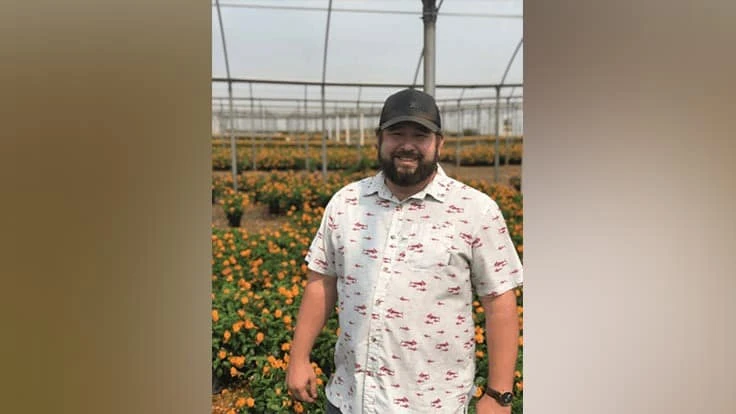

Brett Alldredge may not work at his father’s garden center anymore, but he still gets to work alongside several family members doing what he loves. In his new role as production manager at Greenleaf Nursery, Alldredge cultivates the plants and people around him to produce a high-quality product.
“I get to work with people and plants,” says Alldredge, whose wife and brother also work at Greenleaf. “People are just as diverse as plants, so you get to meet all kinds of personalities and grow all kinds of plants — and try to solve problems for both of them.”
Family roots
Alldredge grew up in the horticulture industry, working at the retail nursery his father owned in Midland, Texas. By age 13, he was spending weekends watering and weeding tree rows at the family business. As he got involved in different aspects of the operation, he learned more about the plants they sold and the people who bought them.
“I saw a lot of opportunity in this industry,” Alldredge says. “Customers come to you with a problem, looking for a solution, so I see myself as a problem-solver.”
Embracing his problem-solving aptitude, Alldredge went to college to study engineering, but soon realized it wasn’t the right fit. He earned a business degree instead, and after he graduated in 2013, he felt called back to horticulture.
He followed his brother to Greenleaf Nursery in El Campo, Texas. While working there in quality control and customer service (before serving as pest management supervisor for several years) Alldredge met his wife. When the head grower position opened at Seville Farms in the southern tip of the state, Alldredge moved there to expand his tropical-growing experience. Then, when an opportunity for advancement came at Greenleaf, he returned — taking on the role of production manager in the fall of 2019.

Tribal knowledge
Alldredge manages production across Greenleaf’s 500-acre facility, leading a team of four growers who oversee separate divisions. Division one is mostly comprised of shade and over-winter structures where camellias, azaleas and Zone 9 crops grow. Division three, by contrast, is entirely outdoor, full-sun production of roses, boxwoods, junipers and other trees. Divisions two and four combine sun and shade — rounding out Greenleaf’s woody-ornamental mix with hydrangeas, nandinas, various vines and shrubs.
Each grower manages a crew of 15 to 20 employees responsible for maintaining hundreds of cultivars, which are sold to retailers and rewholesalers. Although one of the growers has 15 years of experience, the other three stepped into grower roles just more than a year ago. Since then, Alldredge has been focused on training.
“I often forget that they don’t know what I know, so I have to make sure I’m covering all the basic growing principles that I’ve learned over the last 20 years,” Alldredge says. “You really have to overcommunicate things that you take for granted from your knowledge and experience, and remember that you’re an educator.”
Alldredge has a deep well of information to pull from beyond his own experience. Greenleaf’s growers have been sharing plant know-how for 75 years. “We’ve got a lot of historical documentation that we rely on,” Alldredge says, “so I’m passing on the history and knowledge that was passed on to me.”
These constantly updated documents contain production details like watering needs, shearing techniques and temperature points at which plants need protection from the cold. As helpful as this historical data is, Alldredge emphasizes that it doesn’t replace time in the field.
That’s why he spends several hours every day driving through the production space with each grower to monitor their crops. He also expects growers to walk at least one-third of their areas each week. Meanwhile, crop scouts report back about pressure from disease, insects or weeds, and other integrated pest management or fertility concerns. “As new problems present themselves, we change our practices to meet the needs of the plant,” Alldredge says.

Team accountability
Using decades of detailed production data, Greenleaf’s leaders set high standards for their people and the plants they produce.
“Every single task we do is monitored for productivity, and that’s the most important part of our business,” Alldredge says. “We set standards for how many units per manhour we should complete, whether it’s shearing, staking and tying, or spraying, based on peak efficiency. So, if we have a new grower, he doesn’t have to guess how quickly crews should perform those tasks. They know whether or not they’re being productive.”
Foremen document their crews’ daily productivity for certain tasks; supervisors then record that data onto spreadsheets, which are reviewed in weekly grower meetings. This keeps the team accountable to company standards and schedules, while identifying ways to improve efficiency.
Greenleaf’s commitment to quality and continuous improvement hasn’t wavered over its 75-year history. By upholding these standards, Alldredge helps to continue a legacy of success.
“We’re willing to adapt to market changes as they come,” Alldredge says, “but we always maintain our highest standards by not cutting corners on quality.”

Explore the June 2020 Issue
Check out more from this issue and find your next story to read.
Latest from Greenhouse Management
- Grant awarded to test western U.S. wood species for use as wood fiber potting substrate
- Pennsylvania Horticultural Society announces 2025 Gold Medal Plant winners
- Oasis Grower Solutions announces new Southeast territory sales manager
- A nation of gardeners: A history of the British horticulture industry
- Last Word with Angela Labrum, Bailey Nurseries
- Iowa plant supplier Plantpeddler building retail complex
- This month's Greenhouse Management magazine is about native plants and sustainability
- The HC Companies, Classic Home & Garden merge as Growscape