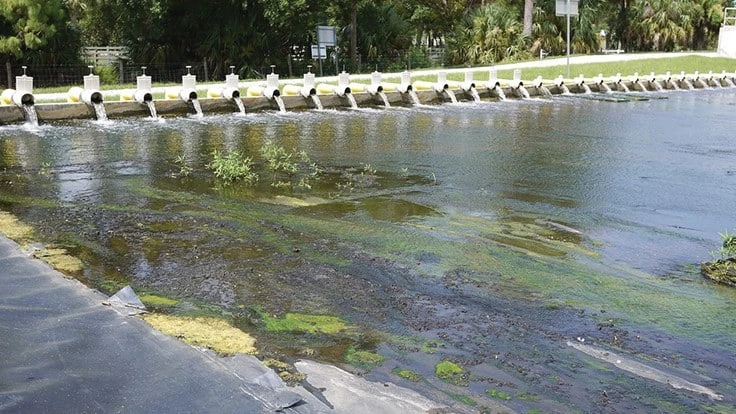

While you are most likely familiar with traditional treatment technologies like mechanical filtration, chlorination and ozonation, you may not be as familiar with biological and ecological treatment technologies. Innovative ecological treatment methods such slow sand filters, bioreactors and algal turf scrubbers are low-cost, low-energy technologies that harness the power of naturally occurring microorganisms to remediate nutrients, agrichemicals and pathogens in water.
Additional benefits of using these technologies include no need for chemical input, no production of unwanted disinfection by-products, no need for technical instrumentation or specially trained personnel, low operating costs and minimal maintenance. Installation costs of these systems typically range from several hundred dollars up to around $10,000, depending upon the volume of water to be treated. These costs are substantially lower than installation, maintenance and labor costs of other disinfestation and remediation technologies.

Slow sand filters
European horticultural growers have been using slow sand filters (SSFs) since the early 1990s to remove plant pathogens from recycled irrigation water. However, the technology is actually much older than that — SSFs have been used since the early 1800s to clean contaminants from water for human consumption. Today, SSFs at nurseries are primarily used to remove plant pathogens, including Phytophthora, Pythium and Fusarium. However, recent research has also shown that slow filters containing substrates other than sand (such as pumice and rockwool) may be able to effectively remediate pesticides and even nutrients from irrigation water.
SSFs consist of three major components (Fig. 1):
- Sand (or other substrate, top layer) – facilitates the purification process, typically about 2 to 4½ feet deep
- Gravel (middle layer) – supports the sand bed and prevents sand from clogging the underdrainage
- Underdrainage (bottom layer) – Captures cleaned water and allows for movement of water through the system
The water reservoir is placed on top of the sand layer and should be maintained at a depth of about 3 to 5 feet to maintain the necessary water pressure to ensure consistent flow through the SSF. Recommended filtration rates range from about 150 to 350 gallons per day per square yard of surface area. So, if you have a 15-foot diameter tank installed, you may be able to treat up to about 7,000 gallons of water per day onsite. While faster flow rates may still achieve sufficient remediation, the filters would be more likely to clog and thus require more frequent maintenance. The ability of the filter to treat water at faster flow rates depends upon the quality of the water entering the filter. If the incoming water was previously held in a settling tank or pond, or has been pre-filtered to remove any organic solids or sediment, higher flow rates can be achieved. The quality of the sand is also critical for optimal treatment — sand should be pre-washed, and grains should be about 0.01 inch (0.3 mm) in diameter, or about 60 mesh.
How exactly does a bunch of sand and rock remove plant destroyers like Phytophthora? Well, we’ve got microorganisms to thank for that. Over the course of about three to four weeks, a biologically active film layer naturally forms in the top few inches of the SSF. These microorganisms help to trap and degrade pathogen contaminants. Periodic maintenance, including the removal of the first few inches of sand, is required to maintain the designed flow rates through the SSF. Installation of two SSFs in parallel is recommended for horticultural applications — this way, while one SSF is shut down for maintenance, the other can remain in operation. However, remember to start cycling water through the alternate filter about a month in advance of use to allow that crucial microbial layer to form at the surface of the SSF.

Bioreactors
Agricultural denitrifying bioreactors, sometimes called carbon beds or carbon walls, are lined trenches or containers filled with a carbon-rich material, such as woodchips or woody substrate. Bioreactors are commonly used to remediate nitrate-rich irrigation runoff and have been applied extensively in agricultural production around the world, including in corn and soybean fields of the Midwest. Bioreactors installed at the edge of row crop fields of the Midwest have been reported to be as large as 120 feet long and 25 feet wide and treat drainage from up to about 80 acres of production area. Sizing of the bioreactor is dependent upon size of production area, estimated irrigation runoff/drainage amount and nutrient load. Experimental bioreactors have been installed at nurseries and greenhouses in the U.S. These horticultural bioreactors are typically smaller than those currently being used in row crop agriculture — on the order of just a few cubic yards and can handle high runoff flow rates without flooding production areas. While the longevity of woody substrate in bioreactors is still being researched, current estimates range from around 10 to 20 years. Both hardwood and softwood substrates have been used in bioreactors.
The typical bioreactor layout (Fig. 2) allows for irrigation drainage water to enter the bioreactor on one side, flow horizontally through the bioreactor via a series of perforated pipe and exit the bioreactor at the opposite end. Naturally occurring microorganisms populate the carbon-rich woody material and reduce nitrate as part of their everyday routine. Flow control structures — one at the bioreactor entrance to divert water and another at the exit to control water height — may be used. Stop logs in the control structures may be raised or lowered to control flow rate. Bioreactors may also be designed to allow for bypass flow during peak flow conditions.
While bioreactors are extremely effective at removing nitrate from water (with removal efficiencies up to 100%), unintended negative consequences of bioreactor use may include the release of greenhouse gases. These side effects are currently being investigated and may be alleviated by maintaining proper flow conditions through the bioreactors. Recent research has revealed that in addition to nitrogen andphosphorus, some types of bacteria and herbicides may also be remediated by bioreactors.

Algal turf scrubbers
Algal turf scrubber (ATS) systems consist of screens covered with attached algae (Fig. 3). Nutrient-rich water is typically pumped over these screens in a shallow trough, or even in open water. The attached algae use the power of the sun to uptake nutrients like nitrogen and phosphorus. Because algae grow so quickly, this technology removes nutrients at a very high rate. It is important to remove (scrape off) the algae from the screens about once a week, as this will rejuvenate the algal community and promote high growth rates. The harvested algae is incredibly rich in nutrients, and thus can be used as a substrate amendment, fertilizer or biofuel feedstock. These ATS systems have been shown to remove almost a pound of nitrogen per 10 square yards per day. Optimization of ATS systems depend on several factors, including flow rate, flow type (pulsed vs. continuous) and pH. Research on how these factors influence efficiency of ATS systems is currently being conducted.
Combination treatments
While many single traditional treatment technologies, as well as the ecological technologies described above, can effectively remediate common agricultural contaminants from water, the combination of several of these technologies in series or “treatment trains” may result in the most efficient contaminant removal, aka the most bang for your buck. Unfortunately, there is no single treatment system out there that will effectively manage all types of contaminants. The types of technologies that should be used in combination treatment trains depends on site conditions, the types of contaminants you’re interested in targeting and your budget. The use of treatment trains for water treatment technologies in container-grown crop production is an emerging topic of research, as little work has been done regarding treatment train efficacy and order of technology application for targeted contaminant removal in agricultural production systems.
Reliable access to fresh water is an increasing concern for many growers, as water supplies continue to decline due to overuse and increased incidence of drought. Additionally, more regulations on water withdrawals, water-use efficiency and quality of irrigation runoff water entering surface waters are being implemented. Therefore, more and more growers are looking into ways to remediate and reuse their irrigation runoff water onsite. The ecological treatment methods discussed in this article are not only low-cost and low-energy but are also safe and easy to use. Implementation of slow sand filters, bioreactors and ATS systems expand the tools available to the green industry to facilitate more efficient and sustainable water use and management. Effective remediation of contaminants, low costs and environmental stewardship do not have to be mutually exclusive. Consider adopting new and nontraditional ways to manage water to meet your irrigation water demands.

Explore the August 2021 Issue
Check out more from this issue and find your next story to read.
Latest from Greenhouse Management
- USDA fires experts on invasive pests, including Asian citrus psyllid, chilli thrips
- CEA Alliance celebrates bipartisan introduction of Supporting Innovation in Agriculture Act
- Dümmen Orange North America celebrating 25th anniversary in 2025
- CEA HERB Part 1: Best management practices for culinary herbs
- Lawsuit challenges new H-2 visa rules
- CEA HERB Part 2: A guide to increasing the sowing density of culinary herbs
- Illinois Landscape Contractors Association changes name to Landscape Illinois
- 2025 Proven Winners Horticulture Scholarship applications now open