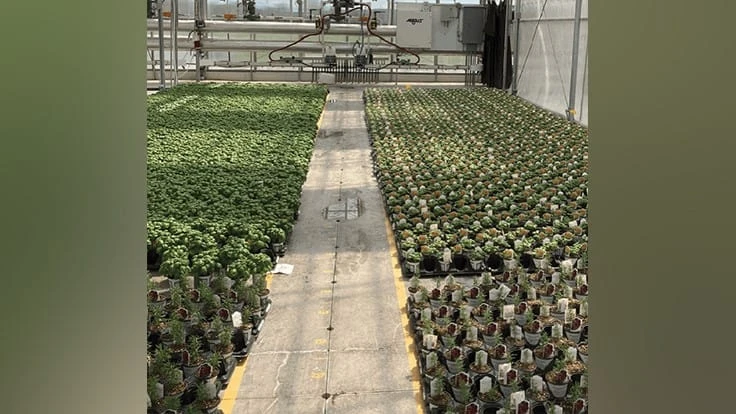

Over the last several years, environmental control technologies available to growers have changed drastically. The interfaces, or controllers, have become more modern and useable. The systems themselves have become more customizable, too. The ability to chart out and visualize production data and trends has increased in value to growers, too, as more growers want to use more and more data to grow successfully. And, particularly for larger operations, this amount of data is necessary to growing efficiently and not overworking your crew.
Below, two experts — Julie Dean, the vice president of Wadsworth Controls, and Brian Debrot, a business development representative from Argus Controls — answer questions about environmental control systems. For more insight from both experts, visit greenhousemag.com
Editor’s note: Julie Dean answered the questions with the assistance of the Wadsworth engineering and sales team. The answers were edited for style and clarity.
Greenhouse Management: If a medium to large sized operation has an environmental control system that is outdated, or doesn’t have one at all, why should they look into getting one?
Julie Dean: It’s all about leaving money on the table. The older systems just aren’t as smart as today’s controllers that offer a well-managed uniform climate resulting in a more robust crop, often produced in a shorter time. Control systems address labor shortages by automating morning and nighttime routines, controlling temperature, humidity and irrigation. Automating your greenhouse creates a more stable climate, with less energy and water consumption. Using on/off thermostats to control the greenhouse creates an ongoing battle between heating and cooling that causes wear and tear on your equipment and can result in heating and cooling the greenhouse simultaneously.
Look toward the future — a greenhouse with leading technology attracts a savvier workforce, and that means forward momentum for your grow.
Brian Debrot: In a larger sized facility, it really just comes down to efficiency, right? You have cost efficiencies for optimization, for starters. If you’re automating at all, one of the big things with automating is the ability to collect data. And especially on a large scale, that can be massively beneficial.
If you can take things like sensor readings and understand exactly what your crops went through and what kind of effect that had - be it higher yield, better quality or something suboptimal — you can now take that, analyze it and apply it to make your facility a better place for your plants. Now, this all allows cultivators, horticulturists, growers and greenhouse crews to direct their energy towards other things. If you can automate your system for what you want your set points to be for a crop throughout the day — and that can apply to temperature, humidity, something like C02 depending on what crop it is — you’re automating all of that and you can jump on the system and see in real time what’s happening in the facility. The controls are interacting with everything that controls those variables and making sure everything is staying at set points. Growers still want to and will need to walk the site, but what’s removed is the need to get into the weeds of it all, so to speak.

GM: How much space can a system cover and what options are available on the market?
JD: Greenhouse management is typically measured in zones. This is often an entire greenhouse, but it can be a single aquaponic tank.
Wadsworth’s controllers typically manage high-end residential projects through large greenhouse ranges. The STEP Up and EnviroSTEP controls each manage a single zone. VersiSTEP is a multi-zone control that can manage 2-4 environments. Seed 16 is a good controller for smaller operations that have, along with standard heating and cooling equipment, lighting and sensors. It includes a control and 16 outputs, is expandable and can do everything the standard Seed control can do. The entry level price makes it a good choice for those who are looking to enlarge operations in the future. The standard Seed control can control as many environments as needed and manage any equipment.

GM: What kind of information does a grower need to provide to get a proper estimate and recommendation when installing a new environmental control system?
BD: We need the grower’s mechanical engineering and plumbing designs. If they have information on what the equipment is in the greenhouse — it could be the light, the irrigation system, heat, etc. — that’s all necessary. Once we have all that information, we come together and build out a plan and see what we have from Argus that will interface with that equipment, whether it’s a direct electrical interface. Or, let’s say there’s some sophisticated HVAC units that have their own “brains,” then we can interface via a protocol language to provide supervisory control. So, as we develop and understand that, and working with the growing team to see how many different zones they want and how they want to visually see the data and how they want to act, we can build it from there. From a basic standpoint, though, it has to start with the mechanical and plumbing designs. For irrigation specifically, understanding cost limits is needed to put together a plan.
GM: How much training is required to properly use a modern environmental control system? And how can a supplier help with training?
JD: The level of training depends on the controller and the complexity of the system. When we designed the Seed control, we made it intuitive and highly accessible but with deep functionality. User ease was an important focus whether the user was someone who had a grant for their school greenhouse, a homeowner, a commercial grower with years of experience, a cannabis facility, or a research center. Whoever walks up to the controller understands the home screen and easily navigates to a specific zone’s equipment to see what equipment is engaged and why.
Wadsworth offers virtual and onsite training. Since our training includes commissioning the controls, software, weather station and testing equipment engagement, along with training the various levels of staff, it’s a powerful tool for a successful startup. We control a wide variety of environments, from herpetariums, aviaries and butterfly pavilions, to floriculture, aquaponic and hydroponic food production, cannabis and botanical gardens. Each facility has specific needs and equipment, and while the manager of the facility has the knowledge regarding what the perfect climate is, they may need support in understanding how to create it.
BD: It can [get complicated]. We always do on-sight training whenever we commission with a greenhouse. Whenever we finish an install, we send our team to the site to confirm it’s been done right, to make sure it’s covering every single control point and that it’s doing what it’s supposed to do for the grower. And then we do training to get the growing teams comfortable and confident in using the Argus system. It’s a robust training. But because the Argus system can be so deep — growers can start writing their own equations into it, they can define their own sequence of operations — we have supplemental training beyond that which we call boot camp. This gets people really honed in on our system in terms of being able to write their own equations, and being able to do a lot more of the in-depth stuff that isn’t typical for a growing or cultivation team to need to just get up and running and seeing some benefits from the system. It’s what can help operations hit the next level.

Explore the March 2021 Issue
Check out more from this issue and find your next story to read.
Latest from Greenhouse Management
- North Carolina Nursery & Landscape Association announces new executive vice president
- Plant Development Services, Inc. unveils plant varieties debuting in 2025
- Promo kit available to celebrate first National Wave Day on May 3
- Applications now open for American Floral Endowment graduate scholarships
- Endless Summer Hydrangeas celebrates 20 years with community plantings
- Invest in silver
- Garden Center magazine announces dates for 2025 Garden Center Conference & Expo
- USDA launches $2 billion in aid for floriculture growers