
Lloyd Traven, founder of Peace Tree Farm in Kintnersville, Pennsylvania, is preparing for his retirement after running the specialized and distinctive operation with his wife Candy for the past 40 years. He’s been making some big investments, but not in post-retirement purchases like a boat or a mountain home. Instead, he’s been investing in greenhouse upgrades as part of the succession plan when his son Alex takes over the business.
“I’ve got a five-year plan to retire, then Alex will own a majority stake and take over the business,” Traven explains. “Over the last few years, it’s been my job to get this company to a place where Alex doesn’t have to be frantic about infrastructure or business development, and he can run on this momentum while he gets his feet completely under him and puts his final team together. I’m not in the greenhouse working on production anymore. I’m all about the 30,000-foot view now.”
In terms of infrastructure, he’s completed an impressive list of upgrades for the 50,000-square-foot greenhouse operation, from computer control systems to LEDs and solar power to a hydrogen peroxide generator.
“We did a top-to-bottom, 100% replacement this year of our Argus environmental control system. We had the oldest fully operational Argus system that they were aware of anywhere. Ours dated back to 1986, and they were stunned that we had the original main controller. All the relays and expansion boards were there,” he describes. “We’d expanded it several times over the years, but we had the old legacy software. They were blown away.”
Traven and Argus worked together to add more functions to the system, including a boiler alarm, LED lighting and dimming capability, as well as daily light integral programs.
“Now there are a lot of things we added that we didn’t have full control over for the last 30 or 40 years,” he adds.
Traven also replaced the microclimate heating system in the upper range. The original system was from the 1980s. And they’re rebuilding greenhouse benches as an ongoing project.
About four years ago, Traven installed an on-site hydrogen peroxide generation system for disinfection and disease control. The Danish system, HPNow, uses water, oxygen and electricity to produce low-concentration hydrogen peroxide.
“Since we’ve started using that system, there’s no algae problems anymore. We don’t have to clean the booms or filters as often as we used to. There are fewer fungus gnats. The benches are cleaner,” he explains.
It’s also cut down on pythium issues that used to be common during summer production.
“We would have a period every summer — and we do a lot of lavender propagation in the summer — that once the water temperature in the ebb and flood tanks hit 78 or 80 degrees, we’d have a sudden outbreak of pythium,” he says. “And since we’re certified organic — we have to grow all the crops organically — we don’t have all the chemicals available to us for pythium control. Once we installed this system, we don’t see those issues at that level anymore. It’s a really slick system.”
Big on basil
Herbs are big business at Peace Tree Farm, including an exclusive program they developed for Wegmans, a regional supermarket chain. Traven and his team are shipping herbs to the grocer’s distribution center for sale in stores throughout Pennsylvania, New Jersey, the New York City metro area and parts of Delaware and Maryland twice a week, 52 weeks a year.
“That’s changed everything we do. That’s why we keep people 52 weeks a year. We no longer depend on spring sales to keep us going,” he says.
The program consists of nine herbs: basil, rosemary, parsley, sage, thyme, dill, mint, cilantro and chive.
Recently, Peace Tree Farm updated its Fluence LED system. Traven says the use of LEDs has positively impacted the herb program. With the help of researchers at Project LAMP (Lighting Approaches to Maximize Profits), he learned the wavelengths of LEDs are important to the physiologic and morphologic growth of the plants.

“We also found out blue light keeps plants shorter. So, if I was growing cut basil, I would want red light, because it makes them get big and long with a lot of mass,” he explains. “Well, ours are sold live in a sleeve in the produce department. We needed something that makes them shorter and denser. When we were looking at LEDs, it turns out the Fluence VYPRs we were installing have a very high percentage of blue wavelength. When we started lighting with LEDs, there was an instantaneous change in the plant growth.”
He’s also learned that using photoperiod night interruption and blue light wavelength “can dramatically slow down sporulation of basil downy mildew.”
Because of this year-round program, the herbs have to look the same during Christmas week as they look on the Fourth of July.
“Between the Argus control system, the lights, the irrigation, the feed and the disinfection system, we have figured out how to grow this crop so it looks the same year-round,” he says.
The Wegmans herb program also precipitated the eventual purchase of a new transplanter and the possibility of buying a new pot dispenser. The automation he currently uses and the machines he’s considering directly support the greenhouse production crews.
“We don’t have trouble finding people,” Traven says. “We pay well; we pay for their medical; we offer profit sharing. And we really try for a 40-hour week, and they get two days a week off.”
Read the rest of Greenhouse Insider:
Sponsor Letter: A welcome message from the NGMA president
Upgrades: Prioritizing upgrades
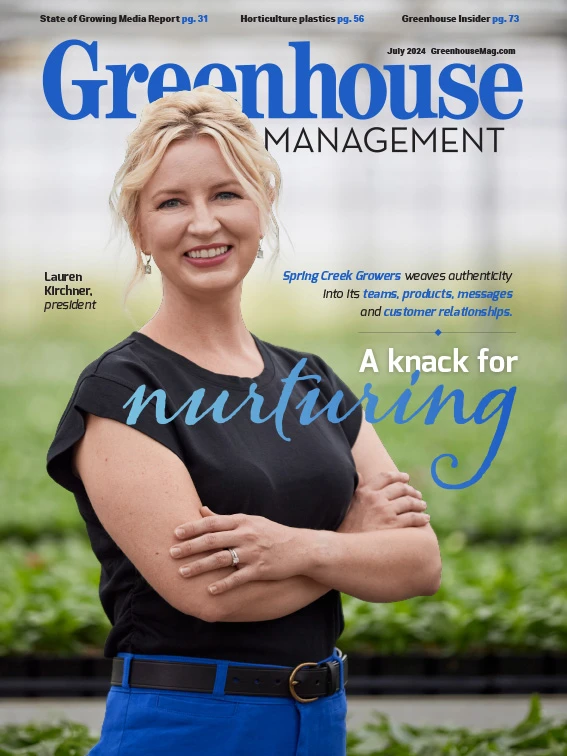
Explore the July 2024 Issue
Check out more from this issue and find your next story to read.
Latest from Greenhouse Management
- Flexible fungicides
- Super Charged Moon Juice from Moon Valley Nurseries now available nationally
- 2025 Proven Winners Horticulture Scholarship applications now open
- How to improve inventory and shipping management in the greenhouse
- Leading Women of Horticulture: Anna Ball, Ball Hort, and Terri McEnaney, Bailey Nurseries
- GM CEA HERB Part 2: A guide to increasing the sowing density of culinary herbs
- GM CEA HERB Part 1: Best practices for producing culinary herbs in controlled environments
- USDA fires experts on invasive pests, including Asian citrus psyllid, chilli thrips