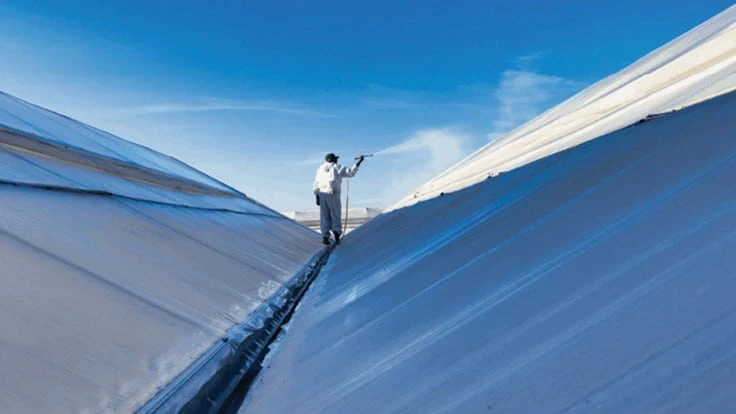

Many things can go horribly wrong in a cultivation operation. With numerous variables to account for, a grower must anticipate encountering a multitude of everyday problems, as well as unexpected events and surprises. A grower must be able to not only anticipate problems, but also be able to troubleshoot/diagnose a given problem rapidly to appropriately solve it before it becomes a bigger issue.
Whether you are troubleshooting problems or simply being appropriately proactive, here are common issues you may encounter in a greenhouse and tips on how to solve them.
Troubleshooting common greenhouse problems
One of the many advantages a greenhouse offers is that it utilizes both supplemental lighting as well as natural sunlight (when available). Many high-value crops, ranging from ornamental flowers to tomatoes, are produced commercially in greenhouses for just that reason. Greenhouse production also allows for multiple crop cycles per year, similar to indoor production.
But, like in any controlled environment, potential problem areas exist in greenhouses that must be monitored and proactively addressed. Losing control of your environment can lead to cultivation headaches ranging from poor airflow to extreme temperatures, as well as opportunities for diseases, such as waterborne viruses like Pythium.
Common problem No. 1: Air filtration
Typically, greenhouses are not sealed environments (such as hybrid facilities with glass roofs), but rather forced air/positive pressure environments. This means that they should be equipped with air filtration and sterilization capabilities on both the intake air and the exhausted air. The intake air is filtered and sterilized for pest and disease prevention. A proper ventilation system also allows a grower to control vapor pressure deficit (VPD) to some degree.
A common issue that can arise in these systems is clogged air filters decreasing airflow. Greenhouse operators can use wind speed sensors to determine if airflow is reduced. Luckily, larger automated ventilation systems often come with sensors that alert growers when it’s time to swap out filters. That said, air filters should be inspected periodically and changed as required. Location of the operation will determine how often filters need to be changed — don’t rely solely on manufacturer recommendations on when to change the filters because each situation is different.
_fmt.png)
Common problem No. 2: Greenhouse temperature swings
The summer of 2020 delivered record temperatures to all of California, including both the southern and northern regions. In Southern California, Death Valley reached 130 degrees, which is the hottest recorded in nearly 90 years. In other parts of the state, radiant temperatures (which is defined as net radiant heat gain or heat loss, and is different than ambient temperature), amplified by wildfires and smoke, reached 120 degrees in September.
With such extreme environmental temperatures, one possible recourse that doesn’t require increasing air conditioning capacity is to use either shade cloth or a greenhouse whitewash to control excessively hot environmental conditions, both ambient temperatures as well as radiant temperature.
A whitewash consists of coating the greenhouse glass with one or more coats of non-permanent, white, washable paint. Operations that use automated glass cleaning machines can fill those systems with whitewash instead of a cleaning solution. Some larger scale operations can also apply whitewash by helicopter.
While the goal of whitewashing is to reduce radiant temperatures, it also impacts the amount of photosynthetically active radiation (PAR) light reaching the crop. If light levels drop below target levels, consider washing off the paint and applying fewer coats or a more diluted paint mix. Ultimately, growers must weigh the risks of heat exposure against loss of light when determining how much light and radiant heat they want to take out of the greenhouse.
In colder climates, a heating system is a must. An inefficient heating system can be expensive at best and dangerous at worst. If growers are experiencing cold spots in the greenhouse or lower temperatures overall, and inspections for leaks and gaps where cold air could be infiltrating have been conducted, the heating system might be at fault. Early spring is the best time to thoroughly inspect and repair any heating systems. All heating equipment and thermostats should be serviced and inspected prior to wintertime use—it’s better to prevent a problem in the fall than respond to one in the dead of winter.
Common problem No.3: Watering and fertigation systems
After harvest and in between crop cycles is the perfect time to troubleshoot and repair/replace any and all worn out, broken or defective irrigation or fertigation equipment.
Measure the flow rate to determine whether a fertigation system is functioning properly. Ideally, growers will have a baseline that was first measured after the system was installed against which to compare. Diminished flow could be a sign of a clogged filter, dripper, or dose meters. Wilting plants are an obvious sign of a potential irrigation problem. For automated irrigation systems, however, a computer should tell growers there’s a problem before it is even noticeable in the plants.
"Thinking proactively about the potential problems that a greenhouse can face is going to be the difference between a humming operation and a wasted investment."
If flow rate is reduced, growers can flush the irrigation system with a hydrogen peroxide and water mix. Use a mix of up to five parts water to one part hydrogen peroxide when flushing systems. For preventative treatment, this can be done between each harvest.
Also, growers or production team members should verify each dripper by hand to make sure there are no clogs that were not unplugged by the peroxide cleaning solution.
Common problem No. 4: Constant mold and pest problems
Besides the overall function of the watering/fertigation system, close attention to disinfection is a major priority. Pythium and other vectors for disease can be transmitted by contaminated irrigation equipment and/or contaminated water. If growers are experiencing continued Pythium problems over multiple crop cycles, consider decontaminating the entire watering system, including lines and the water tank (if a water tank is used). Again, in ideal situations, this should be done after each harvest.
The same water and hydrogen peroxide mix can be used to disinfect water tanks and irrigation lines. Growers should schedule a water tank disinfection after a watering cycle, when the tank will be mostly empty, and fill the tank with the 20% concentrated solution.
If the watering system is sanitized but issues persist, it might be time to deep clean the greenhouse.
Common problem No. 5: EC/nutrient level spikes
If there are noticeable spikes in nutrient solution electrical conductivity (EC) (which growers would notice in runoff testing) but levels are normal at the solution source, consider examining the fertigation lines, as fertilizer salts may have accumulated. Also, thoroughly inspect nutrient application equipment such as injectors for EC and flow rate to prevent under/over fertilization issues from metastasizing and causing nutrient application problems.
Common problem No. 6: Crops drying out
If crops seem consistently dehydrated, inspect all related electronic controls responsible for watering, timing and cycles for clogs or mechanical failures to prevent possible over/under watering or not watering on time.
Thinking proactively about the potential problems that a greenhouse can face, and planning on how to avoid or address those problems, is going to be the difference between a humming operation and a wasted investment. With that in mind, develop SOPs that not only direct team members on how to do things right, but what to do when things go wrong.
(Editor's Note: this article was originally published in the November 2020 issue of Cannabis Business Times Magazine)

Explore the March 2021 Issue
Check out more from this issue and find your next story to read.
Latest from Greenhouse Management
- The Growth Industry Episode 3: Across the Pond with Neville Stein
- Trends: Proven Winners 2025 perennial survey shows strong demand
- Online registration opens for the 2025 Farwest Show
- Green Gear: Battery-powered backpack sprayer and a hoodie
- Sustainabloom launches Wholesale Nickel Program to support floriculture sustainability
- Be the source
- pH Helpers
- Society of American Florists accepting entries for 2025 Marketer of the Year Contest