhouse space.
Increasing efficiencies
In addition to the greenhouse, display gardens and R&D beds fill out Walters Gardens’ property in Zeeland, Michigan. “We’ve really maxed out our main facility,” Koschmann says.“So we decided to look at adding acreage.” The expansion began this fall, with ongoing plans calling for “adding a couple more acres for production next year,” he says.
Meanwhile, to make the most of the space on-site, Koschmann relies on technology to optimize the greenhouse conditions for finishing various crops throughout the season.
_fmt.png)
“We’re receiving tissue culture cuttings throughout the year, so we’ve got to have warm spots in January. We’re holding vernalized plugs, so we’ve got to have cold areas, as well,” he says. “And, since we’re doing a lot of production out-of-season for hostas and hibiscus, we’re proactive in using LED and HPS lights to help them finish.”
About five years ago, Walters Gardens built a 15,000-square-foot propagation facility, referred to as the acclimation range, to house trays of fresh cuttings. Koschmann worked closely with the production manager and maintenance manager to develop the range — which is decked out with high-tech environmental controls, automated boom irrigation, heated floors, shade curtains and a fogger system.
“We’ve been happy with that [automation, because it] helps us manage the temperatures, irrigation, and humidity levels we need for the crops to finish on time,” he says.
Sharing knowledge
Throughout the week, Koschmann keeps tabs on plant progress by meeting one-one-one with his three lead growers, each of whom manages five section growers. An integrated pest management (IPM) team of three people also supports his team. During peak season, Walters Gardens supplements its staff of about 200 employees with an additional 100 workers through the H-2A Temporary Agricultural Employment program.
“That’s been really exciting to see how our section growers have been able to train H-2A labor to help with managing crops,” Koschmann says. “We’ve been working with a lot of the same employees for the past three years, so they’ve become really important in our propagation area, and every year they’re learning more and more.”
Koschmann holds growing team meetings every week to troubleshoot issues by leveraging the various perspectives and expertise of his employees. With decades of knowledge between them, this team is critical to the company’s success.
“We’ve worked really hard to hire experienced people,” he says. “The lead growers have brought a lot of talent to the team. The thing I really love about being here is if a question comes up, there are [growers on staff] I can ask to help me through.”
In fact, Koschmann encourages his lead growers to become experts in their own specialties. For example, one of the lead growers oversees automation, while another one helped develop the company’s internship program. “We’ve been able to bring in some high-quality individuals through our internship program that are still here working for us,” Koschmann says.By focusing on collaboration between growers, staff, seasonal workers and interns, Koschmann is cultivating a strong team at Walters Gardens. Leveraging their combined expertise is key to the company’s growth and innovation.
“Growing is a team sport,” Koschmann says. “You should make your judgment calls based on advice from your team. It’s smart to surround yourself with strong talent, [people who] have skills that are different than your own, [because you’re] always learning from each other.”

Explore the December 2021 Issue
Check out more from this issue and find your next story to read.
Latest from Greenhouse Management
- North Carolina Nursery & Landscape Association announces new executive vice president
- Plant Development Services, Inc. unveils plant varieties debuting in 2025
- Promo kit available to celebrate first National Wave Day on May 3
- Applications now open for American Floral Endowment graduate scholarships
- Endless Summer Hydrangeas celebrates 20 years with community plantings
- Invest in silver
- Garden Center magazine announces dates for 2025 Garden Center Conference & Expo
- USDA launches $2 billion in aid for floriculture growers