
Although it may sound pessimistic, one constant cannabis companies must plan for is technology failures.
It’s inevitable that something will go wrong when working with live plants, multiple inputs and various technologies to keep them thriving, says Jim Mitchell, an industry consultant. And rather than viewing it as pessimistic, he frames it differently: Planning to fail means you’re prepared and are more likely to survive whatever crisis comes up.
“We often forget about how things fail, but they will. Everything fails at some point in its life,” Mitchell says. “The question is, will it take out your company if it does?”
Among the most important systems in cannabis cultivation are those that regulate heating, ventilation and air conditioning, and related controls. CBT asked three industry experts about the most common problems they see with managing HVAC in cannabis cultivation, troubleshooting tips and what prevention strategies can help stave off trouble in the first place.
Andrew Lange, president, Ascendant Management
Problem: Inability to hit humidity control targets
Possible Solution: Check your sensor locations and move them within the plant canopy.
“A common issue I see is people are unable to hit humidity targets, even when dehumidification equipment is properly sized, because their sensors are in incorrect locations,” Lange says. Some cultivators mount sensors on the walls surrounding the canopy, but that can be several feet away from the actual cannabis, and the readings may not represent the climate the plants are actually experiencing. To check this, use a handheld humidity meter and check at the canopy level and where the sensor is currently mounted and compare, Lange says.
“My suggestion is to mount your sensors in the canopy where you want the actual readings, right next to the plants,” he says. He suggests suspending the sensors from the ceiling using a chain and adjusting the device as the plants grow, targeting either right at the top of the canopy or as close to the top of the canopy as possible. Another solution is to affix the meter on a post that again can be raised as plants grow. “Have your grow team move it up to where it needs to be inside the canopy; that gives you your most accurate reading each time.”
Problem: Thermal stratification
Possible Solution: Add ceiling-mounted fans to get vertical air movement.
“Destratification of air is incredibly important, and it’s something that often gets overlooked,” Lange says. “[The] vertical air movement, where we are moving air up from the floor and pushing it up against the ceiling, does two things: one, it elevates CO2 for us and helps bring that CO2 off the floor where it’s not being used, and [two,] it helps reduce hot spots in the room.” This helps equalize temperatures and bring CO2 up to where it can be used in the canopy.
Dr. Nadia Sabeh, Ph.d., president, Dr. Greenhouse
Problem: Condensation on the walls
Possible Solutions: Check the building envelope for cracks or holes, and seal them; create buffers around entrances into the production area.
Gaps, holes, cracks and other building infiltration issues can lead to climate management control problems, no matter how good your equipment and technology are, Sabeh says. If there are humidity control issues, one place she typically looks first is the ceiling or roof to check for holes or cracks causing outside air to come in. One problematic area is around ductwork, she says.
“What’s causing the humidity control issues? Well, they didn’t seal up the hole that the duct is coming through on the roof, and so it’s really cold here on the ceiling in the winter,” Sabeh says. “And so it’s not necessarily that rain is coming through, but because of that cold temperature up at the roof or if it’s a ceiling, you have this humid room and it's condensing. And then they seal it up, and it’s all good.” Sabeh says an infrared camera can reveal pockets of cool and hot air in a room to help find gaps that are not easily seen.
Another place outside air can travel in is from entrances or delivery areas where there are no dividers between the outside and the production space. “It could even be as simple as an air curtain, but there needs to be something that creates a separation because when you open that door, you lose control of that interior space,” Sabeh says. “So you want to create some sort of buffer.” Another way to prevent control issues is to not allow deliveries directly into the production area.
Problem: HVAC equipment cycles off automatically, causing fluctuations in temperature and humidity.
Possible Solutions: Fix communication between sensors and automation system; check manufacturer for instructions on use; check system size; invest in more sensors.
“We have one project now, and they can’t figure out why the equipment cycles on and off every 90 minutes. And you can just see these spikes, and for five minutes, the equipment is off. I find that a lot of the troubleshooting issues around HVAC is about control,” Sabeh says. “This is really an area that needs more attention.”
When equipment cycles off and on, Sabeh says one potential reason is that the HVAC system is too large for the space. “The classic case of oversized equipment is that it cycles on and off, which not only causes wear and tear on the equipment, but you’re going to see a bunch of fluctuations in temperature and humidity as that unit is turning off and on.” Humidity control issues also can be a sign of undersized equipment, she says. Often problems stem from a lack of training on how to use the equipment, however. Sabeh recommends working with suppliers that will provide information and training at the outset.
Another area to check is sensors; it might be that there are not enough sensors to provide accurate information to the environmental control systems. Although it can be expensive, Sabeh says, investing in sensors and monitoring systems that track and store historical data is essential to successfully troubleshooting HVAC problems.
“The more data, the better,” Sabeh says. “Same with sensors. It’s always that sensor you wish you had.”
Jim Mitchell, industry consultant
Problem: Unprepared for component or system failures
Possible Solution: Keep backup equipment on hand and test it; implement a “redundancy strategy.”
Mitchell says that cultivators often store extra HVAC parts so they can replace primary components quickly or switch to backup units, but it’s also important to test backup equipment, include components as part of a regular maintenance program and replace parts regularly.
“You don’t want a surprise when your primary goes down and you go to your backup and no one has checked it,” Mitchell says, adding that the same goes for filtration systems, coils, fan belts, motors, and other key parts.
But, what if the electricity that powers the HVAC system fails?
In his experience as a consultant to cannabis cultivators, he’s seen the worst happen due to factors out of the company’s control, like power outages or, in one particularly unlucky case, when a natural gas supplier in Michigan had an equipment failure at its plant, shutting down systems for multiple hours in the middle of February.
“I’ve consulted with quite a few companies on how to kind of harden their HVAC system, having the backup generator is critical but so is having backup fuel for the backup generator,” he says. “It’s just a matter of going through that list of things that are critical to your operation and saying, ‘well, where do we need to have this layer of redundancy or backup that goes into it?’”
Mitchell says planning for a cultivation crisis is similar to fire drill training — what is the rescue plan if there is a catastrophic situation in your growing operation?
Developing contracts and relationships with suppliers to provide “rescue units” that supply inputs like heat, water or air conditioning is key, he says.
“Those are all critical to the life of the plant,” Mitchell says, and the electricity or water lines that supply those inputs also come into play. “So ... identify [what’s critical to the life of the plant], and rank them as to how important they are on a scale of one to 10.”
Problem: System warnings don’t seem to match up with conditions in room.
Possible Solution: Check labels and wiring when systems are installed.
“You have to make sure your control system is set up and was installed correctly,” Mitchell says. Because of crossed wires, pipes or mislabeled controls, he’s seen situations where alarms are indicating a problem in one flowering room where the issue is actually occurring in the other. “I can’t stress enough [the importance of] conditioning your system when it’s brand new and going over everything with a fine-tooth comb one at a time to make sure that all your systems are installed correctly and are working to specifications.”
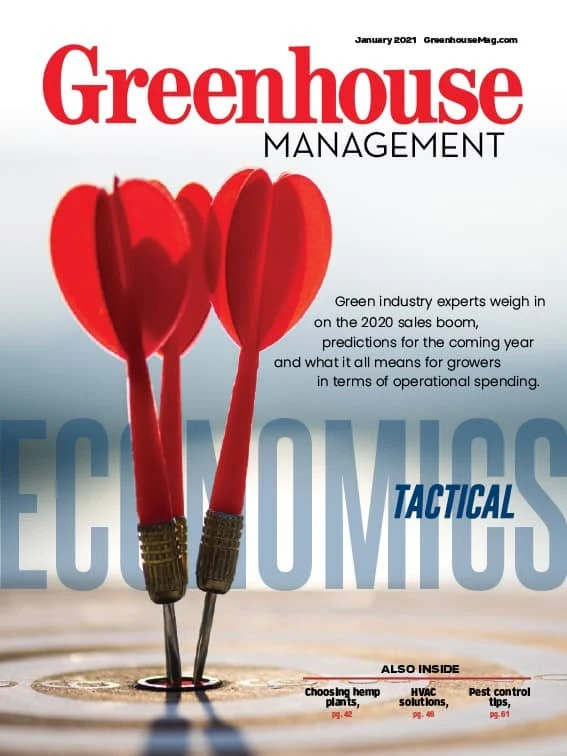
Explore the January 2021 Issue
Check out more from this issue and find your next story to read.
Latest from Greenhouse Management
- The HC Companies, Classic Home & Garden merge as Growscape
- Eason Horticultural Resources will now officially be known as EHR
- BioWorks receives EPA approval for new biological insecticide for thrips, aphids, whiteflies
- ScottsMiracle-Gro transfers cannabis subsidiary to focus on core lawn and garden business
- Ellen Mackenbach-Lakeman appointed new CEO of Dümmen Orange
- Southern Garden Tour sets 2025 dates for trial garden open houses
- Belgian thermal screen manufacturer Phormium launches Noctis Thermo
- New book explores plants that thrive in Rocky Mountains