Labor is the leading cost in producing plants, meaning it is important to look for ways labor costs can be reduced. In recent years, the greatest advances in greenhouse technology have taken place in reducing the labor needed to grow plants. Even small growers can now choose from a selection of good equipment.

New equipment is continually being introduced by manufacturers and suppliers. Just attend one trade show and you will see a wide variety of devices, from precision seeders and automatic transplanters to plant handling equipment to environment control systems. The many alternatives frequently make the selection a difficult and time-consuming process that is often put off until tomorrow. On the other hand, the benefits of utilizing some of this equipment can produce immediate cost reduction and improve plant quality.
The following factors should be considered when deciding if this is the right time to purchase equipment:
Reduction in management time
Growers spend lots of time making routine decisions. Do the plants need to be watered? Should the vents be opened? Is it time for the lights to be turned on? Simple, low-cost devices, such as an irrigation controller, step controller or a time clock can make these decisions for you. Keep track of the time you spend each day at these chores and then select a device for automation.
Task labor reduction
Whether you have 10,000 square feet or 10 acres of growing space, there is equipment that will reduce labor and improve efficiency. The areas of automatic control and material handling equipment should be considered first. Carts, roller conveyors, a pallet truck and a small tractor with a bucket loader are items that can be used by small or large operations, are relatively low cost and have use throughout the year.
Availability of skilled labor
In some parts of the country, this is a limiting factor to the expansion of a business. There is a lot of competition for the people that have training and experience in the industry. Other types of businesses frequently offer better working conditions or greater benefits. An operation that is mechanized will attract workers because future employees can see that less hand labor is required.
Heavy tasks
Lifting and carrying heavy objects is tiring and reduces productivity. Where possible, materials heavier than 50 pounds should be moved mechanically. Examples include a) using carts or wagons to move bales of growing mix, filled containers or cartons of pots; b) installing a loading dock to load carts onto the truck for shipment.
Repetitive tasks
Generally, repetitive, tedious or time-consuming jobs should be considered the first to be mechanized. Installing a flat or pot filler is a good example of this type of automation. Besides doubling or tripling the output per hour, the containers are more uniformly and evenly filled than by hand.
Peak work periods
Mechanization can be used to help you through the peak periods. Seasonal help is frequently difficult to find and train and the extra paperwork adds to an already overloaded work schedule. An automatic transplanter can reduce the need for extra help and can help to refill empty growing space more rapidly.
Lower production costs
Letting machinery replace some of your labor force can result in a lower cost per plant. A piece of machinery, such as the recently developed plant spacing robot, can work for long periods of time without stopping for a coffee break. An analysis of the time that will be saved and the unit cost needs to be made. Good records on the time required to do certain tasks is helpful in determining which jobs should be mechanized. Care should also be taken to see that bottlenecks will not be created.

Improved quality
Equipment can often be used to improve the quality of the plants that are produced. A precision seeder for plug trays can accurately place one or more seeds per cell at a constant depth. This will result in uniform seedlings that are ready for transplanting at the same time. Adding a boom watering system that applies the same amount of water to each cell will do a more uniform job than watering by hand.
Reasonable payback period
The payback period is the time required for the savings from a new piece of equipment to recover the initial cost. It is obtained by dividing the total capital investment, including installation, by the annual cost savings. A payback period of less than three years is excellent, three to five years is good. The cost savings can be estimated from the projected labor reduction less the equipment operating cost.
Once you have decided that it is time to upgrade your operation with automated equipment, take time to evaluate the many alternatives that are available. Visit other growers, attend trade shows, talk with equipment vendors and read articles on what others have done that can be applied to your own business.
Get curated news on YOUR industry.
Enter your email to receive our newsletters.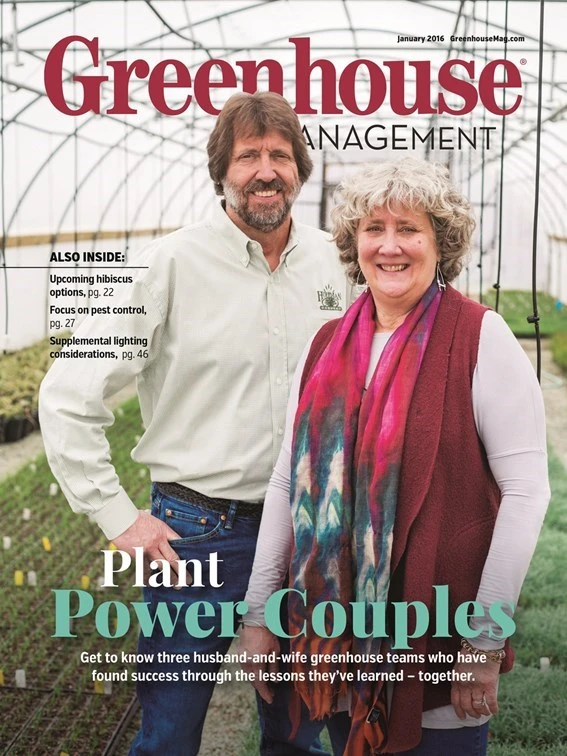
Explore the January 2016 Issue
Check out more from this issue and find your next story to read.
Latest from Greenhouse Management
- The Growth Industry Episode 3: Across the Pond with Neville Stein
- Trends: Proven Winners 2025 perennial survey shows strong demand
- Online registration opens for the 2025 Farwest Show
- Green Gear: Battery-powered backpack sprayer and a hoodie
- Sustainabloom launches Wholesale Nickel Program to support floriculture sustainability
- Be the source
- pH Helpers
- Society of American Florists accepting entries for 2025 Marketer of the Year Contest