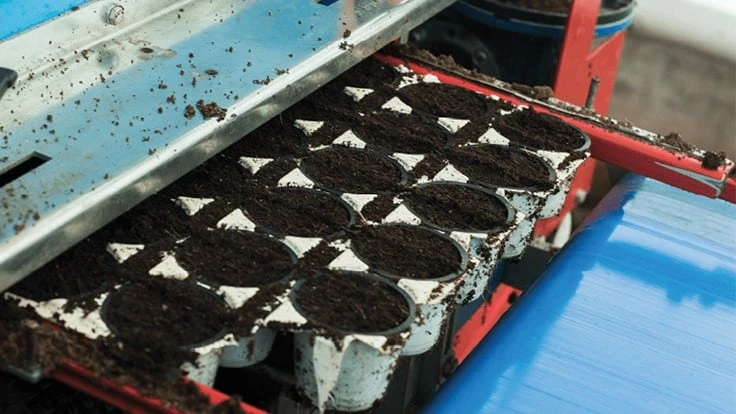

Tray fillers were first developed in the 1960s to replace the large amount of labor needed to fill growing containers for the expanding market for annual transplants. Labor reduction was as great as 90% as these machines could fill up to 900 flats per hour. Additionally, the uniformity of soil in the tray resulted in more even plant growth and marketability.
Since then, several types of machines have been developed to handle the wide variety of container sizes now used. Many improvements and attachments are available that will unstack and insert pots, return surplus soil to the hopper, compact and level the soil and dibble holes for seeds or plugs.
For most growers, trays are filled with a purchased, pre-prepared growing mix. Container filling should be considered as part of an efficient system that handles the soil from the bag or bale to the time when the tray is planted and ready for moving to the growing area. Handling of trays is expensive, adding 2 to 4 cents to its cost each time a tray is moved.
In addition to the filler, accessory equipment should also be considered part of the system. This can include a soil fluffer or bale breaker, conveyors, transplanting conveyor or automatic transplanter, watering tunnel and tagger. Transport to the growing area is frequently provided by carts or in larger operations, fork trucks or transport trays. For propagation, a seeder could also be included.
The system can be purchased initially or can be assembled over time to spread out the cost. In either case, it is important that the pieces of equipment be matched for speed and size of container to provide a smooth flow and uniformly filled trays. Most manufacturers will design the system and provide matching equipment and layouts that fit the production needs and space that is available.
Types of machines
There are two basic types of container-filling machines. Both are available to fill trays or individual pots. These machines are sized to handle as few as 500 trays or as many as 4,000 trays per hour. Smaller machines are usually operated by a single person placing the tray, filling and then moving it to a cart by hand. Larger machines require multiple workers to handle the faster rate.
One concept usually called a potting machine consists of a hopper on wheels, a soil elevator that lifts the media from the hopper and a horizontal circular chain conveyor. Empty pots are placed in holders on the chain, carried under the elevating conveyor, filled, dibbled and moved to a location where they are either manually or mechanically removed. Transplants can be set as the pot goes by or the containers can be placed on carts or pallets for later planting. Excess soil then falls back into the bin. Most of this type of machine can be converted to fill trays. All operations are timed with a variable-speed drive. At least two people are needed to make the operation efficient. Accessories available to growers include fertilizer dispensers, automatic pot dispensers, multiple pot holders for smaller-size containers and conveyors to supply or remove containers.
Another type of machine is designed to move empty containers under a soil hopper. The hopper capacity is usually 1 – 2 cubic yards and can be filled with a front end loader or belt conveyor. Soil is fed by gravity to the containers that move under the discharge chute. Soil flow rate is controlled by adjusting the discharge gate or by a belt conveyor.
A belt or chain conveyor is used to move the containers under the bin. A variable speed drive, either electric or hydraulic, allows the feed rate to be adjusted for different-size containers. Side guides adjust for the size of container. Feed rates as high as 4,000 flats or 20,000 pots per hour can be achieved.

For certain mixes, some compaction is needed. This is provided by either an adjustable roller or vibrating plate. Excess soil is removed by an angled scraper, rotating brush or air brush, and returned by conveyor to the overhead bin.
Accessories include a dibble, container counter and pot or flat dispenser. Supplying adequate containers to kept the machine operating at full speed and removing the containers after they have been filled requires additional employees or conveyors. These machines are usually operated with three employees.
Special machines based on the above concepts are available to fill large containers, plug trays or with a template to precision-fill multiple small pots.
When purchasing a machine, look for heavy-duty construction, standard parts that can be found locally, easy adjustment for different container sizes and convenient access to controls. Operator safety is important and all guards should be kept in place. Portability is important if the machine is to be moved between greenhouses.
There are several things that can affect production rate. These include:
- Organization of the supply and removal of containers — keep material close by.
- Ease of separating and preparing trays
- Skill and knowledge of operators — most manufacturers have videos to aid in training.
- Ease of adjustment or change to different size container
- Growing media that is not uniform, too wet or has large lumps
- Jamming of pot dispenser
- Comfort of operators
- Ease of removal of plugs from supply trays

Sizing the machine
Using the following tables and formula, you can get a reasonable estimate of the number of containers that you need to fill per year to pay for a machine or system:
Information that you will need to know includes:
MC (initial machine cost) — This includes the price of the machine including accessories and auxillary equipment, conveyors, freight charges, installation and setup.
SPB (simple payback) — Simple payback is the amount of time that it takes to recover the initial investment. It doesn’t account for maintenance or inflation. Payback should be less than the useful life of the machine. Most machines are considered to have a five-year useful life but it may be longer due to limited use, quality construction and good maintenance.
CFC (current filling cost) — What is your cost for filling a flat or pot? This can be determined based on the average number of containers that are filled by one person per hour and the cost of the labor to fill them (refer to the tables).
MFC (machine-filling cost) — The cost of filling the same containers using a machine — most manufacturers can give you an estimate based on the design of the machine and grower experience. Usually the manufacturer lists a maximum number, so lowering that value some to account for worker experience, loading the growing mix into the hopper, separating containers, worker breaks, etc., is necessary. Divide the machine rate by the number of operators to get the per-person rate.
Example calculation:
From the table, the cost of handfilling 100 flats/hr at a labor rate of $12/hr is $0.12/flat.
A medium-size basic tray filler without accessory equipment will cost about $15,000 and will fill 1,000 flats/hr with two people (500 flats/person) at a cost of $0.024/flat.
If you would like to get a payback of five years then you would have to fill 31,250 flats/year.

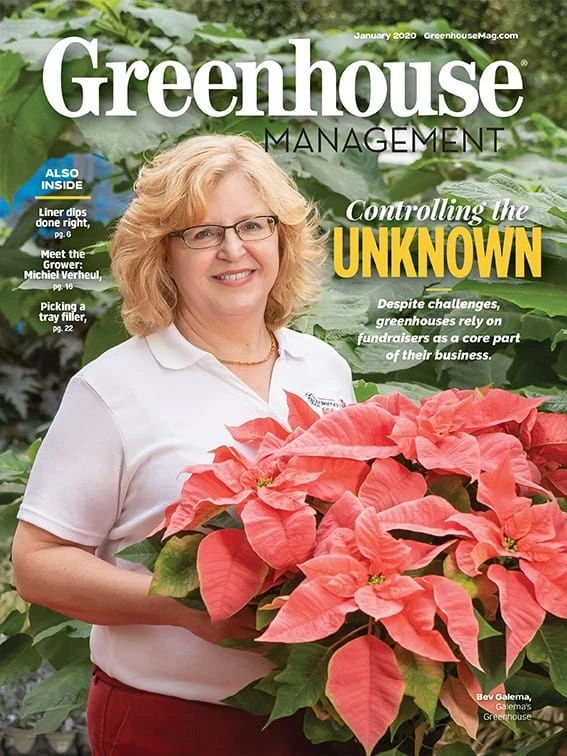
Explore the January 2020 Issue
Check out more from this issue and find your next story to read.
Latest from Greenhouse Management
- North Carolina Nursery & Landscape Association announces new executive vice president
- Plant Development Services, Inc. unveils plant varieties debuting in 2025
- Promo kit available to celebrate first National Wave Day on May 3
- Applications now open for American Floral Endowment graduate scholarships
- Endless Summer Hydrangeas celebrates 20 years with community plantings
- Invest in silver
- Garden Center magazine announces dates for 2025 Garden Center Conference & Expo
- USDA launches $2 billion in aid for floriculture growers