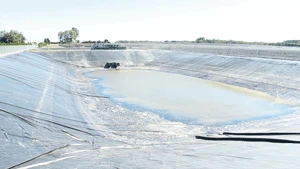
Ornamental growers across the country need to be concerned with the management of irrigation water as fresh water is depleted on a global scale. In anticipation of water restricting regulations, several growers in New Jersey have taken pro-active steps to reduce their dependence on fresh water by investing in recycling technology. This series highlights the costs and benefits of disinfecting and recycling irrigation water in large-scale production. Look for more grower profiles in upcoming issues of Nursery Management.
For more than 20 years, Overdevest Nursery in Bridgeton, N.J., has been collecting and reusing irrigation runoff. It was a necessary move before switching to container production, says owner Ed Overdevest. Ed bought the 150 acres he uses for container production from his parents in 1988.
“We decided to introduce container production. But before we did that we realized that we would have additional irrigation issues to deal with and we wanted to make sure that we were dealing with runoff in a proactive way,” he recalls.
One of the nursery’s first steps was to put in a tail water recovery system to capture the irrigation runoff, which led to a chain of other considerations.
“Once we had [the tail water recovery system], we had to figure out what we were going to do with the water, and our intention was to recycle it. It made sense from a variety of points of view, and that raised another issue — if we recycled the water what were we going to do to prevent recycling diseases?”
He proactively installed one of the first chlorination disinfection systems in New Jersey. This system has allowed him to collect and reuse his runoff for more than 20 years. His goal is to “recycle the water but not recycle any disease issues.” Ed invested in water recycling before many other growers because he “wanted to be proactive because we assumed that eventually, as with other states, the government would begin regulating (runoff). So our preference was to deal with the issue upfront, on our terms.”
Chlorine is the nursery’s treatment of choice because it was one of the only options available at the time.
The nursery’s container production has a tail water recovery basin that captures irrigation runoff. For the last 20 years, it has utilized a vacuum system where workers manually adjust the concentration of chlorine treatment based on experience and using regulators that monitor free chlorine. The chlorine has 15-20 seconds of dwell time before it is filtered and irrigated, and Ed was looking for an instantaneous reaction when he chose chlorine.
“It’s a very simple and low investment system and proves to be very cost effective,” he says. “Back then it was essentially the only option available but even as time has gone on, and other systems and options became available, we still find that this works out to be the best for us in terms of effectiveness, investment cost, operating cost, etc.”
This system worked well but was not large enough to meet their current demand.
Updating chlorine disinfection
“As time has gone on, our needs in terms of irrigation have increased. We wanted to do a little better job in terms of the effectiveness of the chlorination, we were looking to automate our irrigation system, and one of the areas that we wanted to address is that with chlorination, you need contact time. In the case of chlorination, the shorter the dwell time the higher concentration of chlorine necessary in order to take care of any pathogens that might be present,” Ed explains.
As of spring 2014, the operation began using an updated chlorine treatment system, which is completely automated and increases the nursery’s pump capacity to 7,000-8,000 gallons to address its increased water consumption. Runoff is still collected in a tail water recovery system, but takes a new route. It is pumped from the first basin, treated with varying rates of chlorine gas based on oxidation-reduction potential (ORP) sensors, and moved to a new basin with a polypropylene liner and a clean environment. Lee Rain Inc. handled the contract work for the new system.
“With the expansion of our irrigation feeds, we will have increased our capacity in terms of available water, but we’re also going to be able to treat the water as we transfer it from the primary tail water recovery basin over to a new recycled basin. By treating the irrigation water as we transfer it, we will then have it in a holding area, we can cut back on our injection rate because we have considerably longer dwell time. It’s going to be sitting in that new basin for an extended period of time... so it has greater time for reaction with chlorine to disinfect the water,” Ed explains.
The older system monitored free chlorine to determine what effective rate was needed to get the job done.
“As time has gone on, our thinking has evolved to using ORP as a more accurate measure of what’s needed to disinfect the water. This system will be automated- the sensors will measure ORP and if we need more (chlorine) because of the biological load, bacteria presence, algae, silt, etc., it will automatically boost the rate of injection so that the water is treated to the level that we want,” he says.
He anticipates higher efficiency and greater return on investment with the new system, which is automated for safety and convenience.
During the redesign, Ed considered a couple other disinfection options. Ozone treatment is very effective, but it was too costly to filter the nursery’s water down to the necessary level. Another option is ultraviolet light, but the nursery could not use that process because of the silt in the runoff from its field production and neighbors. Ed is pleased with the final product and believes that “with this new system we have a chance to start new and try some different things, automate the process and probably have a little more effective result in terms of disinfection.”
Weighing the costs and benefits
The initial investment was made 20 years ago, but a similar system would cost about $85,000 to install today.
“Looking back, this was pretty inexpensive. It involved the regulators, injector, some manifold piping, etc. Our annual maintenance costs include changing the chlorine cylinders each week, which comes out to around $0.10-$0.15 per 1,000 gallons,” Ed recalls.
The new system required an investment of more than $1 million to construct and line the new basin, add filtration, install a new pumping system, and enlarge the irrigation main.
Chlorine disinfection can pose several challenges in tail water recovery systems. Control release fertilizer could be antagonistic to the chlorine when both are used at the same time, although the nursery has never experienced this problem. The new system will minimize the potential for this antagonism because the chlorine treatment takes place long before irrigation. This chlorine injection used to be at a high concentration to ensure that the last greenhouse received disinfected water, which could potentially produce phytotoxicity to the first plants. This is no longer an issue because the chlorine treatment has a longer dwell time, requiring weaker treatment.
Although the new system required a significant capital investment, Ed is anticipating significant benefits. Unfortunately, these may not translate into immediate economic returns. The operation already recycles two-thirds of its irrigation water, and this new system will likely increase that rate. The new system will also create a private reservoir that they can draw on without harming natural water bodies nearby. It should reduce chlorine costs because of longer dwell time, requiring weaker chlorine treatment, and the nursery will save the energy of pumping up water from wells. Additionally, with the new system the nursery has two shots of irrigation: one at 4:30 a.m., which will already be complete by the time employees come in. This will decrease interference with work and production. There will also be less of a chance of having to water in the afternoon so foliage can go into the night dry, thus minimizing disease issues.
Ed recommends the use of chlorine disinfection because it is cost effective, has low initial investment and annual costs, and is safe and reliable. Water disinfection has several advantages.
“With one crop loss we could lose 10 times what it might cost to install and operate a system for a year. It’s good insurance, works out well, and is a small premium in terms of what it ultimately prevents,” he says. “We’ve never had an issue with phytotoxicity with plants or with disease, so the bottom line is, it has served us well.”
For more: www.overdevestnurseries.com
Latest from Greenhouse Management
- Showing up at your horticulture business as your whole self
- Leading women of Greenhouse Management
- Leading Women of Horticulture: Katie Dubow, Garden Media Group, and Aubry Field, Lizzy Blossom
- USDA fires experts on invasive pests, including Asian citrus psyllid, chilli thrips
- Farwest Show calls for 2025 New Varieties Showcase entries
- Leading Women of Horticulture: Arden Pontasch, North Creek Nurseries
- Leading Women of Horticulture: Emily Showalter, Willoway Nurseries
- Leading Women of Horticulture: Anna Ball, Ball Hort, and Terri McEnaney, Bailey Nurseries